In recent years, materials science has advanced to the point where interlocking metasurfaces (ILMs) composed of 3D printed shape memory alloys (SMAs) provide a new way to create structural integration with minimal fasteners.
Nickel Titanium (NiTi) shape memory alloys are known for their ability to heat, and then return to their original predetermined shape. Additive manufacturing techniques have been successfully taking advantage of this property to create complex geometries with precise control over the material properties. Researchers at Texas A&M University and Sandia National Laboratories have used these capabilities to build ILMs that can be selectively engaged and disengaged through temperature changes, which enable adaptable and reconfigurable joints.
“ILMs are poised to redefine joining technologies across a range of applications, much like Velcro did decades ago,”
stated Dr. Ibrahim Karaman, professor and head of the Department of Materials Science and Engineering at Texas A&M University.
“Our research demonstrates that these ILMs can be selectively disengaged and re-engaged on demand while maintaining consistent joint strength and structural integrity.”
Importantly, SMAs integrate into ILMs across many industries. This technology could enable aerospace engineering assembly and disassembly of components without loss of structural integrity, making maintenance easier and reducing assembly time. In robotics, SMA based ILMs may have advantages in providing more flexible and responsive robotic joints, providing better functionality and performance. Moreover, in the biomedical scene, the ability to create adjustable implants or prosthetics that fit to the body’s motion and temperature fluctuations could increase benefits in terms of patient outcomes and comfort.
Although promising, these advancements face the challenge of fully optimising the superelastic properties of 3D printed SMAs to resist large deformations and recover in high stress. These issues are being addressed by ongoing research and the hope is that SMA-based ILMs can be applied to applications in environments that require it to have extremely good performance and reliability.
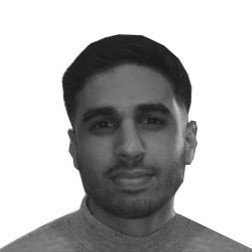
Hassan graduated with a Master’s degree in Chemical Engineering from the University of Chester (UK). He currently works as a design engineering consultant for one of the largest engineering firms in the world along with being an associate member of the Institute of Chemical Engineers (IChemE).