Key Takeaways
– Vibrating feeder design plays a crucial role in various industries.
– Understanding the principles of vibrating feeder design is essential for optimal performance.
– Factors such as material properties, feeder capacity, and operational requirements influence the design process.
– Proper maintenance and troubleshooting are necessary to ensure the longevity and efficiency of vibrating feeders.
– Advances in technology have led to the development of innovative vibrating feeder designs.
Introduction
Vibrating feeders are widely used in industries such as mining, construction, and manufacturing to transport and feed bulk materials. The design of vibrating feeders is crucial for ensuring efficient and reliable operation. This article explores the key aspects of vibrating feeder design, including principles, factors influencing design, maintenance, troubleshooting, and technological advancements.
Principles of Vibrating Feeder Design
Vibrating feeders operate based on the principle of electromagnetic vibration. An electromagnetic drive unit generates vibrations that transfer energy to the material being fed. The design of the feeder must consider factors such as the amplitude, frequency, and direction of vibrations to ensure proper material flow and prevent clogging or spillage.
Material Properties and Feeder Capacity
The design of a vibrating feeder must take into account the properties of the material being handled. Factors such as particle size, density, moisture content, and flowability influence the feeder’s capacity and design parameters. Understanding these material properties is crucial for selecting the appropriate feeder type and size.
Operational Requirements
The operational requirements of the application also play a significant role in vibrating feeder design. Factors such as required feed rate, feeding accuracy, and environmental conditions need to be considered. For example, in industries where precise feeding is critical, the feeder design may incorporate features such as adjustable feed rates and control systems.
Maintenance and Troubleshooting
Proper maintenance is essential for the longevity and efficiency of vibrating feeders. Regular inspection, cleaning, and lubrication of components help prevent wear and ensure smooth operation. Additionally, troubleshooting techniques such as vibration analysis and visual inspection can help identify and resolve issues such as misalignment, loose connections, or worn-out parts.
Common Issues and Solutions
Some common issues that may arise with vibrating feeders include material buildup, excessive noise, and erratic feeding. These issues can be addressed through measures such as installing anti-stick coatings, adjusting the feeder’s amplitude and frequency, and ensuring proper alignment of components. Regular monitoring and prompt troubleshooting can help prevent major problems and minimize downtime.
Technological Advancements in Vibrating Feeder Design
Advances in technology have led to the development of innovative vibrating feeder designs. For example, the integration of sensors and automation systems allows for real-time monitoring and control of feeders, optimizing their performance and reducing human intervention. Additionally, the use of advanced materials and manufacturing techniques enhances the durability and efficiency of vibrating feeders.
Application-Specific Designs
In recent years, vibrating feeder designs have become more tailored to specific applications. For instance, in the food industry, hygienic designs with easy-to-clean surfaces and FDA-approved materials are preferred. In the mining industry, heavy-duty feeders capable of handling large volumes and abrasive materials are in demand. These application-specific designs ensure optimal performance and meet industry standards.
Conclusion
Vibrating feeder design is a critical aspect of various industries, ensuring efficient and reliable material handling. Understanding the principles, considering factors such as material properties and operational requirements, and implementing proper maintenance and troubleshooting techniques are essential for optimal performance. Technological advancements continue to drive innovation in vibrating feeder design, leading to more efficient and application-specific solutions.
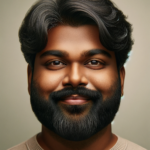
Adrian graduated with a Masters Degree (1st Class Honours) in Chemical Engineering from Chester University along with Harris. His master’s research aimed to develop a standardadised clean water oxygenation transfer procedure to test bubble diffusers that are currently used in the wastewater industry commercial market. He has also undergone placments in both US and China primarely focused within the R&D department and is an associate member of the Institute of Chemical Engineers (IChemE).