Researchers at MIT have developed a more efficient process to mass manufacture polymer-coated nanoparticles for use in drug delivery. The research, which was published in Advanced Functional Materials, can be found below:
Pires, I. S., Gordon, E., Suh, H., Irvine, D. J., & Hammond, P. T. (2025). High‐Throughput Microfluidic‐Mediated Assembly of Layer‐By‐Layer Nanoparticles. Advanced Functional Materials. https://doi.org/10.1002/adfm.202503965
Over the past decade, Professor Paula Hammond’s lab at MIT has been exploring the layer-by-layer assembly of nanoparticles designed to transport therapeutic drugs directly to tumors. The usual assembly process involves sequential deposition of charged polymer layers; with each layer requiring a centrifugation step to remove excess material. While effective in small-scale experiments, this batch process posed challenges for large-scale production necessary for clinical applications.
Hammond and Darrell Irvine, a professor of immunology and microbiology at the Scripps Research Institute, are the senior authors of the new study along with postdoc at Brigham and Women’s Hospital and a visiting scientist at the Koch Institute, and Ezra Gordon ’24 are the lead authors of paper. Heikyung Suh, an MIT research technician, is also an author.
To address this, the researchers introduced a microfluidic mixing device. This device permits the continuous application of polymer layers as nanoparticles flow through microchannels, allowing precise calculation of the needed polymer for each layer. The elimination of manual mixing and repeated purification steps not only accelerates production but also aligns well with Good Manufacturing Practice (GMP) protocols. Hammond explained:
“There’s a lot of promise with the nanoparticle systems we’ve been developing, and we’ve been really excited more recently with the successes that we’ve been seeing in animal models for our treatments for ovarian cancer in particular, Ultimately, we need to be able to bring this to a scale where a company is able to manufacture these on a large level.”
The new method reduces production time. For example, generating 15 milligrams of nanoparticles; an amount approximating 50 doses, now takes only a few minutes, compared to nearly an hour with previous techniques. The streamlined process minimises the risk of operator error and maintains consistency across production runs, a needed improvement for scalability.
Recently, a graduate student in Hammond’s lab developed an alternative approach to purifying the particles, known as tangential flow filtration. However, while this streamlined the process, it still was limited by its manufacturing complexity and maximum scale of production. Hammond stated in regards to the recent alternative:
“Although the use of tangential flow filtration is helpful, it’s still a very small-batch process, and a clinical investigation requires that we would have many doses available for a significant number of patients,”
By integrating continuous process engineering with GMP-compliant production techniques, the research marks a move forwards in drug transport mechanisms. Ivan Pires, a postdoc at Brigham and Women’s Hospital and a visiting scientist at the Koch Institute explained:
“With the new approach, there’s much less chance of any sort of operator mistake or mishaps, This is a process that can be readily implemented in GMP, and that’s really the key step here. We can create an innovation within the layer-by-layer nanoparticles and quickly produce it in a manner that we could go into clinical trials with.”
Engineers have created a precise method for nanoparticle manufacturing that strikes a balance between medical application needs and manufacturing requirements. The new technique demonstrates promising potential for more efficient cancer therapy testing and deployment because it provides scalability alongside process integration alongside manufacturing standards compliance. The methods demonstrate that engineering approaches directly benefit therapeutic outcomes by achieving clinical validation.
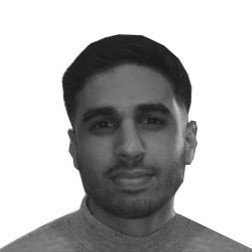
Hassan graduated with a Master’s degree in Chemical Engineering from the University of Chester (UK). He currently works as a design engineering consultant for one of the largest engineering firms in the world along with being an associate member of the Institute of Chemical Engineers (IChemE).