In a groundbreaking study, Matthew Bergschneider, McDermott Fellow and PhD candidate at UT Dallas, and Dr. Kyeongjae Cho, professor of materials science and engineering in the Erik Jonsson School of Engineering and Computer Science and director of the Batteries and Energy to Advance Commercialization and National Security (BEACONS), have taken major steps toward solving key degradation issues in LiNiO₂ cathodes; one of the most promising materials for high-energy lithium-ion batteries. We featured an news earlier report, we spoke with Bergschneider and Dr. Cho to explore the degradation mechanisms they uncovered, how their work addresses these challenges, and what this means for the future of battery performance and commercial scalability. You can see the published paper here:
Bergschneider, M., Kong, F., Conlin, P., Hwang, T., Doo, S., & Cho, K. (2024). Mechanical Degradation by Anion Redox in LiNiO 2 Countered via Pillaring. Advanced Energy Materials. https://doi.org/10.1002/aenm.202403837
Follow the Main Authors here:
- Dr. Kyeongjae Cho | Linkedin | Research Lab
- Matthew Bergschneider | Linkedin
The following interview is presented unedited to preserve Matthew’s original responses and offer readers a direct view into the thinking, motivations, and implications behind his work on sustainable fluorination techniques.
The original news feature from the UT Dallas website can be found here.
Acknowledgments from the Team: The research is a project of UTD’s BEACONS initiative, which launched in 2023 with $30 million from the Department of Defense. The BEACONS mission is to develop and commercialize new battery technology and manufacturing processes; enhance the domestic availability of critical raw materials; and train high-quality workers for jobs in an expanding battery-energy storage workforce.
Could you explain the fundamental mechanisms behind the degradation of LiNiO₂ cathodes in lithium-ion batteries, and how your research addresses these failure pathways?
A few coupled degradation mechanisms are most notable. Significantly, surface regions of the layered LiNiO2 (here “layered” refers to the atomic arrangement of the material bulk—alternating layers of Ni-O and Li-O are repeated throughout each grain of the material—and the lithium layers are vacated to charge the material) are vulnerable to a phase transformation that goes as:
- Nickel atoms migrate from their layer into the Li-layer. Later, when discharging (returning Li to the structure), Li can then move into the old Ni-site. These are so-called “cation mixing” processes, where the ideal layered structure is disrupted.
- Too much cation mixing yields a phase transition from the layered phase to the spinel phase. This (and even simple mixing) inhibits discharge, as it is more challenging for Li to return to the structure. In the spinel phase, Li is confined to smaller interstitial sites and some restricted motion.
- Evolving oxygen from the surface (resulting in sub-oxide NiOx) and finally,
- Densification and conversion to rock-salt structured NiO, which leaves no pathways for Li to pass into the bulk material below the surface.
This degradation pathway is troublesome, but is worsened when paired with the mechanism we seek to correct—large volume changes.
At deep charge states (charging to and above 4.3V vs Li metal reference electrode), a volume collapse of the bulk material occurs. This is linked to the Li-layer spacing, which contracts significantly at around this charge state, and so in anisotropic (not equal in all directions). Typically, cathode materials are polycrystalline particles, made up of many randomly oriented grains. This anisotropic volume change causes strain and eventual cracking of the particles, exposing new surface area. In cases with liquid electrolytes, the fresh surface area is attacked and undergoes the degradation pathway outlined above.
Our proposed doping is intended to mitigate the cause of the volume collapse, lessening its impact and preserving this cathode material at these previously inaccessible high charge states.
What role does the protective barrier layer play in mitigating structural degradation, and how does it improve the long-term stability of the battery during cycling?
By substituting a small portion of the lithium throughout the material with the dopants, it is modeled (by density functional theory) to provide compensation to oxygen that otherwise develop h+ (holes, lack of electrons) due to the negative charge transfer redox of the Ni-O complex at deep charge states. The compensating effect mitigates the Li interlayer spacing collapse, and strengthens it against deformation.
By lessening the volume change in particular, the particle’s integrity is maintained, and catastrophic failure, where cracks in the material became exposed to liquid electrolytes and prompted surface degradation, until whole particles deteriorated.
How does your solution impact the overall energy density, charging rates, and thermal stability of LiNiO₂-based batteries compared to conventional cathode materials?
Experimental validation is ongoing to quantifiably answer these questions.
What experimental or computational methods were critical in identifying and validating the degradation mechanisms at the atomic scale?
Density functional theory was the first-principles method applied in our published study. This atomic-scale modeling solves electron and nuclei behavior of e.g., a crystal structure, and allows for close analysis of structural and chemical processes, allowing study of phenomena such as the LiNiO2 degradation, and the impact of correcting schemes, enabling materials design.
How scalable is this protective layer technology for industrial battery production, and what challenges remain for its commercial adoption?
The proposed doping scheme does exhibit current challenges in material synthesis scaling, which we hope to explore more to enable commercial application.
Beyond electric vehicles and consumer electronics, are there other applications where this advancement in LiNiO₂ stability could have significant impact, such as grid storage or aerospace?
The high energy density of this material are particularly suited to mobile applications. This would indeed include aerospace or mobile robotics.
Looking ahead, what are the next steps for your research team in further optimising lithium-ion battery performance, and are there ongoing collaborations with industry partners to accelerate real-world implementation?
Experimental validation, compositional optimization for so-called “zero-strain” cathodes, and material synthesis scaling of these are ongoing endeavors and plans. If zero-strain (ΔV/V < 1%) conditions are met, application in all-solid-state batteries would be an exciting application.
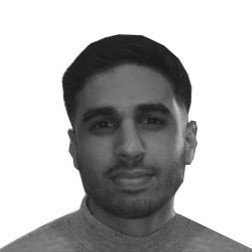
Hassan graduated with a Master’s degree in Chemical Engineering from the University of Chester (UK). He currently works as a design engineering consultant for one of the largest engineering firms in the world along with being an associate member of the Institute of Chemical Engineers (IChemE).