Key Takeaways
– Vibrating feeder design plays a crucial role in various industries.
– Understanding the principles of vibrating feeder design is essential for optimal performance.
– Factors such as material properties, feeder capacity, and operational requirements influence the design process.
– Proper maintenance and troubleshooting are necessary to ensure the longevity and efficiency of vibrating feeders.
– Advances in technology have led to the development of innovative vibrating feeder designs.
Introduction
Vibrating feeders are widely used in industries such as mining, construction, and manufacturing to transport and feed bulk materials. The design of vibrating feeders is crucial for ensuring efficient and reliable operation. This article explores the key aspects of vibrating feeder design, including principles, factors influencing design, maintenance, troubleshooting, and technological advancements.
Principles of Vibrating Feeder Design
Vibrating feeders operate based on the principle of electromagnetic vibration. An electromagnetic drive unit generates vibrations that transfer energy to the material being fed. The design of the feeder must consider factors such as the amplitude, frequency, and direction of vibrations to ensure proper material flow and prevent clogging or spillage.
Material Properties and Feeder Capacity
The design of a vibrating feeder must take into account the properties of the material being handled. Factors such as particle size, density, moisture content, and flowability influence the feeder’s capacity and design parameters. Understanding these material properties is crucial for selecting the appropriate feeder type and size to achieve optimal performance.
Operational Requirements
The operational requirements of a vibrating feeder, such as the desired feed rate, must be considered during the design process. The feeder’s design should ensure a consistent and controlled flow of material to downstream processes. Factors such as the angle of inclination, feeder length, and tray design play a significant role in meeting the operational requirements and achieving efficient material handling.
Maintenance and Troubleshooting
Proper maintenance is essential for the longevity and efficiency of vibrating feeders. Regular inspection, cleaning, and lubrication of components help prevent wear and ensure smooth operation. Additionally, troubleshooting techniques such as checking for loose connections, adjusting drive settings, and inspecting for damaged parts can help identify and resolve issues that may affect the feeder’s performance.
Common Issues and Solutions
Some common issues that may arise with vibrating feeders include material spillage, excessive noise, and erratic feeding. These issues can be addressed through various solutions, such as adjusting the feeder’s amplitude and frequency, modifying the tray design, or installing additional components like chutes or baffles. Understanding the root causes of these issues and implementing appropriate solutions is crucial for maintaining optimal feeder performance.
Technological Advancements in Vibrating Feeder Design
Advances in technology have led to the development of innovative vibrating feeder designs. For example, the integration of sensors and automation systems allows for real-time monitoring and control of feeder parameters, optimizing performance and reducing downtime. Additionally, the use of advanced materials and manufacturing techniques has improved the durability and reliability of vibrating feeders, extending their lifespan and reducing maintenance requirements.
Future Trends
The future of vibrating feeder design is likely to be influenced by advancements in digitalization, artificial intelligence, and robotics. These technologies have the potential to further enhance the efficiency and capabilities of vibrating feeders, enabling more precise control, predictive maintenance, and seamless integration with other automated systems.
Conclusion
Vibrating feeder design is a critical aspect of material handling in various industries. Understanding the principles, factors influencing design, and maintenance requirements is essential for achieving optimal performance and efficiency. Technological advancements continue to drive innovation in vibrating feeder design, offering opportunities for improved control, reliability, and integration with advanced automation systems. By staying informed about the latest developments and best practices, industries can harness the full potential of vibrating feeders for their material handling needs.
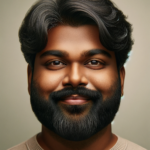
Adrian graduated with a Masters Degree (1st Class Honours) in Chemical Engineering from Chester University along with Harris. His master’s research aimed to develop a standardadised clean water oxygenation transfer procedure to test bubble diffusers that are currently used in the wastewater industry commercial market. He has also undergone placments in both US and China primarely focused within the R&D department and is an associate member of the Institute of Chemical Engineers (IChemE).