Follow Dr. Niusha Shafiabady and her teams works here. A link to the specific paper our earlier news report and this interview pertain to can be found here:
Nguyen, T. Q., Vu, T. B., Shafiabady, N., Nguyen, T. T., & Nguyen, P. T. (2024). Real-time structural health monitoring of bridges using convolutional neural network-based loss factor analysis for enhanced energy dissipation detection. Structures, 70, 107733. https://doi.org/10.1016/j.istruc.2024.107733
In a groundbreaking study, Dr. Niusha Shafiabady and her team have developed an AI-driven system for detecting structural defects in bridges, leveraging convolutional neural networks (CNNs) to enhance real-time monitoring and predictive maintenance. As part of our continued exploration of this topic, which we covered in an earlier news feature, we spoke with Dr. Shafiabady to gain further insight into the technology, its applications, and its potential to revolutionise infrastructure monitoring.
The following interview is presented unedited to preserve Dr. Shafiabady’s original responses, offering an in-depth, unfiltered perspective on her work. This format allows readers to fully understand the technical details and broader implications of AI-driven defect detection in structural engineering.
Acknowledgments from Dr Niusha Shafiabady: This study is conducted in collaboration with researchers from Ho Chi Minh City Open University, Roads Management Center (RMC), Ho Chi Minh City Department of Transportation, Ho Chi Minh City University of Transport in Ho Chi Minh City, Vietnam and the Australian Catholic University in Australia.
Could you explain the specific neural network architecture or AI algorithms utilised in your system for defect detection, and how they are tailored to analyse structural data from bridges?
This system uses a special type of artificial intelligence called a Convolutional Neural Network (CNN) to monitor the health of bridges in real-time. It focuses on how energy moves through a bridge as it vibrates, using a measurement called the loss factor to detect even small changes that could signal problems. A basic overview of how it works is presented below:
Data Collection
Sensors on the bridge measure vibrations, which include how much the bridge is shaking and at what speeds. This information is collected over a period of time.
Vibration Data Analysed
This vibration data is then converted into a format that the CNN can understand. The CNN looks at the different frequencies and amplitudes, and it also looks at how much energy is lost during the vibrations
The Loss Factor is Incorporated
This loss factor is a key measurement. It tells us how much energy is being dissipated as the bridge vibrates. A higher loss factor can indicate that the bridge is experiencing stress, which can be a sign of damage or wear
As mentioned above, the CNN is used to monitor the health of the bridge. It works as follows:
The CNN uses layers of filters that scan the vibration data to find important features. These filters help the system learn to recognise normal and abnormal patterns of vibration. The CNN also uses a process called pooling to simplify the data and focus on the most important information. The last step, the CNN uses connected layers to combine the extracted information and classify it. This is how the system determines if the signals are normal, noise, or indicate a potential defect
The CNN is trained using a large amount of data from real bridges. This helps it learn what normal vibration patterns look like, so it can recognise when something is different. The CNN can analyse vibration data as it comes in, providing almost immediate feedback on the bridge’s condition. This allows for quick intervention if a problem is detected. As the system gathers more data, it learns and improves, making it even more effective at detecting potential problems. This CNN model is specifically designed to analyse complex bridge data. By focusing on the loss factor, the system is less affected by environmental factors and can more accurately detect early signs of structural problems. This method provides a robust, real-time tool for bridge health monitoring.
What types of data inputs (e.g., visual imaging, acoustic signals, vibration patterns) are processed by the AI, and how do these contribute to accurately identifying defects in bridge structures?
The AI system primarily processes vibration data to identify defects in bridge structures. This data is collected by sensors strategically placed on the bridges. The analysis of this vibration data is crucial for detecting structural anomalies, and the system uses several key aspects of the vibration signal as inputs
In summary, the AI system uses vibration data, with the key aspects of the energy spectrum, the loss factor, time-domain characteristics, and the derived parameters of amplitude and frequency to detect structural defects in bridges. This approach enables early detection of minor structural issues and supports effective maintenance planning
How does your AI system handle the variability in bridge materials and designs to ensure consistent defect detection across diverse infrastructures?
The approach we use doesn’t really rely on the bridge materials. This AI system uses a smart approach to keep bridges safe by constantly checking how they vibrate and lose energy. Instead of just looking at how much a bridge shakes or how fast it moves, it focuses on something called the loss factor, which measures how much energy is lost as the bridge vibrates. This helps the system detect even small problems that might be missed by other methods. Of course the amount of energy that is lost depends on the material of the bridge too but we haven’t bound ourselves to the material; we look into loss factor.
Could you discuss the training process for the neural networks? What datasets were used, and how was the system validated for real-world application?
The AI system uses a sophisticated process to learn how to detect problems in bridges, much like how a doctor learns to identify diseases. This process involves training neural networks, which are a type of artificial intelligence, using specific data. The AI system takes in training data and then learns from the given information.
The neural networks are trained using large amounts of vibration data collected from real bridges. This data includes information about how bridges vibrate under different conditions, such as when cars or trucks drive over them. The data includes a wide range of conditions, such as different traffic loads (heavy trucks, light cars, mixed traffic), which helps the AI learn to distinguish between normal bridge behaviour and signs of potential damage. The data is gathered from accelerometers, which are sensors that measure vibrations, placed at various points on the bridge. The vibration data is initially in the time domain, but it’s then transformed into the frequency domain using a process called Fast Fourier Transform (FFT). This allows the AI to analyse the different frequencies present in the vibration signals. The system also uses a parameter called the loss factor (η), which is a measure of how much energy is lost during vibrations. This factor is calculated from the vibration data and serves as a key indicator of structural health
The core of the system is a Convolutional Neural Network (CNN), a type of AI particularly good at recognising patterns in data. The CNN is trained by feeding it the vibration data and telling it whether each piece of data represents normal bridge behaviour, noise, or a potential defect This process is called supervised learning.
During training, the CNN adjusts its internal settings (called weights) to better identify patterns that are associated with defects. This is done by comparing the CNN’s predictions with the actual labels of the data, using a custom loss function, and adjusting the weights through back-propagation. The training data is preprocessed to include key spectral characteristics. The raw signals are transformed into the frequency domain using FFT, and noise filtering techniques are applied. The training also uses data augmentation techniques to make the model more resilient to varying conditions, by increasing the variability of training data.
The system is then Validated. We have used Test data for this process. The test data is the data the system hasn’t seen before. The system’s performance is evaluated using real-world data collected from actual bridge monitoring systems. This ensures that the system works effectively under practical conditions. The CNN model’s ability to differentiate between normal operating signals, noise, and defect-related signals is tested. This is crucial to avoid false alarms and ensure that the system only flags genuine issues.
The results are compared with other machine learning models, such as multilayer perceptrons (MLP) and recurrent neural networks (RNNs), to demonstrate the CNN’s superior accuracy. The performance of the system is measured using metrics such as mean squared error (MSE), root mean squared error (RMSE), and classification accuracy. The CNN model consistently shows lower error rates and higher accuracy, indicating its greater precision and better convergence in processing vibration signals.
The system is also tested under various traffic conditions, including heavy and light traffic periods, to make sure it is accurate in different scenarios.
What advantages does your AI-based approach offer over traditional methods of bridge inspection in terms of accuracy, efficiency, and cost-effectiveness?
The AI-based system for bridge monitoring offers several key advantages over traditional inspection methods, particularly in terms of accuracy, efficiency, and cost-effectiveness.
The AI-based approach provides a more accurate, efficient, and cost-effective alternative to traditional bridge inspection methods. By focusing on the loss factor and leveraging the power of CNNs for data analysis, this system enables early detection of defects, targeted maintenance, and continuous monitoring, all of which contribute to enhanced safety and the long-term sustainability of bridge infrastructure.
Unlike traditional methods that often rely on visual inspections or measurements of displacement, this AI system focuses on the loss factor, which measures how much energy is lost as a bridge vibrates
This parameter is highly sensitive to even small structural changes, allowing the detection of problems that might be missed by traditional methods
The AI system can detect minor defects and changes in structural behaviour at an early stage. Traditional methods might only identify issues when they become more pronounced and visible, by which time the damage may be significant
By using a Convolutional Neural Network (CNN), the system can distinguish between normal vibrations, noise, and defect-related signals. This reduces the likelihood of false alarms that can occur with traditional methods which may be sensitive to environmental factors
The CNN can process and analyse complex vibration patterns, identifying subtle anomalies that would be very difficult for a human to detect. Traditional methods often rely on human interpretation of data or visual inspection, which can be subjective or prone to error.
The AI system provides continuous, real-time monitoring, allowing for immediate detection of structural changes. This is in contrast to traditional inspections, which are usually periodic and might miss transient or developing issues.
Are there any limitations or challenges in deploying this technology at scale, such as environmental factors, hardware requirements, or integration with existing maintenance workflows?
While the AI-based bridge monitoring system offers many advantages, there are some limitations and challenges to consider when deploying this technology at scale. These challenges can be broadly categorised into environmental factors, hardware requirements, and integration with existing maintenance workflows.
Continuous monitoring requires a reliable power supply for sensors and data transmission equipment, which may be a challenge for remote or isolated bridge structures.
The sensors and hardware must be durable and resistant to harsh weather conditions, and they may require periodic maintenance or replacement, which can add to the overall cost.
Integrating this new system with existing bridge management systems may require additional software development to ensure compatibility. This integration is crucial for seamless data exchange and effective maintenance planning.
The initial costs associated with installing sensors, data processing equipment, and software development may be a barrier to adoption, especially for smaller or cash-strapped infrastructure management agencies.
Looking forward, what advancements or refinements do you envision for this technology? Are there plans for collaborations or field trials to further validate and optimise its performance?
The same principles can be applied to different bridges globally. We can use similar decision-making processes for monitoring the health of any bridge. We are working to come up with ways to even further enhance the accuracy of our predictive AI systems.
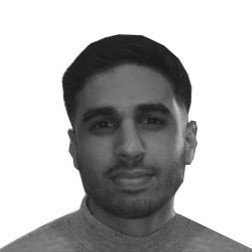
Hassan graduated with a Master’s degree in Chemical Engineering from the University of Chester (UK). He currently works as a design engineering consultant for one of the largest engineering firms in the world along with being an associate member of the Institute of Chemical Engineers (IChemE).