Northwestern University researchers have unveiled a process that could reshape plastic recycling by converting polyethylene terephthalate (PET) using a simple catalyst and the natural moisture found in air. This new method, detailed in a recent Green Chemistry publication, employs a low-cost molybdenum-based catalyst along with activated carbon to break down the bonds in polyethylene terephthalate (PET); the most common polyester plastic, without the need for solvents or harsh chemicals. You can see the published research here:
Malik, N., Li, J., Agarwal, A., Kratish, Y., & Marks, T. J. (2025). Thermodynamically leveraged solventless aerobic deconstruction of polyethylene-terephthalate plastics over a single-site molybdenum-dioxo catalyst. Green Chemistry, 27(9), 2427–2438. https://doi.org/10.1039/D4GC05916F
The process is initiated by heating PET alongside the catalyst mixture, which breaks the long polymer chains into smaller ones. The procedure uses ambient air moisture instead of extra liquid reagents to achieve fragmentation of PET into terephthalic acid (TPA) and acetaldehyde.
“Air contains a significant amount of moisture, making it a readily available and sustainable resource for chemical reactions,”
Naveen Malik stated, the study’s first author.
“On average, even in relatively dry conditions, the atmosphere holds about 10,000 to15,000 cubic kilometers of water. Leveraging air moisture allows us to eliminate bulk solvents, reduce energy input and avoid the use of aggressive chemicals, making the process cleaner and more environmentally friendly.”
By avoiding traditional solvents, the researchers not only reduce energy input but also eliminate the awkward and hard to handle step of separating recycled materials from solvents.
“There is a dire need for better technologies that can process different types of plastic waste. Most of the technologies that we have today melt down plastic bottles and downcycle them into lower-quality products. What’s particularly exciting about our research is that we harnessed moisture from air to break down the plastics, achieving an exceptionally clean and selective process. By recovering the monomers, which are the basic building blocks of PET, we can recycle or even upcycle them into more valuable materials.”
said Northwestern’s Yosi Kratish, the study’s co-corresponding author. This study was carried out by a team of experts in chemical and materials science. Naveen Malik, Jiaqi Li, and Amol Agarwal led by researchers Yosi Kratish and Tobin J. Marks. Kratish went onto say:
Recycling methods usually involve high temperatures, significant energy consumption, and expensive or toxic catalysts, which can lead to the generation of harmful byproducts. Alternatively, this new approach developed by the team at Northwestern is less energy-intensive and produces fewer unwanted byproducts. Importantly, the catalyst in the Northwestern process is both durable and recyclable.
“Our study offers a sustainable and efficient solution to one of the world’s most pressing environmental challenges: plastic waste,”
said Naveen Malik, the study’s first author.
“Unlike traditional recycling methods, which often produce harmful byproducts like waste salts and require significant energy or chemical inputs, our approach uses a solvent-free process that relies on trace moisture from ambient air. This makes it not only environmentally friendly but also highly practical for real-world applications.”
Tests have shown that within 4 hours, up to 94% of the available terephthalic acid (TPA) can be recovered from PET waste. Moreover, the technique works even on mixed plastic waste and coloured plastics, selectively targeting polyesters and therefore bypassing the need for extensive pre-sorting a key economic and process advantage for large-scale recycling operations.
Given that PET plastics make up roughly 12% of global plastic use and contribute massively to the global environmental pollution issue , this innovation offers a promising way for a more sustainable, circular economy. Recovering monomers like TPA from used plastics means that materials could be continuously reused, either by remanufacturing into new PET products or by converting. PET usually ends up in landfills or degrades into microplastics which enter water courses etc. This will mitigate those issues. Kratish said:
“The U.S. is the number one plastic polluter per capita, and we only recycle 5% of those plastics,”
While further work is needed to adapt the process for industrial-scale applications, the research team is optimistic about its future impact. Scaling up this method could offer industries a more cost-effective and environmentally responsible way of handling plastic that otherwise is a massive weight in the global pollution issue.
“Our technology has the potential to significantly reduce plastic pollution, lower the environmental footprint of plastics and contribute to a circular economy where materials are reused rather than discarded,” Malik said. “It’s a tangible step toward a cleaner, greener future, and it demonstrates how innovative chemistry can address global challenges in a way that aligns with nature.”
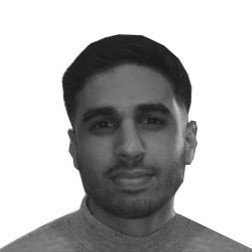
Hassan graduated with a Master’s degree in Chemical Engineering from the University of Chester (UK). He currently works as a design engineering consultant for one of the largest engineering firms in the world along with being an associate member of the Institute of Chemical Engineers (IChemE).