A team of researchers at The University of Texas at Dallas has introduced a new fabrication method for artificial muscles that could lower production costs and increase application possibilities. The breakthrough, detailed in Science, replaces the mandrel-wrapping process that is used traditionally in industry with a mandrel-free technique that forms coiled polymer fibres with high spring indexes. The research paper can be found here:
Zhang, M., Fang, S., Cai, W., Huynh, C., Göktepe, F., Oh, J., Wang, Z., Ekanayake, I., Göktepe, Ö., & Baughman, R. H. (2025). Mandrel-free fabrication of giant spring-index and stroke muscles for diverse applications. Science, 387(6738), 1101–1108. https://doi.org/10.1126/science.adr6708
Creating high-spring-index artificial muscles requires wrapping polymer fibres or carbon nanotube yarns around a mandrel—a process that not only drove up costs but also produced waste when the mandrel was later removed.
The new technique, developed under the leadership of Dr. Mengmeng Zhang, sidesteps this issue by inserting a controlled twist into individual fibers. By plying the twisted fibers together, the method allows each fibre to serve as a mandrel for its neighbours, forming the coiled structure without any additional components. This approach not only cuts costs but also provides a way to vary the spring index along the muscle’s length, enhancing performance versatility.
“The problem has been that there are no process reports for making mandrel-free, large-spring-index yarns other than to dissolve the mandrel after muscle coiling, which wastes the large-diameter polymer fiber that is typically used as a mandrel and creates a waste stream,”
said Baughman, a Robert A. Welch Distinguished Chair in Chemistry in the School of Natural Sciences and Mathematics.
The fabricated artificial muscles exhibit the ability to stretch up to 97% of their original length while achieving a spring index exceeding 50. This parameter, which measures the ratio of the coil’s mean diameter to the fibre diameter, determines a spring’s flexibility and stiffness. A higher spring index, means that the artificial muscles are more adaptable.
“High-spring-index yarns can be made much less expensively by this mandrel-free method. When heated and cooled, these muscles can significantly contract and elongate due to their large spring index.”
Said Dr. Mengmeng Zhang, research scientist in the Alan G. MacDiarmid NanoTech Institute.
Among the uses that have been thought could be associated with this discovery is the integration of these muscles into adaptive clothing. One promising application is in comfort-adjusting jackets that automatically create larger, thermally insulating pores as the ambient temperature drops. Previous iterations of such jackets, which relied on the more expensive mandrel-wrapped process, were showcased during the 2022 Winter Olympics. However, commercialisation was hampered by production costs. The new mandrel-free method may offer a cost-effective route to reintroducing this technology. As stated by Baughman:
“Our new mandrel-free method for making high-spring-index coiled fiber avoids this major problem, so it may soon enable the commercialization of new comfort-adjusting jackets,”
Beyond wearable technology, the artificial muscles could serve as self-powered strain sensors or be employed in mechanical energy harvesters. By harnessing thermal energy; whether from applied electricity, solvent interactions, or electrochemical means, these muscles achieve precise and repeatable expansion and contraction strokes.
Dr. Ray Baughman, director of the Alan G. MacDiarmid NanoTech Institute and a leading figure in the field, has been a proponent of coiled artificial muscle technology for years. Previous manufacturing processes with mandrel wrapping developed by Dr. Baughman provided foundational knowledge for modern advancements. This mandrel-free manufacturing approach brings manufacturing into a new evolution which establishes connexions between laboratory research and practical commercial applications.
We would like to acknowledge the collaborative effort of the researchers whose contributions have been instrumental to the project: Mengmeng Zhang, Shaoli Fang, Wenting Cai, Chi Huynh, Fatma Göktepe, Jiyoung Oh, Zhong Wang, Ishara Ekanayake, Özer Göktepe, and Ray H. Baughman.
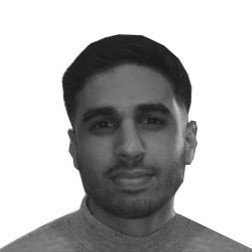
Hassan graduated with a Master’s degree in Chemical Engineering from the University of Chester (UK). He currently works as a design engineering consultant for one of the largest engineering firms in the world along with being an associate member of the Institute of Chemical Engineers (IChemE).