Key Takeaways
– Metal casting is a versatile manufacturing process used to create complex metal parts.
– The basics of metal casting involve melting metal, pouring it into a mold, and allowing it to solidify.
– Different types of molds, such as sand molds and investment molds, are used in metal casting.
– Metal casting has been used for centuries and continues to be an important method in various industries.
– Understanding the basics of metal casting can help individuals appreciate the intricacies of this ancient technique.
Introduction
Metal casting is a fascinating manufacturing process that has been used for centuries to create a wide range of metal parts. From intricate jewelry pieces to massive industrial components, metal casting offers a versatile and efficient method of production. In this article, we will explore the basics of metal casting, including the different types of molds used, the steps involved in the casting process, and the significance of this technique in various industries.
The Types of Molds Used in Metal Casting
One of the key elements in metal casting is the mold. A mold is a hollow cavity into which molten metal is poured to create the desired shape. There are several types of molds used in metal casting, each with its own advantages and applications.
Sand Molds
Sand molds are the most common type of molds used in metal casting. They are made by compacting sand around a pattern, which is a replica of the desired part. The sand is then hardened to create a rigid mold. Sand molds are versatile and can be used to cast both ferrous and non-ferrous metals. They are relatively inexpensive and can be reused multiple times, making them a cost-effective choice for many casting applications.
Investment Molds
Investment molds, also known as lost-wax casting, are used for more intricate and detailed parts. This process involves creating a wax pattern of the desired part, which is then coated with a ceramic shell. The wax is melted out, leaving behind a cavity that is filled with molten metal. Investment molds allow for greater precision and finer details, making them ideal for jewelry and art casting. However, they are more expensive and time-consuming compared to sand molds.
The Metal Casting Process
The metal casting process involves several steps, starting from the preparation of the mold to the final finishing of the cast part. Here is a brief overview of the key steps involved:
Mold Preparation
The first step in metal casting is preparing the mold. This includes creating or selecting the appropriate mold material, such as sand or investment material, and ensuring it is properly shaped and prepared to receive the molten metal.
Melting the Metal
Once the mold is ready, the next step is melting the metal. The metal is heated to its melting point in a furnace, and any impurities are removed through various refining processes. The molten metal is then poured into the mold.
Solidification and Cooling
After the metal is poured into the mold, it begins to solidify and take the shape of the mold cavity. The cooling process is carefully controlled to ensure proper solidification and minimize defects in the cast part.
Part Removal and Finishing
Once the metal has solidified and cooled, the mold is removed, and the cast part is extracted. The part may require additional finishing processes, such as trimming excess material, sanding, polishing, or heat treatment, to achieve the desired final product.
The Significance of Metal Casting
Metal casting has played a crucial role in various industries throughout history. From ancient civilizations to modern manufacturing, metal casting has been used to create tools, weapons, decorative objects, and industrial components. The ability to create complex shapes and intricate details makes metal casting a preferred method for producing parts that are difficult or impossible to manufacture using other techniques.
Automotive Industry
In the automotive industry, metal casting is used to produce engine blocks, cylinder heads, transmission components, and other critical parts. The ability to cast these parts in a single piece reduces the need for assembly and improves overall performance and durability.
Aerospace Industry
Metal casting is also vital in the aerospace industry, where lightweight yet strong components are required. Casting allows for the creation of complex shapes and intricate internal structures, making it possible to produce parts with high strength-to-weight ratios.
Art and Jewelry
Metal casting has long been used in art and jewelry to create unique and intricate pieces. The ability to capture fine details and create custom designs makes casting a preferred method for artists and jewelers.
Conclusion
Metal casting is a fascinating and versatile manufacturing process that has stood the test of time. From sand molds to investment molds, the different types of molds used in metal casting offer a range of possibilities for creating complex metal parts. Understanding the basics of metal casting allows us to appreciate the skill and craftsmanship involved in this ancient technique. Whether it’s in the automotive industry, aerospace sector, or the world of art and jewelry, metal casting continues to play a significant role in shaping our modern world.
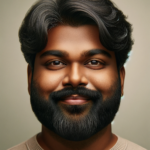
Adrian graduated with a Masters Degree (1st Class Honours) in Chemical Engineering from Chester University along with Harris. His master’s research aimed to develop a standardadised clean water oxygenation transfer procedure to test bubble diffusers that are currently used in the wastewater industry commercial market. He has also undergone placments in both US and China primarely focused within the R&D department and is an associate member of the Institute of Chemical Engineers (IChemE).