Researchers at the University of Texas at Dallas have introduced a self-repairing 3D-printed foam that is more durable and more recyclable than polymer foams that are currently used in industry. The team’s work was published in the RSC Applied Polymers journal and can be found below:
Johnson, R. M., Tolfree, A. R., Felicio Perruci, G., Ayers, L. C., Arora, N., Liu, E. E., Ganesh, V., Lu, H., & Smaldone, R. A. (2025). 3D printable polymer foams with tunable expansion and mechanical properties enabled by catalyst-free dynamic covalent chemistry. RSC Applied Polymers, 3(2), 428–437. https://doi.org/10.1039/D4LP00374H
UT Dallas researchers have developed a foam that integrates covalent chemistry; a process where reversible chemical bonds allow the material to repair itself after damage. Unlike polymer foams used in industry now, which often undergo irreversible reactions during curing, the new foam formulation takes advantage of these reversible bonds to offer both longevity and greater recyclability. The research addresses a key challenge: combining the versatility of 3D printing with the functional requirements of durable foam materials. Rebecca Johnson, who plans to complete her PhD in chemistry in May explained:
“This is probably the longest project I’ve ever done, From start to finish, it was a little over two years. A lot of it was trying to get the polymer formulation correct to be compatible with the 3D printer.”
The 3D-printing developed by the team offers several advantages. The technique gives researchers the ability to make geometric structures which conventional foaming methods were unable to produce. The material designing capabilities make it possible to produce specialised applications across diverse fields.
- The foam’s recovery from physical impacts creates new possibilities for superior design of protective apparel including helmets as well as automotive bumpers and protective equipment.
- The material stands as a viable choice for developing improved solutions related to thermal and acoustic insulation because it maintains lightweight properties while maintaining resilience.
- Three-dimensional printing technology empowers users to design exact microstructures for the foam that fit individual industrial sectors and consumer purposes.
Dr. Ron Smaldone, associate professor of chemistry and biochemistry at UT Dallas, explained that developing a material that could consistently be printed without defects was a central goal of the project. By using dynamic covalent bonds, the researchers have taken a step toward overcoming the recyclability issues that are inherent in many polymer foams that are in use in industry. Dr. Smaldone explained:
“We’re certainly not the only ones trying to do this, The novelty is using dynamic chemistry to print really great foam material. The next question to address will be, how do we tune the properties and use this new kind of knowledge to fit a variety of different needs?”
The project was led by doctoral students Rebecca M. Johnson and Ariel R. Tolfree, among others. Funding for the research came from institutions such as The Welch Foundation, the National Science Foundation, and the Department of Energy. You can learn more through a video created by the authors here:
Tolfree said creating a foam balloon dog as one of the group’s test objects was a natural choice. Tolfree said:
“It’s a simple shape but perfectly represents our foams, A balloon seems ordinary until it’s twisted into something new, almost defying expectations. Our foams are the same — unassuming at first, but once expanded and transformed, they become something remarkable.”
The creation of self-healing foam represents an advancement in additive manufacturing development. The UT Dallas team’s research brings substantial value to polymer engineering by resolving crucial problems of material longevity and environmental impact.
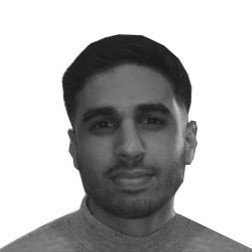
Hassan graduated with a Master’s degree in Chemical Engineering from the University of Chester (UK). He currently works as a design engineering consultant for one of the largest engineering firms in the world along with being an associate member of the Institute of Chemical Engineers (IChemE).