Follow Jeff Foster on LinkedIn or learn more about the research Jeff Foster and his team conduct at ORNL here. A link to the specific paper our earlier news report and this interview pertain to can be found here:
Foster, J. C., Damron, J. T., Zheng, J., Guan, C., Popovs, I., Rahman, Md. A., Galan, N. J., Dishner, I. T., & Saito, T. (2024). Polyalkenamers as Drop-In Additives for Ring-Opening Metathesis Polymerization: A Promising Upcycling Paradigm. Journal of the American Chemical Society, 146(48), 33084–33092. https://doi.org/10.1021/jacs.4c10588
In a groundbreaking study, Jeff Foster and his team at ORNL have developed an innovative “polymer editing” approach to upcycling plastic waste, transforming it into high-performance materials. As part of our continued coverage of this research, which we explored in a previous news feature, we spoke with Jeff Foster to gain deeper insights into the chemical mechanisms behind this upcycling process and its potential industrial impact.
The following interview is presented unedited to preserve Jeff Foster’s original responses, providing a direct and comprehensive look at the scientific and practical advancements of polymer editing. This format allows readers to fully understand the process, challenges, and future potential of this innovative recycling method.
Can you explain the key chemical process or “polymer editing” mechanism behind this upcycling method? How does it transform waste plastics into high-performance materials?
Polymer editing effectively inserts new material into the waste plastic through a combination of ring-opening polymerization and chain transfer. Briefly, a catalyst molecule randomly cleaves a polymer chain in the waste plastic, creating a new active site. This active site can then begin to elongate through the polymerization of cyclic monomer. The active site eventually exchanges with another polymer chain, continuing the insertion process. This continues until all of the cyclic monomer has been consumed, affording a population of polymer comprised of material derived from both the waste plastic and the newly polymerized monomers.
What types of plastics are most suitable for this upcycling process, and are there limitations in handling mixed or contaminated waste streams?
Any plastic that is comprised of polymers containing backbone functional groups is theoretically amenable to this process. Our initial demonstration used polyalkenamers such as polybutadiene and acrylonitrile butadiene styrene that possess reactive carbon-carbon double bonds. However, we have successfully expanded the scope of this process to other functional polymers and will report on these findings soon. Our process is well suited to mixed waste streams, as we can target specific functionalities that are present in some polymers but not others. Contamination is only problematic if the contaminants poison the relevant catalytic species that are used, although we have yet to encounter issues.
How does this method compare to existing recycling technologies in terms of efficiency, scalability, and the quality of the resulting materials?
Our polymer insertion method is highly atom economical and conserves the vast majority of the waste plastic matter that is added. Its scalability is only limited by the cost of the catalyst, solvent, and monomers used, which we have shown and will show in future works can be readily exchanged for a variety of economical options. The quality of the resulting material is significantly enhanced compared to mechanical recycling, for example because the molecular weight of the polymers produced by our method is generally increased after editing, resulting in enhanced thermomechanical performance.
Could you discuss the environmental impact of the upcycling process, particularly regarding energy consumption, emissions, and the reduction of landfill or ocean-bound plastic waste?
Our polymer editing process is highly energy efficient. The chemistries we have employed operate at relatively low temperatures (e.g., ≤ 40 °C), under ambient pressures, and do not produce toxic byproducts. We aim to ultimately use plastic waste as a feedstock to synthesize many chemicals and tailor-made materials, thereby reducing landfill or ocean-bound plastic waste.
What are the primary challenges in scaling this technology for industrial applications, and how is your team addressing these hurdles?
While we have yet to address scalability, we anticipate that potential hurdles could be the availability and cost of the transition metals used to catalyze polymer editing and the availability of recycled waste polymer that can be collected and separated. We note that recycling recovery rates for vulcanized rubbers are significantly higher than most plastics and thus we feel that there is potential to commercialize our process to address this waste stream, specifically.
Are there specific industries or applications where the high-performance materials produced through this method have the most potential for adoption?
Our process can produce materials ranging from tough thermoplastics to elastomers to adhesives to rubbers to thermosets. The specific industrial/application targets will arise (we hope) from interest and engagement by the private sector.
Looking ahead, what are the next steps for you and the ORNL team in advancing this technology? Are there collaborations or pilot projects underway to demonstrate its viability at a commercial scale?
We are currently exploring the scope of this technology to address other forms of plastic waste and developing pathways to directly produce a variety of materials from them. Included in these efforts are direct demonstrations of polymer editing starting from post-consumer plastic waste.
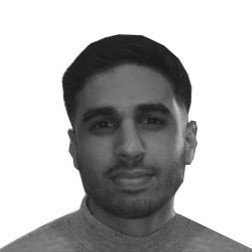
Hassan graduated with a Master’s degree in Chemical Engineering from the University of Chester (UK). He currently works as a design engineering consultant for one of the largest engineering firms in the world along with being an associate member of the Institute of Chemical Engineers (IChemE).