Researchers at the University of Houston have created ‘Bendable’ ceramic origami material. In a fusion of time-tested folding techniques and advanced additive manufacturing, Maksud Rahman, assistant professor of mechanical and aerospace engineering and his team have devised a new class of ceramic structures that flex under load rather than shatter. By adopting origami-inspired geometries and a soft polymer shell, the team has turned brittle ceramics into damage-tolerant components that recover their shape after compression. Their research was published in Advanced Composites and Hybrid Materials and can be found here:
Thakur, M. S. H., Nath, M. D., Ajayan, P. M., Paulino, G. H., & Rahman, M. M. (2025). Macroscale ceramic origami structures with hyper-elastic coating. Advanced Composites and Hybrid Materials, 8(2), 226. https://doi.org/10.1007/s42114-025-01284-3
Ceramics, widely used due to their low weight and biocompatibility, normally fail catastrophically when stressed.
“Ceramics are incredibly useful—biocompatible, lightweight and durable in the right conditions—but they fail catastrophically, our goal was to engineer that failure into something more graceful and safer.”
explains Rahman. Working alongside postdoctoral fellow Md Shajedul Hoque Thakur, the group tackled ceramic fragility by combining folding patterns from the Miura-ori origami method with a stretchable polymer coating.
To fabricate the prototypes, the researchers 3D-printed latticed ceramic panels following the Miura-ori crease map; a folding scheme that allows a flat sheet to collapse and expand uniformly, and then applied a thin layer of hyper-elastic, biocompatible polymer. Under multi-axis loading, the coated samples bent and rebounded cleanly, while identical uncoated parts exhibited cracks or complete failure.
Mechanical tests under both static and cyclic compression, supported by finite-element simulations, showed the hybrid structures maintained integrity through repeated deformation. The polymer layer absorbs and redistributes stress at fold lines, markedly increasing toughness in orientations where plain ceramics are weakest. Md Shajedul Hoque Thakur said:
“The origami geometry gave us mechanical adaptability, and the polymer coating introduced just enough flexibility to prevent sudden breakage.”
This new approach has many potential uses in area that require lightweight, impact-resistant materials. Areas such as medical prosthetics, soft robotics and aerospace assemblies, where components must flex without sacrificing strength are some target markets this research could impact. The adaptable ceramic folds could serve as joints in prosthetic limbs or as energy-dissipating skins on unmanned aerial vehicles.
Led by assistant professor Maksud Rahman and postdoctoral fellow Md Shajedul Hoque Thakur (Rice University), the project used expertise from a number of institutions with collaborators Pulickel M. Ajayan (Rice University), Methu Dev Nath (Carnegie Mellon University) and Glaucio H. Paulino (Princeton Materials Institute). The research was funded by Lockheed Martin and utilised equipment supported by Rice University’s Shared Equipment Authority. The 3D printing was done with Formlabs Form 2, and other materials and equipment included Dow Chemical’s PDMS and Formlabs Ceramic Resin.
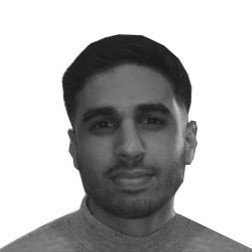
Hassan graduated with a Master’s degree in Chemical Engineering from the University of Chester (UK). He currently works as a design engineering consultant for one of the largest engineering firms in the world along with being an associate member of the Institute of Chemical Engineers (IChemE).