Semiconductor manufacturing relies on ultrapure water in every cleaning and etching step, generating large volumes of wastewater loaded with specialty chemicals that can sometimes be hard to remove. A Research team at the University of Technology Sydney (UTS) and water-tech start-up Infinite Water International (IWI) in Australia have introduced a plug-and-play catalytic oxidation module that targets the two most persistent contaminants; hydrogen peroxide and triazole, breaking them down rather than simply filtering them out.
Global chipmakers draw on vast water supplies. For instance, TSMC’s three Taiwanese parks consume some 3 billion metric tons of water daily; roughly three times Sydney’s municipal supply, underscoring the need for on-site recycling above 90 percent to avoid local shortages. More than a hundred specialty chemicals are used across semiconductor processes; hydrogen peroxide (for surface cleaning) and triazole (for corrosion inhibition) rank among the most toxic and recalcitrant. Professor Long Nghiem, Director of the UTS Center for Technology in Water and Wastewater said:
“With the booming demand for microchips to power artificial intelligence, and huge volumes of water being used to manufacture them, companies need to recycle at least 90% of their water to not deplete local supplies. More than 100 specialty chemicals are used in microchip manufacturing. We need to remove the worst of these chemicals to get clean water at the end of the process, The two most problematic of these chemicals are hydrogen peroxide, used in surface cleaning, and triazole, for corrosion prevention. Both are very toxic and don’t break down easily.”
In bench tests, the unit degraded high-concentration peroxide to benign byproducts in under five minutes and achieved up to 90 percent destruction of triazole within an hour. Both processes rely on an advanced oxidation catalyst loaded into a flow-through cartridge, minimising footprint and energy demand compared to conventional treatment tanks.
The water tech start-up Infinite Water International (IWI) Australia’s, Professor Nghiem and his team, including fellow researcher Associate Professor Cuong Ton-That were instrumental in this technology’s production and conception. Professor Nghiem stated:
“We use a catalytic process. We don’t filter out the contaminants but instead have an oxidation agent that breaks them down in a very targeted way, we pack this agent into a plug-and-play unit that fits into wastewater infrastructure and flushes contaminated water to clean it. We degrade the pollutants to the point where the water becomes safe for any subsequent processes for recycling or eventual disposal.”
Two of the world’s largest logic-chip manufacturers have already agreed to pilot this system in their fab wastewater loops. Water and recycling capital accounts for over 10 percent of a fab’s capital expenditure, so even small efficiency gains can lead to savings of hundreds of millions of dollars across global operations.
While peroxide and triazole pose acute toxicity risks, the industry also contends with per- and polyfluoroalkyl substances (PFAS), so-called “forever chemicals” linked to health issues. Startups such as Oxyle AG use microbubble-driven catalysts to mineralise PFAS molecules, and Gradiant Corp. has deployed PFAS-destruction units in partnership with semiconductor firms, demonstrating the sector’s move toward on-site chemical neutralisation.
The development of this catalytic treatment was led by Professor Long Nghiem, Director of the UTS Centre for Technology in Water and Wastewater, with critical experimental and process‐optimisation work carried out by Associate Professor Cuong Ton-That. They partnered closely with Matthew Ng, Founder and CEO of Infinite Water International (IWI) Australia, whose engineering team helped integrate the oxidation catalyst into a modular, plug-and-play unit.
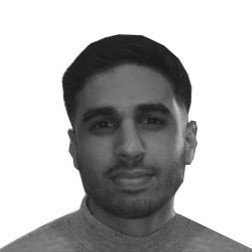
Hassan graduated with a Master’s degree in Chemical Engineering from the University of Chester (UK). He currently works as a design engineering consultant for one of the largest engineering firms in the world along with being an associate member of the Institute of Chemical Engineers (IChemE).