Key Takeaways
- The FBD process is a widely used method in the pharmaceutical industry for drying and granulation.
- It involves the use of a fluidized bed to suspend and agitate particles, allowing for efficient drying and granulation.
- The FBD process offers several advantages, including uniform drying, improved product quality, and reduced drying time.
- Proper control and monitoring of process parameters are crucial for achieving optimal results in the FBD process.
- Regular maintenance and cleaning of the fluidized bed equipment are essential to ensure its efficient operation.
Introduction
The FBD (Fluidized Bed Drying) process is a widely used technique in the pharmaceutical industry for drying and granulation. It involves the use of a fluidized bed, where particles are suspended and agitated by a stream of air or gas. This article will explore the FBD process in detail, discussing its principles, applications, advantages, and key considerations for optimal operation.
Principles of the FBD Process
The FBD process operates on the principle of fluidization, where a bed of solid particles is transformed into a fluid-like state by passing a gas or liquid through it. In the case of the FBD process, air or gas is used to fluidize the bed of particles. This fluidization creates a turbulent and agitated environment, allowing for efficient heat and mass transfer.
Fluidization and Particle Suspension
When the gas or air velocity is increased, it reaches a point where the drag force exerted on the particles overcomes their weight, causing them to become suspended in the fluidized bed. This suspension allows for uniform contact between the particles and the drying or granulating medium, ensuring efficient heat and mass transfer.
Heat and Mass Transfer
The fluidized bed provides an ideal environment for heat and mass transfer due to its high surface area and efficient mixing. As the particles are suspended and agitated, the drying or granulating medium can penetrate the bed, rapidly transferring heat to the particles and evaporating moisture. Similarly, during granulation, the binder solution can evenly coat the particles, leading to uniform granule formation.
Applications of the FBD Process
The FBD process finds extensive applications in the pharmaceutical industry, particularly in the drying and granulation of pharmaceutical powders and granules. Some common applications include:
Drying of Active Pharmaceutical Ingredients (APIs)
The FBD process is widely used for drying APIs, ensuring their stability and shelf-life. The fluidized bed allows for uniform drying, preventing the formation of hot spots and ensuring consistent product quality.
Granulation of Pharmaceutical Powders
The FBD process is also employed for granulation, where fine powders are transformed into granules with improved flowability, compressibility, and uniformity. The fluidized bed facilitates the even distribution of the binder solution, leading to uniform granule formation.
Advantages of the FBD Process
The FBD process offers several advantages over other drying and granulation methods:
Uniform Drying
The fluidized bed ensures uniform contact between the drying medium and the particles, resulting in uniform drying throughout the bed. This eliminates the risk of over-drying or under-drying, leading to consistent product quality.
Improved Product Quality
The FBD process allows for precise control over process parameters, such as temperature, airflow, and residence time. This control ensures that the drying or granulation process is optimized, leading to improved product quality with desired characteristics.
Reduced Drying Time
The efficient heat and mass transfer in the fluidized bed significantly reduce the drying time compared to other methods. This not only improves productivity but also minimizes the risk of degradation or loss of volatile components in the product.
Considerations for Optimal FBD Process
To achieve optimal results in the FBD process, several key considerations should be taken into account:
Process Parameters
Proper control and monitoring of process parameters, such as temperature, airflow, and residence time, are crucial for achieving the desired drying or granulation outcomes. Regular calibration and adjustment of equipment are necessary to maintain optimal process conditions.
Equipment Maintenance
Regular maintenance and cleaning of the fluidized bed equipment are essential to ensure its efficient operation. This includes cleaning the filters, inspecting the nozzles, and checking for any signs of wear or damage. Proper maintenance helps prevent equipment malfunction and ensures consistent performance.
Conclusion
The FBD process is a widely used method in the pharmaceutical industry for drying and granulation. It offers several advantages, including uniform drying, improved product quality, and reduced drying time. Proper control and monitoring of process parameters, as well as regular equipment maintenance, are crucial for achieving optimal results in the FBD process. By understanding the principles and applications of the FBD process, pharmaceutical manufacturers can enhance their drying and granulation processes, leading to high-quality products and improved efficiency.
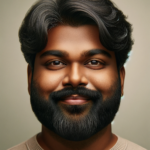
Adrian graduated with a Masters Degree (1st Class Honours) in Chemical Engineering from Chester University along with Harris. His master’s research aimed to develop a standardadised clean water oxygenation transfer procedure to test bubble diffusers that are currently used in the wastewater industry commercial market. He has also undergone placments in both US and China primarely focused within the R&D department and is an associate member of the Institute of Chemical Engineers (IChemE).