Aramid fibres which people know primarily from their use in bulletproof vests and clothing present significant obstacles during recycling operations. Aramid Fibres usually known as, Kevlar, exhibit exceptional strength along with durability. Sustainable methods to handle these materials and dispose has been causing issues for years. Several studies from the University of Groningen, NHL Stenden University of Applied Sciences, Teijin Aramid , along with coverage in multiple industry outlets, suggest that new microwave-assisted techniques may provide a path toward more efficient reuse.
Aramid is derived from a polymer called poly(p-phenylene terephthalamide), or PPTA. Recycling processes for PPTA rely on mechanical or chemical methods. Mechanical approaches reduce aramid to lower-quality material, and while chemical approaches can break it down to its core components, they often require high temperatures, high pressure, and organic solvents.
A study published in the Journal of the American Chemical Society on February 21 highlights a new technique using microwave reactors to depolymerise aramid fibers in as little as 15 minutes, all without the need for strong chemical solvents. You can view the research here:
Benninga, J., Gebben, B., Folkersma, R., Voet, V. S. D., & Loos, K. (2025). Rapid Microwave-Assisted Chemical Recycling of Poly( p -Phenylene Terephthalamide). Journal of the American Chemical Society, 147(9), 7191–7195. https://doi.org/10.1021/jacs.4c17791
Researchers observed a conversion rate of about 96 percent at lower temperatures than previously needed. This work was conducted in collaboration with Teijin Aramid, a major producer of aramid fibres, signalling possible real-world applications in coming years.
“Given the $2.9 billion aramid fibres market, this process could contribute to more sustainable material management and support closed-circle recycling initiatives in the industry,”
says Katja Loos, Professor of Macromolecular Chemistry and corresponding author of the JACS paper.
According to the researchers, the aim is to integrate their microwave process into existing manufacturing lines. Doing so could create a more sustainable pathway for end-of-life aramid products, from bulletproof vests to high-performance ropes and automotive components. Several composites-focused publications have underscored the significance of this advancement, noting how a streamlined depolymerisation process might encourage manufacturers to recover and repurpose aramid fibers.
Teijin Aramid has previously recognised the importance of closed-loop recycling for high-performance fibres. Representatives from the company have indicated that a commercially viable recycling method would help shrink the environmental footprint of aramid and keep pace with broader industrial sustainability initiatives. By potentially reintegrating raw components back into manufacturing, the approach could reduce both the waste stream and the costs associated with new aramid production.
While more testing is required to confirm the process’s scalability, the multi-partner collaboration represents a step toward a future in which bulletproof vests and other advanced aramid-based products have a second life. Studies underway at the University of Groningen will continue to refine the microwave process, with an eye on optimising reaction conditions and improving the overall rate of conversion.
Fibre manufacturers, polymer chemists, and government agencies are increasingly focused on cradle-to-cradle approaches. If successful, microwave depolymerisation may set a precedent for how other durable materials, such as carbon fibre or certain thermoplastics, could be recycled.
For those of us in the engineering sphere, it’s an encouraging example of how a small innovation; in this case, adapting chemical reactions to microwaves, can spur significant advances. All eyes will be on the final outcome of these collaborative studies to see if they can bring us closer to a sustainable cycle for high-performance materials.
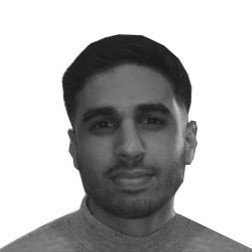
Hassan graduated with a Master’s degree in Chemical Engineering from the University of Chester (UK). He currently works as a design engineering consultant for one of the largest engineering firms in the world along with being an associate member of the Institute of Chemical Engineers (IChemE).