As the demand for metals in modern electronics and electric vehicles (EVs) continues to rise, repurposing spent batteries and other lithium recycling techniques are continuously being investigated. Not only does this reduce greenhouse gas emissions but it also conserves energy and water. A recent lifecycle analysis from Stanford University has quantified these advantages in clear numbers. The study showed that recycling processes emit less than half the greenhouse gases associated with mining virgin metals, while also requiring about one-fourth of the energy and water typically used in mining and refining using current industry techniques. The finding, published in Nature Communications can be found here:
Machala, M. L., Chen, X., Bunke, S. P., Forbes, G., Yegizbay, A., de Chalendar, J. A., Azevedo, I. L., Benson, S., & Tarpeh, W. A. (2025). Life cycle comparison of industrial-scale lithium-ion battery recycling and mining supply chains. Nature Communications, 16(1), 988. https://doi.org/10.1038/s41467-025-56063-x
Battery recycling primarily handles two streams: defective scrap directly from manufacturers and so-called “dead” batteries collected from workplace settings. This differentiation is important because the environmental impact of recycling is not uniform across these streams. The recycling process extracts lithium, nickel, cobalt, copper, manganese, and aluminum from these sources.
The recycling process’ environmental effect has been calculated, showing its emission of GHGs at only half the level thats is found in current mining and refining techniques used in industry, with usage of water and energy at 25% below mining fresh metals. Data indicates that the scrap stream, which comprises roughly 90% of the recycled material analysed, shows lower rates of greenhouse gas emissions, water, and energy consumption compared to that by new mining operations, coming in at: 19% of the GHG emissions of mining and processing, 12% of the water use, and 11% of the energy use.
“This study, I think, tells us that we can design the future of battery recycling to optimize the environmental benefits. We can write the script.”
Said William Tarpeh, assistant professor of chemical engineering in the School of Engineering at Stanford and the study’s senior author.
Transport logistics also plays a significant role. While mining of metals like cobalt and lithium involves long-distance transportation; sometimes covering tens of thousands of miles, the collection and refinement of used batteries involve much shorter distances. Studies estimate that recycling entails an average transport distance of around 140 miles (based on a presumed optimal location for future refining facilities), compared to roughly 35,000 miles for metals processed through traditional channels. This factor not only reduces emissions from transport but also lowers the associated economic and logistical burdens. Michael Machala, another lead author of the study said:
“We determined that the total transport distance for conventional mining and refining of just the active metals in a battery averages about 35,000 miles (57,000 kilometers). That’s like going around the world one and a half times,”
Recycling lithium-ion batteries could help address issues of supply security for critical metals. With global mining operations for minerals like cobalt and lithium concentrated in specific regions; such as the Democratic Republic of the Congo for cobalt and Australia and Chile for lithium, the recycling of batteries could alleviate some of the geopolitical and logistical challenges that arise from heavily centralised supply chains.
Despite the promising data and increasing industrial interest, the pace of industrial-scale battery recycling still lags behind demand. It is important to note that while around half of the U.S. lithium-ion batteries are currently recycled, the design and scale of recycling systems requires improvements to meet future needs. Tarpeh noted:
“For a future with a greatly increased supply of used batteries, we need to design and prepare a recycling system today from collection to processing back into new batteries with minimal environmental impact,”
By lowering greenhouse gas emissions, reducing energy and water usage, and shortening logistical chains, recycling technologies not only offer environmental benefits but also promise to ease long-term supply challenges in the evolving market for electric vehicles and renewable energy storage.
The research team was led by Stanford’s Chemical Engineering Assistant Professor William Tarpeh and his PhD student Samantha Bunke, supported by lead authors Michael Machala and Xi Chen; whose work continues at the Toyota Research Institute and City University of Hong Kong, respectively. The collaborative effort also included contributions from Stanford faculty Inês L. Azevedo and Sally Benson, Jacques A. de Chalendar, graduate student Gregory Forbes, and former Stanford intern Akarys Yegizbay.
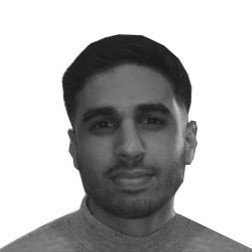
Hassan graduated with a Master’s degree in Chemical Engineering from the University of Chester (UK). He currently works as a design engineering consultant for one of the largest engineering firms in the world along with being an associate member of the Institute of Chemical Engineers (IChemE).