In a pioneering study, Kevin Chen, Suhan Kim, Yi-Hsuan (Nemo) Hsiao and their team are developing robotic insects designed to replicate the efficiency of natural pollinators, addressing critical challenges in agriculture. Their innovative approach combines bio-inspired design, advanced materials, and cutting-edge engineering to tackle issues such as declining pollinator populations and agricultural productivity in controlled environments.
Follow the main authors here:
- Suhan Kim MIT profile | Linkedin
- Kevin Chen MIT profile | Linkedin
- Yi-Hsuan (Nemo) Hsiao MIT profile | Linkedin
And see the full team involved here. A link to the related news report, which provides additional context for this interview, can be found here. The published paper in the Science Robotics Journal can be found here, referenced below.
Suhan Kim et al.,Acrobatics at the insect scale: A durable, precise, and agile micro–aerial robot.Sci. Robot.10,eadp4256(2025).DOI:10.1126/scirobotics.adp4256
The following interview is presented unedited to preserve Suhan Kim’s original responses and provide a deeper, unfiltered insight into his research on robotic insects. This format allows readers to fully grasp the technical nuances and potential impact of his work on the future of agriculture and environmental sustainability.
What are the key design features of these robotic insects that enable them to replicate the efficiency and precision of natural pollinators, such as bees?
Designing small and lightweight flying robots involves significant technical challenges. Traditional drones experience a dramatic drop in power-density when scaled down due to the limitations of electromagnetic motors, making them incapable of lifting their own weight. To address this, we take a completely different approach.
Specifically, our robot design draws inspiration from natural insects such as honeybees. We develop artificial muscles that are approximately 5 mm in size and weigh about 0.1 g. These muscles are far more power-dense than small motors, making them ideal for generating thrust for flight. On these muscles, we attach flapping-wing structures, mimicking the thrust generation of natural insects. A single muscle and a wing form a robotic module, and, like drones, four modules can be combined to enable controlled flight. This nature-inspired approach has allowed us to explore the ultra-lightweight domain, which traditional drone designs could not achieve, paving the way for new use cases such as artificial pollination.
Could you explain the technical challenges in achieving the 17-minute flight time and how innovations in energy storage or wing dynamics have contributed to overcoming these limitations?
Through extensive testing of previous robotic designs, we identified the wing hinge as the primary failure point. In prior designs, the hinge was located at the base of the wing, resulting in excessive mechanical stress due to the offset between the hinge and the center of aerodynamic pressure applied to the wing.
To address this, we redesigned the wing and hinge by extending the hinge along the wing’s leading edge. This new design aligns the hinge with the center of pressure, significantly reducing mechanical stress by over 100 times, as verified through simulations. The wing-hinge structure now demonstrates near-infinite durability, representing a major factor in the robot’s extended lifespan.
Additionally, we increased flight efficiency and lifespan by reducing the number of wings from eight to four, reinforcing the airframe, and resolving transmission bending issues. These mechanical design improvements were instrumental in overcoming the challenges of flight duration.
How does the robotic insect interact with flowers to ensure effective pollination without causing damage, and what mechanisms are in place to mimic natural pollination processes?
Artificial pollination is a future application we envision, though we have not conducted specific research on it yet. However, we can anticipate certain requirements for effective pollination. The robot must exert very delicate forces to interact with flower components such as petals and stamens, which requires a small and lightweight design. For example, current commercial drones, being relatively large, are unsuitable for such tasks.
Another critical factor is navigating densely clustered spaces without causing damage to either the robot or the plants. A key advantage of our robots, highlighted in our research, is their resilience to collisions due to the compliance of their artificial muscles and wings. This compliance minimizes the impact on objects upon collision. Moreover, our robots possess remarkable damage resilience, maintaining functionality even after sustaining significant damage, such as being punctured over 100 times with needles. This robustness is unparalleled among current flying robots and positions our design as highly suitable for delicate applications like artificial pollination.
What advancements in materials or fabrication techniques have been critical to creating lightweight and durable robotic insects suitable for real-world agricultural applications?
When we think of typical robot manufacturing process, one might imagine assembling components such as bolts, nuts, and linkages. However, our robots are fabricated in a completely different way. The primary materials come in the form factor of either liquid chemicals or thin films. These materials undergo processes such as mixing, heating, pressing, cutting, and assembling, involving over 10 distinct processes, all optimized for our specific robotic designs.
Building robots from raw materials is truly challenging, as it requires expertise across multiple domains. However, it offers a significant advantage: the ability to customize every detail. For instance, we can adjust the quantity of nanomaterials in our actuators to the microliter level, control polymer thickness to the micrometer scale, and incrementally modify the dimensions of micromachined flexible joints to optimize aerodynamic efficiency. This high level of customization has been a critical factor in designing and experimenting with innovative robotic systems.
How scalable is this technology for large-scale agricultural use, and what steps are being taken to ensure affordability and accessibility for farmers globally?
As mentioned earlier, starting from raw materials provides a cost advantage by enabling control over production costs. Additionally, the small size of the robots allows for batch fabrication of components without the need for large equipment, facilitating mass production.
One current challenge is the manual assembly required for certain fabrication steps. To address this, we are researching methods to standardize and automate these processes. With advancements in robotics and AI, we believe automation is achievable, which would naturally enable large-scale manufacturing. This progress would make the technology more accessible and affordable for farmers worldwide.
Could you discuss the potential environmental impacts of deploying robotic insects in ecosystems? How does the team ensure that these robots integrate safely with natural pollinators?
While our robotic design is inspired by natural pollinators such as bees, we do not intend to replace them, nor do we believe they can be fully substituted. Natural pollinators possess highly advanced wing and muscle structures that far surpass the capabilities of any artificial system. Additionally, preserving natural pollinators is critical, as they play an irreplaceable role in ecosystems.
However, two key scenarios highlight the potential role of our robots. First, the declining bee population poses a significant challenge for agriculture reliant on pollinators. In such cases, our robots could serve as a viable alternative. Second, certain agricultural environments, such as indoor vertical farms, are unsuitable for natural pollinators due to environmental or safety concerns. In these settings, our robots could complement natural pollinators rather than replace them, supporting agricultural productivity without disrupting ecosystems.
Looking ahead, what are the next stages of development for these robotic insects? Are there plans for field trials or collaborations with agricultural partners to test their effectiveness in diverse farming environments?
In the long term, we aim to collaborate with agricultural partners for field trials and diverse farming applications. However, from a technical perspective, we still have short-term milestones to achieve.
Our primary focus is on making the robot autonomous, similar to current commercial drones. Currently, our robot relies on external power through wires, external motion capture systems for position and orientation tracking, and external feedback control. Achieving autonomy requires integrating power, sensing, and control systems onboard the robot.
Developing ultra-lightweight batteries, sensors, and power circuits within the robot’s tight payload capacity is a formidable challenge. Nevertheless, we are making significant progress, and we hope to share more advancements soon. Creating autonomous robots will mark a critical step toward commercialization, enabling us to explore broader applications through collaborations in agricultural engineering.
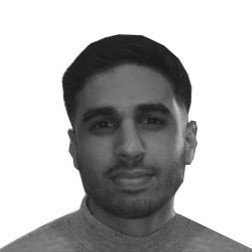
Hassan graduated with a Master’s degree in Chemical Engineering from the University of Chester (UK). He currently works as a design engineering consultant for one of the largest engineering firms in the world along with being an associate member of the Institute of Chemical Engineers (IChemE).