As countries push toward commercial fusion, understanding how materials behave under reactor conditions is critical. Engineers at the University of Surrey have used a combined plasma-focused ion beam and digital image correlation (PFIB-DIC) method to reveal stress patterns in welded P91 steel, an important factor when considering safe plant design and material considerations.
Working with UKAEA, the National Physical Laboratory and TESCAN, the team applied PFIB-DIC to ultra-narrow weld zones to produce high-resolution maps of residual stress in laser-welded P91 joints. By sequentially milling and imaging, they tracked strain relaxation at the micrometre scale, linking stress concentrations to local microstructural features. The research published in Journal of Materials Research and Technology can be found here:
Zhu, B., Mohamed, O., Koko, A., Zhang, H., Dluhoš, J., Wang, Y., Gorley, M., Whiting, M. J., & Sui, T. (2025). Assessing residual stress and high-temperature mechanical performance of laser-welded P91 steel for fusion power plant components. Journal of Materials Research and Technology, 35, 6341–6347. https://doi.org/10.1016/j.jmrt.2025.02.260
Tests at 550 °C, typical temperatures within a fusion environment, showed that tensile residual stress zones became more brittle, with over 30 % strength loss compared to stress-free regions. Conversely, compressive stress pockets exhibited slight hardening, showing how internal stresses can both weaken and reinforce different weld areas.
This work builds on a 2022 Science Advances study, which first demonstrated PFIB-DIC on Eurofer97 steel to map multiscale residual stresses in fusion-relevant materials. The current research extends that approach to P91, tackling the higher temperatures and alloy differences encountered in power-plant components.
Beyond microscopy, the PFIB-DIC datasets have fed machine-learning models that predict residual stress distributions and component lifetimes, offering a faster route to assess weld integrity under service conditions Open Research Surrey. Such predictive tools could reduce the need for lengthy experiments as designs evolve. Dr. Tan Sui, Associate Professor (Reader) in Materials Engineering at the University of Surrey who is leading the research, said:
“Fusion energy has huge potential as a source of clean, reliable energy that could help us to reduce carbon emissions, improve energy security and lower energy costs in the face of rising bills. However, we first need to make sure fusion reactors are safe and built to last. Previous studies have looked at material performance at lower temperatures, but we’ve found a way to test how welded joints behave under real fusion reactor conditions, particularly high heat. The findings are more representative of harsh fusion environments, making them more useful for future reactor design and safety assessments.”
Dr Bin Zhu, research fellow at the University of Surrey’s Center for Engineering Materials and a main author of the study, added,
“Our work offers a blueprint for assessing the structural integrity of welded joints in fusion reactors and across a wide range of extreme environments. The methodology we developed transforms how we evaluate residual stress and can be applied to many types of metallic joints. It’s a major step forward in designing safer, more resilient components for the nuclear sector.”
Jiří Dluhoš of TESCAN, highlighting the industrial relevance of the approach
“We are proud that our FIB-SEM instruments can be part of such a crucial topic in materials research for the energy industry. Our long-standing collaboration with the University of Surrey to automate microscopic residual stress measurements proves that the plasma FIB-SEM can be successfully used for high-precision machining at the microscale.”
With the future commercialisation of fusion power around the corner, the research will play an important role in advancing the technologies needed toward delivering secure, low-carbon electricity at scale.
The work was carried out by Dr Tan Sui (Associate Professor in Materials Engineering) and Dr Bin Zhu (Research Fellow, Centre for Engineering Materials) at the University of Surrey, in close collaboration with engineers and scientists from the UK Atomic Energy Authority and the National Physical Laboratory. Instrumentation and PFIB-SEM expertise were provided by TESCAN’s team under FIB-SEM Product Manager Jiří Dluhoš. Together, this multidisciplinary group designed, executed and analysed the PFIB-DIC experiments and high-temperature mechanical tests.
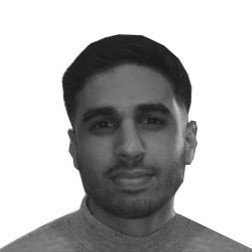
Hassan graduated with a Master’s degree in Chemical Engineering from the University of Chester (UK). He currently works as a design engineering consultant for one of the largest engineering firms in the world along with being an associate member of the Institute of Chemical Engineers (IChemE).