Concrete, the backbone of our modern infrastructure, is undergoing a revolutionary transformation thanks to cutting-edge advancements in robotics and additive manufacturing. Long celebreated for its strength, traditional concrete has its flaws, chief among them, a susceptibility to cracking under stress. But now, researchers are taking inspiration from nature and using innovative technologies to produce tougher, more resilient concrete that could redefine how we build everything from skyscrapers to bridges.
Princeton University’s engineering team, led by Reza Moini, recently unveiled a breakthrough method to enhance the crack resistance of concrete by up to 63% compared to standard methods. This was done by looking at a bio-inspired design mimicking the ancient coelacanth fish, known for its resilient, scale-like structure. By adopting this “double-helical” arrangement, the researchers created a concrete composition that not only resists cracking but also prevents cracks from spreading once they form.
The use of additive manufacturing, 3D printing on a grand scale, coupled with robotics has made this advancement possible. Traditional concrete casting limits design flexibility and structural complexity, but additive manufacturing opens the door to innovative architectures. The team used robots to deposit concrete strand by strand, precisely controlling the material’s curing process. This approach allowed for a layered, interlocking design that improves the concrete’s structural integrity without sacrificing its aesthetic potential.
What makes this development particularly exciting is the combination of robotics and chemistry. The robotic system employed by Moini’s lab uses an advanced nozzle to mix concrete with a chemical accelerator just before deposition, enabling faster curing times and ensuring geometric stability throughout the process. This eliminates one of the biggest hurdles in large-scale concrete 3D printing; deformation caused by the weight of the material during the building process.
Shashank Gupta, a graduate student at Princeton and co-author of the work stated:
Creating architected concrete material with the necessary high geometric fidelity at scale in building components such as beams and columns sometimes requires the use of robots. This is because it currently can be very challenging to create purposeful internal arrangements of materials for structural applications without the automation and precision of robotic fabrication.
The implications of this technology are vast. Additive manufacturing, already praised for its potential in reducing construction waste and enabling more sustainable building practices, could now lead to even longer-lasting infrastructure. From urban mega projects to remote construction sites where labour and resources are limited.
The construction industry is on the cusp of a major shift, where age-old materials like concrete are reimagined with modern technology. As robotic systems grow more sophisticated and the possibilities for architected designs expand, we may soon witness a future where buildings are not only more durable but also more sustainable and visually striking.
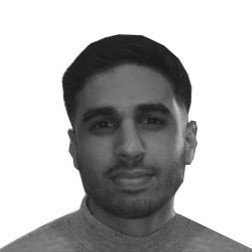
Hassan graduated with a Master’s degree in Chemical Engineering from the University of Chester (UK). He currently works as a design engineering consultant for one of the largest engineering firms in the world along with being an associate member of the Institute of Chemical Engineers (IChemE).