Key Takeaways
– An aggregate screener is a valuable tool used in various industries to separate and sort different types of materials.
– The use of an aggregate screener can improve efficiency and productivity in construction, mining, and recycling operations.
– There are different types of aggregate screeners available, including vibrating screeners, trommel screeners, and scalping screeners.
– Factors to consider when choosing an aggregate screener include the type of material, desired output, and specific application requirements.
– Regular maintenance and proper operation of an aggregate screener are essential for optimal performance and longevity.
Introduction
In various industries such as construction, mining, and recycling, the process of separating and sorting different types of materials is crucial for efficient operations. One tool that plays a significant role in this process is the aggregate screener. An aggregate screener is a machine designed to separate and classify aggregates based on their size, shape, and other characteristics. This article will explore the importance of aggregate screeners, the different types available, and key considerations when choosing one for specific applications.
The Importance of Aggregate Screeners
Aggregate screeners are essential in industries where the separation and classification of materials are necessary. These machines help improve efficiency and productivity by automating the process of sorting aggregates. By using an aggregate screener, operators can save time and labor, as the machine can handle large volumes of materials in a shorter period. Additionally, the use of an aggregate screener ensures consistent and accurate separation, resulting in higher-quality end products.
Types of Aggregate Screeners
There are several types of aggregate screeners available, each designed for specific applications and material types. One common type is the vibrating screener, which uses vibrating screens to separate aggregates based on size. Vibrating screeners are versatile and can handle a wide range of materials, making them suitable for various industries.
Another type is the trommel screener, which consists of a rotating drum with perforated screens. As the drum rotates, the smaller materials pass through the screens, while the larger ones are discharged at the end. Trommel screeners are commonly used in mining and recycling operations, where the separation of different-sized materials is crucial.
Scalping screeners, on the other hand, are designed to remove oversized materials from the feed stream. These screeners have larger openings and are typically used as the first step in the screening process. By removing oversized materials, scalping screeners help prevent damage to downstream equipment and ensure efficient operation.
Considerations When Choosing an Aggregate Screener
When selecting an aggregate screener, several factors should be taken into account to ensure the machine meets specific requirements. One important consideration is the type of material to be screened. Different materials have varying characteristics, such as size, shape, and moisture content, which can affect the performance of the screener. It is crucial to choose a screener that is capable of handling the specific material effectively.
Another factor to consider is the desired output or production rate. The capacity of the screener should match the required throughput to avoid bottlenecks and maximize productivity. Additionally, the size and configuration of the screener should be suitable for the available space and operational requirements.
Other considerations include the ease of maintenance and operation, as well as the availability of spare parts and technical support. Regular maintenance and proper operation are essential for the optimal performance and longevity of the screener.
Proper Maintenance and Operation
To ensure the longevity and optimal performance of an aggregate screener, regular maintenance and proper operation are crucial. This includes routine inspections, cleaning, and lubrication of the machine. It is also important to follow the manufacturer’s guidelines and recommendations for maintenance tasks.
Proper operation of the screener involves adjusting the settings and parameters according to the specific material and desired output. This may include adjusting the screen angle, vibration intensity, and feed rate. Operators should be trained on the proper operation of the screener to maximize its efficiency and prevent unnecessary wear and tear.
Conclusion
Aggregate screeners play a vital role in various industries by automating the process of separating and sorting different types of materials. They improve efficiency, productivity, and the quality of end products. When choosing an aggregate screener, factors such as material type, desired output, and specific application requirements should be considered. Regular maintenance and proper operation are essential for optimal performance and longevity. By understanding the importance of aggregate screeners and making informed choices, industries can enhance their operations and achieve better results.
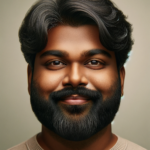
Adrian graduated with a Masters Degree (1st Class Honours) in Chemical Engineering from Chester University along with Harris. His master’s research aimed to develop a standardadised clean water oxygenation transfer procedure to test bubble diffusers that are currently used in the wastewater industry commercial market. He has also undergone placments in both US and China primarely focused within the R&D department and is an associate member of the Institute of Chemical Engineers (IChemE).