What Is The Shop Process?
SHOP stands for shell higher olefin process and is a chemical process that produces Linear alpha olefins (LAO) from the raw material of ethylene. The SHOP process and mechanism was discovered in 1969 by shell chemists notably Wilhelm Keim in Emeryville California. The SHOP process came at a very important time and its success is due to several factors; the first factor was the cost of producing LAO was high and was only done by using a combination of wax and the Ziegler polymerization, the SHOP overcame the high costs as it processes to produce LAO’s was economically and environmentally better than the wax-splitting and Ziegler methods. Another factor is the demand for ethylene which is produced by the petrochemical industry being far smaller than the supply, thus with the abundance and low cost of ethylene it was the ideal hydrocarbon to use for the SHOP process. Another reason is that in the late 1960’s due to the negative ecological effects of detergents that caused foaming of surface water, theses detergents where being produced from branched fatty alcohols, thus the negative impact of the detergents put pressure on companies such as Shell to innovate and produce a detergent that didn’t cause ecological harm. The SHOP processes solved the ecological issue due to the branched fatty alcohols used in detergents by replacing them with linear fatty alcohols, which worked at lower temperatures and had better washing performances than the detergents that contained branched fatty alcohols (Keim, 2013).
The SHOP process was commercialized by Dutch Shell In 1977 and is used internationally with production exceeding 1 million tonnes annually. LAO are olefins which are alkenes with the general formula CnH2n and are distinguished from other alkenes/olefins due to the carbon double bond being located at the alpha position such as 1-butene and 1-hexene (figure 1).
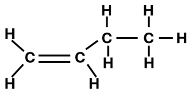
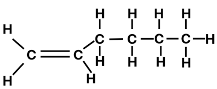
Figure 1: 1-Butene (left) and 1-Hexene (right) examples of linear alpha-olefins.
Linear Alpha-Olefin Market
The market for LAO is constantly expanding with the highest uses in North America (40%), middle east (19%), Western Europe (16%) and China (10%) (figure 2). From 2012 – 2016 the global consumption of LAO increased by 5.4%, this is due to the increased demand for products that are manufactured using LAO such as; oilfield chemicals, detergents, surfactants and polyethylene comonomers. The projection for the LAO market for the future is an increase of around 3.6% during 2016-2021 with an estimated market value of 15.85 billion by 2023 (PRNewswire, 2018).
One of the main reasons for the projected increase is a new 200,000-tonne production plant being constructed in Qatar, this will increase the current annual global production by approximately 20% (Keim, 2013). Other factors for the projected increase of the alpha-olefins market is due to the continued high demand for alpha-olefins due to the low price of ethylene, the high demand for polyolefin comonomers, the high demand for speciality chemicals and the need for LAO in the oil industry and shale-based natural gases which are the driving force as both of these industries are projected to continue growing and will thus increase the demand for LAO (IHS Markit, 2017).
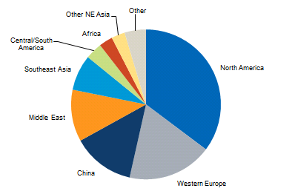
Figure 2: A Breakdown of SHOP market (IHS Markit, 2017).
Linear Alpha-Olefin Production Methods
LAO’s are produced in two main methods; the first method which is the most popular is the Oligomerization of Ethylene and the second method is the Fischer-Tropsch synthesis. The Oligomerization of Ethylene is the most used process for the production of ethylene as the undesired products that are produced at the end of the process can be recycled till extinction thus this makes the process have very small waste and increases the amount of product produced thus making the process very profitable. Fischer-Tropsch synthesis is used less for the production of LAO’s as Fischer-Tropsch as it produces a range of substance such as; alkanes, alkenes and alcohols. Also, the LAO’s produced must be separated and purified, this will cause the cost of the process to be high as more equipment is needed for the separation and purification. Furthermore, due to the importance of the position of the carbon double bond for LAO production companies will choose SHOP due to SHOP only producing LAO’s.
LAO’s that are produced from the SHOP process has a range of uses; the shorter chain LAO such as C4 – C8 are predominantly used in the production of polyethylene, LAO of chains of C10 – C14 are used in making surfactants for detergents. LAO with chains C16 – C18 is primarily used as a lubricating fluid and LAO with chain C20 and greater which are the least used types of LAO and are used in linear alkylbenzenes, which are used in household detergents as a surfactant (Students, 2015).
The SHOP process (figure 3) converts ethylene into LAO’s by using a variety of catalysts and the three main steps of the SHOP process; oligomerization of ethylene, isomerization and metathesis. The oligomerisation of ethylene this produces alpha-olefins C4-C8, C10-C14 and C16-C40, the desired alpha-olefins can be separated and sold or they C10-C14 alpha-olefins can be turned into alcohols by undergoing linear hydroformylation and then undesired alpha-olefins are sent to the next stage of the process. The second step is the isomerisation of carbon chains C4-C8 and carbon chains of C16-C40 and greater and converts them into internal olefins. The third step and last step is the metathesis which produces new internal olefins with the desired internal olefins C10-C14 being separated by distillation and then undergo hydroformylation and are converted into linear alpha olefins and then into alcohols and the undesired are sent back to isomerization’s part of the process and are recycled to extinction to produce the desired products (ETH Zurich, 2018).
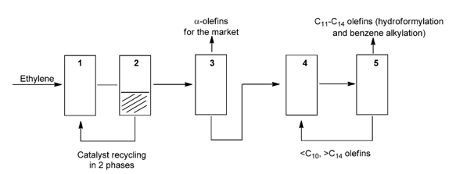
Figure 3: SHOP process diagram schematic (Keim, 2013).
Oligomerization
The oligomerization of ethylene (C2H4) is carried using a homogenous nickel catalyst with a polar solvent at the process conditions of 90-100 ℃ and 40 bar with excess ethylene (Equation 1) (ETH Zurich, 2018). The polar solvent used is 1,4-butanediol, the 1,4-butanediol doesn’t act as a solvent for the products but the reactants and the catalyst, this makes recycling the catalyst easier as the 1,4-butanediol can be separated easily.

Equation 1: oligomerization of ethylene (C2H4) using a homogenous nickel catalyst.
The mechanism for oligomerization of ethylene (figure 4) starts with the catalyst precursor being converted into a nickel hydride complex which is the active catalyst intermediate, this is done by using a catalyst precursor which can include oxygen-phosphorus chelate (figure 5). The catalyst precursor has a chelate part and an organic part, the chelate part controls the length of the chain that is produced, and the organic part stabilizes the complex (figure 5) (Rothenberg, 2015). Ethylene is then inserted into the nickel hydride complex; the length of the carbon chain increases due to the insertion of ethylene and then β – hydride elimination occurs which transferrers the hydride atom from the ligand at the beta-position to the metal centre (Interactive Learning Paradigms Incorporated, 2015) thus terminating the chain and produces oligomers of different chain length, polyethylene, wax and regenerates the nickel hydride complex (Rothenberg, 2015).
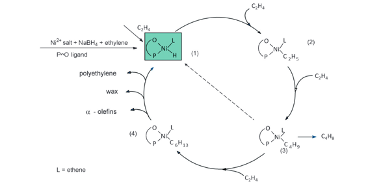
Figure 4: The mechanism for Oligomerisation of ethylene (Keim, 2013)
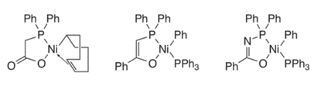
Figure 5: examples of catalyst precursors (Hartwig, 2010)
The process of oligomerization of ethylene involves using the nickel catalyst to oligomerize ethylene to produce a broad range of alpha-olefins, the alpha-olefins that are produced are even-numbered and exhibit Flory-Schulz distribution. The alpha-olefins that are produced from the oligomerization of ethylene are then sent separated using distillation, with the alpha-olefins that are desired C4-C10 and C12-C18 being separated and the undesired products being recycled or sent to the next stage of the process which is isomerisation. The Flory-Schulz distribution indicates that oligomerization process favours polymers that are short-chain rather than a long chain, this is extremely useful the alpha-olefins that are produced majority short chain, with 41% being C4-C8 alpha-olefins, 40.5% C10-C18 alpha-olefins and the remaining 18.5% being C20 or greater alpha -olefins (Wittcoff, 2013). Producing these shorter chains alpha-olefins is economically advantageous as the shorter chain alpha-olefins with carbon chains C4-C8 and C10-C18 have direct commercial value and are separated and sold. Furthermore, C10-C14 LAO can undergo hydroformylation, which turns the C10-C14 alpha-olefins into C11-C15 alcohols with an aldehyde intermediate using an octacarbonyl catalyst with ligands such as tributylphosphine (equation 2) (Wittcoff, 2013).
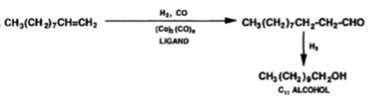
Equation 2: linear hydroformylation of C10 alpha-olefins into C11 alcohol (Wittcoff, 2013)
Isomerization
The next step of the process is isomerisation, this carried out at the process conditions 80 -140 ℃ and 4-20 bar and uses heterogeneous catalysts such as; solid potassium, alkaline alumina or magnesium oxide granules (Hartwig, 2010) and involves the isomerisation of light alpha-olefins (C4-C10) and heavy alpha-olefins (C20+) into internal olefins. Internal olefins have the carbon double bond within the chain and not on the outer carbons. Undertaking isomerisation will cause the alpha-olefins to have the position of the double bonds change position and will result in several internal isomers forming which can be either cis or trans-isomers. This is witnessed in the isomerisation of 1-octene to form a mixture of mainly internal olefins such as 2-octene, 3-octene and 4-octene and a tiny amount of the original alpha-olefin is also found (equation 3) (King Fahd University of Petroleum & Minerals, 2018). After the isomerisation of an alpha-olefin into an internal olefin, the internal olefins are sent to a mixer where they are mixed and are sent to the next stage of the SHOP process where they internal olefins are subjugated to olefin metathesis.
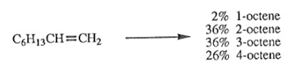
Equation 3: Isomerisation of 1-octene (King Fahd University of Petroleum & Minerals, 2018)
Metathesis
Olefin metathesis causes new carbon double bonds to form, the mixture of short and long-chain internal olefins is passed over an alumina-supported molybdate catalyst that operates at 100-125 ℃ and 10 bar (Mol, 2004), the long and short-chain internal olefins in the mixture then react with one another and produce a statistical distribution of a mixture of linear internal olefins of that include carbon chains which are odd and even (equation 4) (Wittcoff, 2013).

Equation 4: Olefin metathesis of C4 and C20 internal olefins into C12 internal olefins (Wittcoff, 2013).
The species in the catalyst that acts as the active centres for olefin metathesis is the Mo4+ or the Mo5+ (Molybdenum ions). For the formation of the active species the formation of an -allyl complex is important and is the initiation step, and the formation of the active species is by prepared by in situ reductions of the catalyst by the olefin feed (DWYER, 2006). The process of olefin metathesis produces 10-15% of the desired linear internal olefin which has a carbon chain of C10-C14, the desired products are separated from the remaining 85-90% of the undesired products by distillation. The undesired products are then recycled and undergo isomerization and olefin metathesis until extinction. Using this recycling stream more than 96% of the products are C10-C14 linear internal olefin. The desired products form the metathesis stage (C10-C14 linear internal olefin) can undergo two different processes; the first process is linear hydroformylation, this causes linear internal olefins to be converted into linear aldehydes using a catalyst and in the presence of hydrogen. The catalyst is an octacarbonyl catalyst with ligands such as tributylphosphine (Wittcoff, 2013). The catalyst causes the reduction of the aldehyde as it causes the migration of the position of the carbon-carbon double bond to the primary position and then converts the intermediate aldehyde to be converted into C11-C14 alcohols which are used in plasticizers and precursors to detergents, an example of this is converting C12 internal olefins to C14 alcohol (equation 5) (Wittcoff, 2013). The second process involves alkylating the linear internal olefins to creates linear alkylbenzenes, which are used in household detergents as a surfactant (DWYER, 2006).
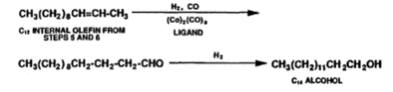
Equation 5: Linear hydroformylation of C12 internal olefin to C14 alcohol (Wittcoff, 2013).
References
DWYER, C. L. (2006). Metathesis of Olefins. In G. P. Chiusoli, Metal-Catalysis in Industrial Organic Processes (pp. 208-209). Sheffield: RSC publishing.
ETH Zurich. (2018). The Shell Higher Olefins Process (SHOP). Retrieved from ETH Zurich: https://www.ethz.ch/content/dam/ethz/special-interest/chab/icb/van-bokhoven-group-dam/coursework/Catalysis/2018/HomCat4_olefins_Part3_SHOP.pdf
Hartwig, J. F. (2010). Organotransition Metal Chemistry – From Bonding to Catalysis. California: University Science Books.
IHS Markit. (2017, March). Linear Alpha-Olefins. Retrieved from IHS Markit: https://ihsmarkit.com/products/linear-alpha-olefins-chemical-economics-handbook.html
Interactive Learning Paradigms Incorporated. (2015, March 31). Beta-Hydride Elimination. Retrieved from Interactive Learning Paradigms Incorporated: http://www.ilpi.com/organomet/betahydride.html
Keim, W. (2013, October 15). Oligomerization of Ethylene toa-Olefins: Discovery and development of the Shell Higher Olefin Process(SHOP). Retrieved from Wiley Online Library: https://onlinelibrary.wiley.com/doi/pdf/10.1002/anie.201305308
King Fahd University of Petroleum & Minerals. (2018). ISOMERIZATION OF OLEFINS. Retrieved from King Fahd University of Petroleum & Minerals: http://faculty.kfupm.edu.sa/chem/belali/CHEM%20620/Chapter%202/CHAPTER%202_ISOMERIZATION%20OF%20OLEFINS.pdf
Mol, J. C. (2004). Industrial applications of olefin metathesis. Journal of Molecular Catalysis A: Chemical, 39-45.
PRNewswire. (2018, July 31). Global $15.85 Billion Alpha Olefins Market by Type, Application and Geography – Forecast to 2023. Retrieved from PR Newswire: https://www.prnewswire.com/news-releases/global-15-85-billion-alpha-olefins-market-by-type-application-and-geography—forecast-to-2023–300689141.html
Rothenberg, G. (2015). Catalysis: Concepts and Green Applications. Amsterdam: Wiley.
Students, I. C.-F. (2015). Industrial Chemistry – For Advanced Students. Detroit: De Gruyter.
Wittcoff, H. (2013). Industrial Organic Chemicals (3rd Edition). New Jersey: Wiley.
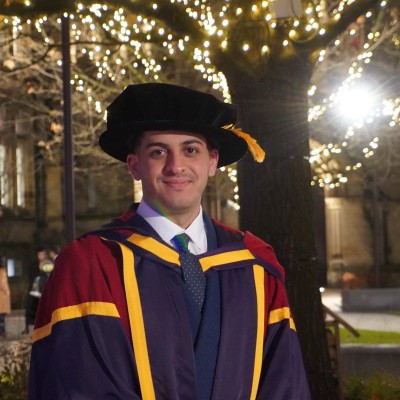
Dr. Adam Zaidi, PhD, is a researcher at The University of Manchester (UK). His doctoral research focuses on reducing carbon dioxide emissions in hydrogen production processes. Adam’s expertise includes process scale-up and material development.’