In a groundbreaking collaboration, Dr. Ronald Smaldone and his team have harnessed dynamic phosphodiester bonds to create 3D-printed, self-healing polymer foams that expand and repair without catalysts at low activation temperatures. By combining printed architectures with catalyst-free reversible crosslinks, they achieve isotropic mechanical strength and rapid foaming. This offers a more sustainable alternative to conventional thermoplastic foams. The interview builds upon our previous feature, which you can view here. You can view the paper, which was published in RSC Applied Polymers, here:
Johnson, R. M., Tolfree, A. R., Felicio Perruci, G., Ayers, L. C., Arora, N., Liu, E. E., Ganesh, V., Lu, H., & Smaldone, R. A. (2025). 3D printable polymer foams with tunable expansion and mechanical properties enabled by catalyst-free dynamic covalent chemistry. RSC Applied Polymers, 3(2), 428–437. https://doi.org/10.1039/D4LP00374H
You can view more of the research published by the team here.
The following interview is presented unedited to preserve Rebecca Johnson’s and Ariel Tolfree’s original responses, they are both PhD Candidates at the Smaldone Lab, Department of Chemistry and Biochemistry, The University of Texas at Dallas and offer an unfiltered look at their and their teams microscopy approaches and insights into self-healing polymer architectures.
Follow the main authors here:
What types of dynamic chemical bonds or reversible crosslinks underpin the self-healing properties of this foam, and how were these bonds selected and optimised?
We chose dynamic phosphodiester bonds for the improved expansion and healing of the 3D printed foams. This choice was made because this bond exchange doesn’t require a catalyst and has a low temperature for activation. Also, as a commercially available crosslinker, the cost is lower than synthesizing a custom one for potential commercial applications.
How does the foam’s 3D-printed architecture influence its self-healing efficiency and overall mechanical strength, particularly compared to traditionally moulded thermoplastics?
The 3D printing allows for much more complex architectures in comparison to traditional manufacturing processes for foams and polymers in general. Additionally, we see isotropic mechanical properties and foaming, providing for strong 3D printed foams. This is beneficial because we achieve the foaming post synthesis, which can expand applications compared to molded foams.
Could you discuss the specific conditions (e.g., temperature, pressure, humidity) under which the self-healing process is activated, and whether any external stimuli are required?
The dynamic chemistry occurs in an oven at 165°C, at ambient pressure and humidity. This heat activates both the foaming process and the dynamic chemistry concurrently. This only takes about 15 minutes, making the foaming process a quick technique.
What are the key environmental benefits of using this dynamic chemistry in polymer manufacturing, and how does it improve sustainability over conventional foam materials?
The potential environmental and sustainability benefits are from the ability of the 3D printed materials to be used in multiple forms. Once 3D printed, the materials can be used pre-foaming, with the microspheres responsible for the foaming remaining dormant in the polymer. At any point foaming can be done and the dynamic chemistry can counteract any damage that occurred in the pre-foamed state. This allows for use in multiple applications both in the pre-foamed polymer state and in the foamed state.
How robust is the foam’s performance after multiple self-healing cycles? Does the material retain its original mechanical properties or gradually degrade over repeated use?
We have yet to test multiple cycles of self-healing. With the microspheres used for foaming, optimization would be required to not damage the closed-cell foam pores with successive foaming and healing cycles as heat is required.
What are the most promising applications for this self-healing foam, and are there any ongoing collaborations or pilot projects aiming to commercialise this technology?
These foams have promising properties for sound blocking, energy dissipation and structural applications. We are working alongside mechanical engineering graduate students to further quantify their abilities. Currently, we have no plans to commercialize at this time.
Looking ahead, what further refinements do you plan to explore (for example, improving healing speed, enhancing mechanical strength, or incorporating additional functional properties) to advance the material’s real-world viability?
We are looking toward more bio-based polymer alternatives for the foams, along with testing recyclability for improved sustainability.
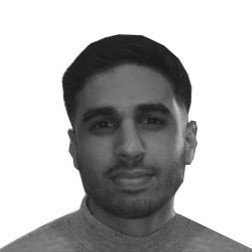
Hassan graduated with a Master’s degree in Chemical Engineering from the University of Chester (UK). He currently works as a design engineering consultant for one of the largest engineering firms in the world along with being an associate member of the Institute of Chemical Engineers (IChemE).