Polyethylene (PE) and polypropylene (PP) together represent about two-thirds of global plastic production, but their similar densities and melting behaviours make them hard to separate in mechanical recycling. When mixed, these polymers form weak, phase-separated blends that lack practical value.
Researchers at Cornell University have introduced a one-step chemical compatibilisation method that uses a common alkyl peroxide. Under heat, the peroxide generates radicals that abstract hydrogen from high-density polyethylene (HDPE) and isotactic polypropylene (iPP), enabling the two chains to graft into a copolymer. This additive can be blended with mixed HDPE/iPP feedstocks during mechanical recycling to restore tensile strength and impact resistance. Their research was published in the Journal of the American Chemical Society, and can be found here:
Kränzlein, M., Cui, S., Hu, J., LaPointe, A. M., Fors, B. P., & Coates, G. W. (2025). One-Step Radical-Induced Synthesis of Graft Copolymers for Effective Compatibilization of Polyethylene and Polypropylene. Journal of the American Chemical Society. https://doi.org/10.1021/jacs.5c03869
This work builds on a multiblock polymer strategy first demonstrated in 2017 by Coates’ lab and collaborators at the University of Minnesota. That earlier approach used a bespoke multiblock polymer to link PE and PP, but complex synthesis and high material costs prevented scale-up. The new peroxide-based route relies entirely on commercially available reagents and standard melt-processing equipment.
The co-lead authors were postdoctoral researcher Moritz Kränzlein and doctoral student Shilin Cui. The project was led by Geoffrey Coates, the Tisch University Professor of Chemistry and Chemical Biology in the College of Arts and Sciences, the paper’s senior author. Geoffrey Coates explained:
“We had to go back to the drawing board and think of the Venn diagram of what material would work and what synthetic methods would be affordable, why didn’t we just do that in 2017? Trust me, if it was easy, somebody else would have done this long ago.”
The team conducted over 200 experiments, maintaining a strict price-per-pound threshold to ensure industrial feasibility rather than pursuing elaborate lab-only solutions.
When heated with HDPE and iPP, the peroxide selectively plucks hydrogen atoms from each polymer backbone, and the resulting macroradicals recombine to form graft copolymers. These behave like a ‘plastic soap,’ reducing interfacial tension and promoting miscibility between the two phases. Kränzlein explained.
“When we have mixtures of commodity plastics like HDPE and iPP, those don’t mix very well, and those phases separate from each other, which makes the material properties of those mixtures pretty bad,” Kränzlein said.
“This process adds in a third component that acts like a soap between those two phases, and that soap facilitates a better miscibility between the polymers, and that restores the physical properties of those mixtures, essentially. To quantify the effects. It took us a very, very long time playing around with all the different tuning points, until we finally achieved something that we were happy with.”
Looking ahead, Geoffrey Coates noted,
“We’ve shown the chemistry at the gram scale; scaling to tens of kilograms will require process optimisation, but we’re confident it’s feasible.”
He has since launched a startup through Cornell’s Praxis Center to commercialise the technology. Coates explained:
“The dream is, if you can make a really rigid polymer that’s also really tough, then you can make packaging that uses less material, yet has the same sort of properties. That’s one of the other big applications for this technology.”
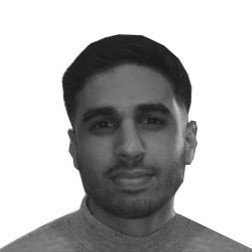
Hassan graduated with a Master’s degree in Chemical Engineering from the University of Chester (UK). He currently works as a design engineering consultant for one of the largest engineering firms in the world along with being an associate member of the Institute of Chemical Engineers (IChemE).