A research team of material scientists at Texas A&M University have successfully demonstrated a polymer film capable of resealing punctures smaller than the impacting particle by undergoing a reversible solid–liquid transition at the point of impact. The findings were published in the Materials Today journal and can be found here:
Sang, Z., Eoh, H., Xiao, K., Kurouski, D., Shan, W., Hyon, J., Sukhishvili, S. A., & Thomas, E. L. (2025). Supersonic puncture-healable and impact resistant covalent adaptive networks. Materials Today, 83, 43–53. https://doi.org/10.1016/j.mattod.2024.12.006
The material, classified as a Diels–Alder polymer (DAP) within covalent adaptive networks, breaks its dynamic covalent bonds under heat and mechanical strain, then reforms them once undergoing cooling. When a high-speed microparticle penetrates the film, much of the kinetic energy is absorbed as the polymer melts locally to the impact; once cooled, the bonds reassemble and leave a hole up to 30 percent smaller in diameter than the projectile.
Material scientists at Texas A&M University have developed just such a polymer with a unique self-healing property never before seen at any scale. When struck by a projectile, this material stretches so much that when the projectile manages to pass through, it takes only a small amount of the polymer with it. As a result, the hole left behind is much smaller than the projectile itself. Dr. Svetlana Sukhishvili, a professor in the Department of Materials Science and Engineering said:
“This is the first time a material at any scale has displayed this behaviour,”
To capture this behaviour, the team used laser-induced projectile impact testing (LIPIT), a method developed in collaboration with colleagues over at MIT. In these experiments, silica beads approximately 3.7 µm in diameter were laser-launched into polymer films just 75–435 nm thick. An ultrahigh-speed camera (3 ns exposure, 50 ns intervals) recorded the deformation, while scanning electron microscopy, laser scanning confocal microscopy and infrared nanospectroscopy verified the tiny perforations and rapid healing. Dr. Edwin Thomas, professor of materials science and engineering said:
“A major goal of our work was to see if we could simultaneously provide a material that would absorb a lot of kinetic energy per unit target mass from the high-speed projectile and be capable of very rapid healing of the punctured region, we wanted the post-impact material to still be capable of performing its intended function, such as carrying air or liquids and remaining sealed against the loss of such fluids across the material membrane.”
Micrometeoroids in low Earth orbit travel at about 10 km/s and can leave visible punctures in spacecraft windows. A DAP coating could reduce hole size and help maintain window integrity under such high-velocity impacts. On Earth, similar polymers may find use in flexible protective layers for satellites, unmanned vehicles or even next-generation body armor.
Scaling nanoscale healing to macroscopic materials poses a challenge: strain rates at larger scales differ by orders of magnitude. The team plans to explore variations in polymer composition, temperature response and the inclusion of catalysts to speed bond reformation. The ambition of the research team is to achieve multiple break–reform cycles within the microseconds of a ballistic event.
The work was carried out by a multidisciplinary team led by Dr. Svetlana Sukhishvili and Dr. Edwin Thomas of Texas A&M’s Department of Materials Science and Engineering, with nanoscale impact testing developed in collaboration with MIT. The polymer synthesis and LIPIT experiments were performed by Zhen Sang, now an engineer at Apple, alongside doctoral student Hongkyu Eoh. Postdoctoral researchers Dr’s. Kailu Xiao, Wenpeng Shan and Jinho Hyon carried out materials characterization, and Dr. Dmitry Kurouski of Texas A&M’s Biochemistry and Biophysics Department contributed infrared nanospectroscopic analysis.
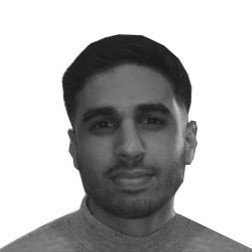
Hassan graduated with a Master’s degree in Chemical Engineering from the University of Chester (UK). He currently works as a design engineering consultant for one of the largest engineering firms in the world along with being an associate member of the Institute of Chemical Engineers (IChemE).