Key Takeaways
– Rotary drum is a versatile and efficient equipment used in various industries.
– It is commonly used for drying, cooling, and mixing applications.
– The design and operation of rotary drums play a crucial role in their performance.
– Regular maintenance and proper handling are essential for maximizing the lifespan of rotary drums.
– Advancements in technology have led to the development of more efficient and eco-friendly rotary drum systems.
Introduction
Rotary drums are an integral part of many industrial processes, offering a versatile and efficient solution for various applications. From drying and cooling to mixing and granulating, rotary drums have become indispensable in industries such as agriculture, chemical, food processing, and mining. In this article, we will explore the world of rotary drums, their design, operation, maintenance, and the advancements that have made them more efficient and eco-friendly.
The Basics of Rotary Drums
Rotary drums, also known as rotary dryers or rotary kilns, are cylindrical vessels that rotate on their axis. They are designed to facilitate the transfer of heat or mass between the drum and the material being processed. The drum is typically inclined slightly to allow the material to move from one end to the other as it rotates.
The Design and Operation of Rotary Drums
The design of a rotary drum is crucial for its performance and efficiency. Factors such as drum diameter, length, inclination, and rotational speed need to be carefully considered to ensure optimal heat and mass transfer. Additionally, the choice of materials for the drum and the internal flights or lifters can impact the overall performance and durability of the equipment.
The Drying Process in Rotary Drums
One of the primary applications of rotary drums is drying. The drying process involves the removal of moisture from a material through evaporation. As the material moves through the drum, it is exposed to hot air or gases, which absorb the moisture and carry it away. The design of the drum and the control of airflow and temperature are critical for achieving efficient drying.
Advancements in Rotary Drum Technology
Over the years, advancements in technology have led to the development of more efficient and eco-friendly rotary drum systems. These advancements include improved insulation to minimize heat loss, enhanced control systems for precise temperature and airflow control, and the use of renewable energy sources for heating. These innovations have not only increased the efficiency of rotary drums but also reduced their environmental impact.
Energy Efficiency in Rotary Drums
Energy efficiency is a key consideration in the design and operation of rotary drums. By optimizing the insulation, airflow, and heat transfer mechanisms, manufacturers have been able to reduce energy consumption and operating costs. Additionally, the integration of renewable energy sources, such as solar or biomass, has further improved the sustainability of rotary drum systems.
Eco-Friendly Features of Rotary Drums
In addition to energy efficiency, rotary drums now incorporate various eco-friendly features. These include the use of low-emission burners, advanced control systems to minimize waste, and the integration of dust collection systems to reduce air pollution. These advancements not only benefit the environment but also help industries comply with stricter regulations and reduce their carbon footprint.
Maintenance and Handling of Rotary Drums
Proper maintenance and handling are essential for maximizing the lifespan and performance of rotary drums. Regular inspections, cleaning, and lubrication of the drum and its components are necessary to prevent wear and ensure smooth operation. Additionally, operators should follow proper handling procedures to avoid damage during loading and unloading of materials.
Troubleshooting Common Issues
Despite regular maintenance, rotary drums may encounter common issues such as uneven drying, material buildup, or excessive noise. These issues can be addressed through proper troubleshooting techniques, which may involve adjusting the drum speed, optimizing airflow, or cleaning the drum internals. It is important to identify and resolve these issues promptly to avoid any adverse effects on the process or equipment.
Conclusion
Rotary drums have revolutionized various industries by providing efficient and versatile solutions for drying, cooling, and mixing applications. The design, operation, and maintenance of rotary drums play a crucial role in their performance and longevity. With advancements in technology, rotary drum systems have become more energy-efficient and eco-friendly, helping industries reduce their environmental impact. By understanding the basics of rotary drums and following proper maintenance practices, industries can maximize the benefits offered by this essential equipment.
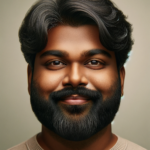
Adrian graduated with a Masters Degree (1st Class Honours) in Chemical Engineering from Chester University along with Harris. His master’s research aimed to develop a standardadised clean water oxygenation transfer procedure to test bubble diffusers that are currently used in the wastewater industry commercial market. He has also undergone placments in both US and China primarely focused within the R&D department and is an associate member of the Institute of Chemical Engineers (IChemE).