Follow Dr. Olawumi Sadare on LinkedIn or learn more about the research Dr. Sadare and her team conduct at the University of Bath here. A link to the specific paper our earlier news report and this interview pertain to can be found here:
Sadare, O., Zoumpouli, G. A., Chew, Y. M. J., Wenk, J., Castro-Dominguez, B., & Mattia, D. (2025). Lignin- and Cellulose-Derived Sustainable Nanofiltration Polyelectrolyte Membranes. ACS Sustainable Chemistry & Engineering, 13(5), 2060–2071. https://doi.org/10.1021/acssuschemeng.4c08611
In a groundbreaking study, Dr. Olawumi Sadare and her team have developed plant-based membranes for water filtration, providing a sustainable alternative to fossil fuel-derived membranes. This innovative approach not only enhances water purification efficiency but also supports environmentally friendly practices within the water treatment industry. As part of our in-depth look at this advancement, which we covered earlier in our news feature, we spoke with Dr. Sadare to gain further insight into her research and its potential impact.
The following is a brief outline of the team and their roles in the research along with their Bath University profile and Linkedin for you to follow their next steps in their careers:
- Dr Sadare Olawumi (Royal Society Newton International Fellow) | Linkedin
- Writing: Original draft, Methodology, Investigation, Analysis, Conceptualization, Funding acquisition.
- Dr Liana Zoumpouli (Research Associate, Dept. of Chemical Engineering, University of Bath) | Linkedin
- Writing: review & editing, Analysis.
- Prof. John Chew (Deputy Dean Faculty of Engineering and Design, University of Bath) | Linkedin
- Writing: review & editing, Supervision, Resources, Conceptualization.
- Prof. Davide Mattia (Professor, Dept. of Chemical Engineering, University of Bath) | Linkedin
- Writing: review & editing, Supervision, Resources, Funding acquisition, Conceptualization.
- Dr Jannis Wenk (Senior lecturer, Dept. of Chemical Engineering, University of Bath) | Linkedin
- Writing: review & editing, Supervision.
- Dr Bernardo Castro-Dominguez (Senior lecturer, Dept. of Chemical Engineering, University of Bath) | Linkedin
- Writing: Review & editing, Supervision.
The following interview is presented unedited to preserve Dr. Sadare’s original responses and offer a deeper, unfiltered understanding of her work on plant-based membrane filtration. This format allows readers to fully appreciate the intricacies and significance of her contributions to sustainable water treatment technologies.
Acknowledgement From Dr. Olawumi Sadare: O.S. acknowledges the Royal Society for financial support via a Newton International Fellowship (NIF/R1/221820). The authors are grateful to the EPSRC for funding (EP/ V047078/1). The authors acknowledge the Material and Chemical Characterisation Facility (MC2), Core research facility, and the Faculty of Engineering & Design technical services at the University of Bath for assistance in collecting the data presented in the study.
Could you explain the key structural and chemical properties of the plant-based membranes that allow them to function as effective filtration materials without relying on fossil fuel-derived polymers?
The plant-based membranes leverage the unique structural and chemical properties of lignin and cellulose to achieve effective filtration without fossil fuel-derived polymers. Lignin’s aromatic backbone ensures chemical stability, while the hydrophilic nature of both cationic lignin and sodium carboxymethyl cellulose (NaCMC) enhances their suitability for water purification membranes. The strong electrostatic interactions between these polyelectrolytes, controlled through precise pH adjustments, create a stable and selective multilayer barrier that effectively rejects charged contaminants. Additionally, the layer-by-layer (LBL) assembly technique enables fine-tuning of membrane thickness and pore size, optimizing permeability and selectivity for nanofiltration applications.
How does the filtration performance of these membranes compare to conventional polymeric membranes in terms of selectivity, permeability, and durability?
The manufactured polyelectrolyte membrane exhibited a higher pure water permeance than some commercial regenerated cellulose membranes. It achieved a molecular weight cutoff (MWCO) of 300–620 Da, making it a loose nanofiltration membrane. The membrane showed high selectivity, rejecting 93% of positively charged methylene blue and 96% of negatively charged reactive orange-16, comparable to the commercial Regenerated cellulose membrane. Additionally, it maintained excellent stability after 30 days in water, highlighting its durability. These results suggest that PEMs offer a sustainable alternative with comparable separation efficiency to conventional NF membranes. While its rejection performance aligns with commercial alternatives, further long-term studies are needed to assess steady-state behaviour and potential performance variations.
What challenges did your team face in designing a membrane that does not require toxic solvents in its fabrication process, and how were these challenges overcome?
One challenge was, determining the optimal pH conditions for strong electrostatic interactions between cationic lignin and NaCMC, as improper pH balance could weaken layer adhesion and membrane stability. This was overcome by carefully adjusting the pH of the polyelectrolyte solutions to ensure complete ionization, allowing for robust layer-by-layer assembly. Another challenge was achieving uniform deposition, which was addressed by optimizing dipping times and salt concentrations to enhance polyelectrolyte binding and membrane performance.
Can you discuss the biodegradability or end-of-life management of these plant-based membranes? How do they contribute to a more sustainable water treatment industry?
The plant-based membranes, made from lignin and cellulose, are designed to be more environmentally friendly than fossil fuel-derived alternatives. While all-lignin membranes containing cationic lignin have been reported to be biodegradable, and sodium carboxymethyl cellulose (NaCMC) is known to be biodegradable, further research is required to verify the biodegradability of the lignin-cellulose membrane as a whole. At the end of their lifecycle, these membranes have the potential to degrade naturally or be repurposed through controlled composting or bio-based recycling processes. Their sustainable fabrication and degradability align with circular economy principles, offering a greener alternative for water treatment while minimising plastic waste and toxic solvent pollution.
Are there specific water contaminants or industrial applications where these membranes perform exceptionally well, or are they intended to be a general replacement for current membrane technologies?
These membranes perform exceptionally well in removing charged contaminants such as dyes (e.g., methylene blue and reactive orange-16) and small organic molecules, making them ideal for wastewater treatment applications. Their tunable molecular weight cutoff (300–620 Da) allows for selective separation in nanofiltration processes, particularly in industries dealing with dye removal, protein separation, and organic pollutant filtration. While they offer a sustainable alternative to conventional membranes, their specific advantages in charged solute rejection suggest they are best suited for targeted applications rather than a complete replacement for all existing membrane technologies.
How scalable is the production of these membranes, and what are the key factors that need to be addressed for large-scale commercial implementation?
The production of these membranes is scalable due to the layer-by-layer (LBL) assembly method, which allows precise control over membrane properties and can be adapted for roll-to-roll manufacturing. However, key factors for large-scale commercial implementation include optimizing deposition techniques for continuous and high-throughput fabrication, ensuring long-term membrane stability under diverse water treatment conditions, and reducing material costs while maintaining performance. Additionally, regulatory approvals, industry partnerships, and pilot-scale testing are essential to validate efficiency and accelerate market adoption.
Looking forward, what are the next steps in optimising this technology? Are there ongoing collaborations with industry partners or government agencies to bring plant-based membrane filtration to market?
The next steps in optimizing this technology include enhancing membrane durability, improving rejection efficiency for a broader range of contaminants, and scaling up the fabrication process for industrial applications. Further research will focus on refining the layer-by-layer (LBL) assembly method to increase production efficiency and exploring surface modifications to enhance antifouling properties.
Yes, a patent application has been filed for this innovation, and discussions are ongoing with industry partners for potential commercialisation, aiming to bring plant-based membrane filtration to the market.
While the study highlights the feasibility of plant-based membranes, further work is needed to refine manufacturing techniques and conduct long-term field testing for real-world deployment.
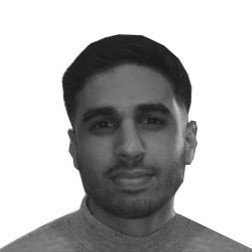
Hassan graduated with a Master’s degree in Chemical Engineering from the University of Chester (UK). He currently works as a design engineering consultant for one of the largest engineering firms in the world along with being an associate member of the Institute of Chemical Engineers (IChemE).