Key Takeaways
– A vibratory grinder is a versatile tool used for various grinding and polishing applications.
– It uses vibration and abrasive media to remove material and achieve a smooth finish.
– Vibratory grinders are commonly used in industries such as metalworking, automotive, and jewelry making.
– They offer advantages such as faster material removal, reduced manual labor, and improved surface quality.
– Proper maintenance and safety precautions are essential for optimal performance and operator safety.
Introduction
A vibratory grinder is a powerful and efficient tool used in various industries for grinding, polishing, and finishing applications. It utilizes vibration and abrasive media to remove material and achieve a smooth surface finish. This article will explore the features, benefits, and applications of vibratory grinders, as well as provide insights into their maintenance and safety considerations.
The Working Principle of Vibratory Grinders
Vibratory grinders operate on the principle of vibration. The machine consists of a bowl or chamber that holds the workpiece and abrasive media. When the machine is turned on, it generates vibrations that cause the media to move and interact with the workpiece. This movement creates friction, which results in material removal and surface refinement.
Advantages of Vibratory Grinders
Vibratory grinders offer several advantages over traditional grinding methods. Firstly, they provide faster material removal rates, allowing for increased productivity and shorter processing times. Additionally, the vibration action of the machine reduces the need for manual labor, as the media does most of the work. This not only saves time but also reduces operator fatigue.
Applications of Vibratory Grinders
Vibratory grinders find applications in various industries. In metalworking, they are used for deburring, descaling, and surface preparation of metal parts. The automotive industry utilizes vibratory grinders for polishing and finishing automotive components, such as engine parts and body panels. Jewelry makers also rely on vibratory grinders for polishing and cleaning precious metals and gemstones.
Maintenance and Safety Considerations
To ensure optimal performance and longevity of a vibratory grinder, regular maintenance is crucial. This includes cleaning the machine after each use, inspecting and replacing worn-out parts, and lubricating moving components. It is also important to follow the manufacturer’s guidelines for media selection and machine settings to prevent damage and achieve desired results.
Safety Precautions
When operating a vibratory grinder, certain safety precautions must be followed. Operators should wear appropriate personal protective equipment, such as safety glasses, gloves, and ear protection. The machine should be placed on a stable surface and securely fastened to prevent movement during operation. It is also important to avoid overloading the machine and to keep hands and clothing away from moving parts.
Conclusion
Vibratory grinders are versatile tools that offer numerous benefits in grinding, polishing, and finishing applications. Their ability to remove material quickly, reduce manual labor, and improve surface quality makes them indispensable in industries such as metalworking, automotive, and jewelry making. By following proper maintenance procedures and adhering to safety precautions, operators can maximize the performance and longevity of vibratory grinders while ensuring their own safety.
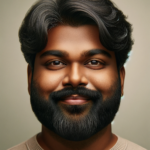
Adrian graduated with a Masters Degree (1st Class Honours) in Chemical Engineering from Chester University along with Harris. His master’s research aimed to develop a standardadised clean water oxygenation transfer procedure to test bubble diffusers that are currently used in the wastewater industry commercial market. He has also undergone placments in both US and China primarely focused within the R&D department and is an associate member of the Institute of Chemical Engineers (IChemE).