Centrifugal pumps are an important part of current engineering applications. They do crucial work moving liquids from water supply systems to industrial processes efficiently. In the particular area of application; the global pump market, it is extremely important to grasp the ‘how’, to choose the best machine for our system, and to take best advantage of these investments through optimised performance. In this in-depth guide, we’ll cover everything you need to know about centrifugal pumps, including their types, features, design considerations, and even an easy-to-use pump calculation tool.
What Is A Centrifugal Pump?
A centrifugal pump is a mechanical device designed to move fluids by converting rotational kinetic energy into hydrodynamic energy. It operates through the action of one or more driven rotors known as impellers, which increases the fluid’s velocity as it spins. Fluid enters the rotating impeller along it’s axis and is ejected by centrifugal force along it’s circumference through the impellers vane tips. This increased velocity is then converted into pressure, allowing the fluid to be transported through a piping system. Special design of the pump casing is such that the pump fluid is conveyed from pump inlet into impeller, then slowed and controlled before discharge.
These pumps are ideal for low-viscosity fluids such as water, fuel, or chemicals. However, their versatility makes them applicable in many industries, from agriculture to oil and gas.
For more information and a more indepth look into Centrifugal Pumps, check out this book for more information:
How Centrifugal Pumps Work
Centrifugal pump has an important component, known as the impeller. It is made from a series of curved vanes. They usually sandwich between two discs (an enclosed impeller). For slurry fluids an open or semi-open impeller backed by a single disc is preferred.
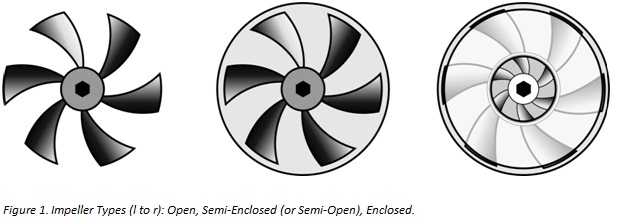
At the ‘eye’ of the impeller fluid goes in, and comes out around the vanes in the circumference. On the opposite side to the eye there is an impeller, which is connected to a motor and rotated at high speed (around 500-5000rpm) through a drive shaft. The fluid is thereby accelerated out through the impeller vanes into the pump casing at high rotational speed.
There are two basic designs of pump casing: volute and diffuser. We want a controlled discharge at pressure in both designs.
The impeller is situated in a volute casing, which acts to offset the impeller and in effect produce a curved funnel of increasing cross-sectional area to the pump outlet. This design leads to a pressure difference, increasing the pressure towards the outlet.
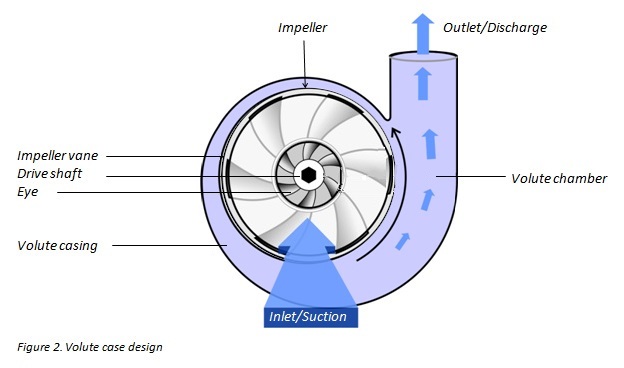
The same basic principle applies to diffuser designs. In this case, a set of stationary vanes surround the impeller with fluid being expelled between the two. Since diffuser designs can be tailored for particular applications, more efficient ones can be designed. When it is desirable to avoid the increased constrictions inherent in diffuser vanes, volute cases are more appropriate for applications with entrained solids or high viscosity fluids. Volutes of more than rectangular or square shape can cause the impeller to be worn and the drive shaft to wear more than equally.
Centrifugal pumps are constant head machines. They generate a fixed “head” (the height a fluid can be lifted) regardless of the fluid being pumped. The design and operation of a centrifugal pump are based on the relationship between the system curve (which defines the required flow and pressure) and the pump’s performance curve (which shows how the pump performs under various conditions).
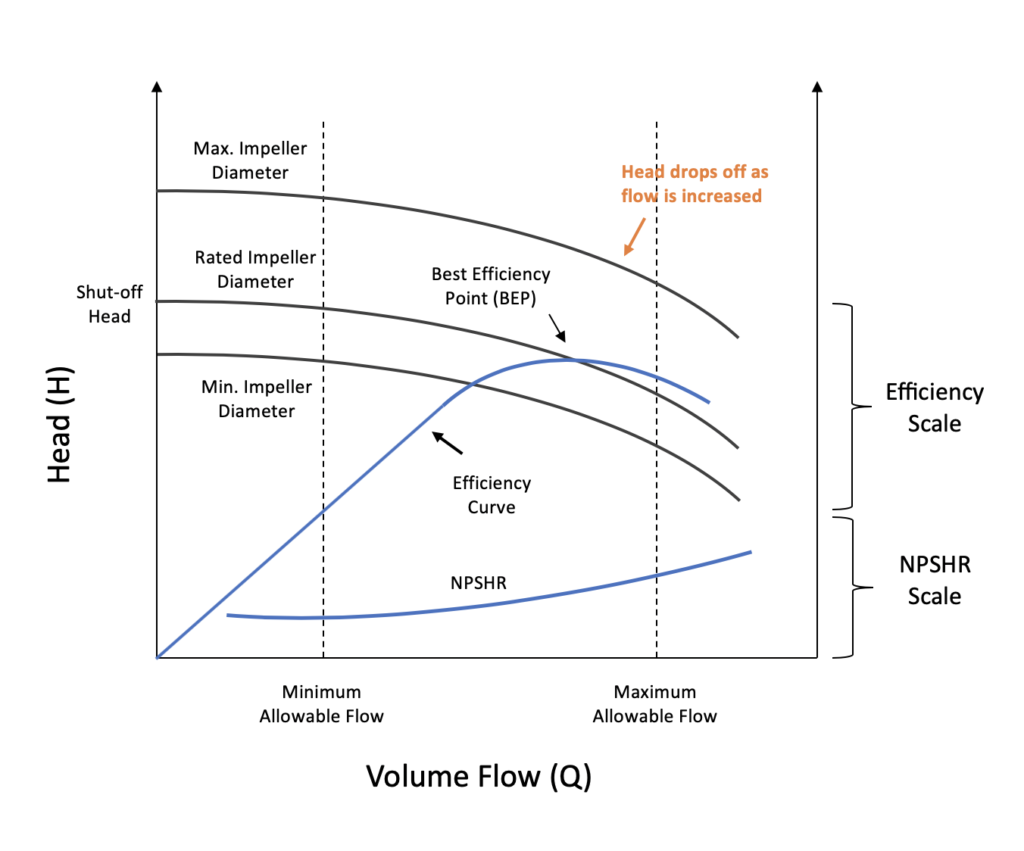
A centrifugal pump is a mechanical device that, by means of an impeller driven at high speed by a prime mover, presses on the fluid to cause it to enter the pump casing and so move a fluid under pressure. The rapidly rotating impeller welcomes fluid along the axis and casts it out by centrifugal force along the circumference of the tip of the vane. The impeller action increases the fluid velocity and pressure as well as directs the fluid towards the pump outlet. The pump casing is specially configured to limit the fluid coming into the pump inlet, drive it into the impeller, and restrict on slowing and controlling the fluid before discharge.
Types of Centrifugal Pumps
Type of Centrifugal Pump | Key Features | Use Case |
---|---|---|
Canned Motor Pump & Magnetic Drive Pump | Sealless designs: Canned motor pumps use a sealed can to contain wetted parts, while magnetic drive pumps use close-coupled magnets to drive the impeller. | Safe handling of hazardous, corrosive, or high-purity fluids in chemicals and hydrocarbons where leakage is not permitted. |
Chopper/Grinder Pump | Impeller fitted with grinding or cutting teeth to handle solids | Industrial wastewater, sewage systems, and food processing |
Circulator Pump | Inline compact design for efficient fluid circulation | HVAC systems for heating, cooling, and ventilation |
Multistage Pump | Multiple impellers in series for higher pressure generation | High-pressure applications like boiler feedwater, reverse osmosis, and industrial systems |
Cryogenic Pump | Special construction materials to withstand extremely low temperatures | Liquid natural gas (LNG), liquid oxygen, and coolant handling |
Trash & Slurry Pump | Abrasion-resistant designs; trash pumps handle water with solids, while slurry pumps withstand highly abrasive slurries | Draining pits, mines, construction sites, and handling mining or mineral-processing slurries |
Close Coupled & Frame Mounted Pump | Compact designs with impellers mounted directly on motor shaft (close coupled) or supported by independent bearing housing (frame mounted) | General-purpose industrial applications with limited space or high flow rates |
Self-Priming Pump | Automatically primes itself after initial fill; capable of handling air-contaminated fluids | Industrial applications, flood control, and agricultural irrigation |
Axial Flow Pump | Fluid moves parallel to the pump shaft, optimized for high flow and low head | Irrigation, flood control, cooling water systems |
Radial & Mixed Flow Pump | Radial flow pumps discharge fluid perpendicularly for high head; mixed flow pumps combine radial and axial features for balanced flow and head | Municipal water supply, drainage, irrigation, and industrial cooling |
Wet Pit Volute Pump | Vertical orientation; pump bowl submerged in fluid | Sump drainage, sewage, and stormwater handling |
Vertical Turbine Pump | Long shaft with submerged impellers to lift water from deep wells | Municipal water supply, irrigation, and industrial pumping |
Barrel/Can Pump | Enclosed pump for minimal leakage; suitable for handling high pressures | Refinery, petrochemical, and high-pressure industrial systems |
Horizontal & Vertical Split-Case Pumps | Horizontally split casing for easy maintenance; vertical designs save space while offering similar benefits | Municipal water systems, fire protection, and cooling water |
End Suction Pump | Single inlet with horizontal suction and vertical discharge | General-purpose industrial and municipal applications |
Inline Centrifugal Pump | Compact design with suction and discharge in line | HVAC systems and confined-space installations |
Regenerative Turbine Pump | Recirculates fluid between blades to generate high pressures for small flows | Chemical dosing systems, small industrial applications |
Rotating Casing Pump (Pitot Tube) | Uses centrifugal force from a rotating casing to enhance flow and head | Specialised industrial applications requiring precise flow control |
Reversible Centrifugal Pump | Can reverse operation to act as a turbine | Energy recovery and hydroelectric systems |
Submersible Pumps | Fully submerged pump and motor, sealed to prevent fluid ingress | Sewage treatment, drainage, and underwater applications |
Key Operational Characteristics of Centrifugal Pumps
Flow and Head Relationship
Unlike many other components, centrifugal pumps are designed for a specific combination of flow and head. Pumps run outside of their optimal design point (often known as their ‘best efficiency point’ or BEP’) decrease in efficiency and result in more component wear. This can be seen in Figure 3.
System Dependency
The system dictates the operating point of the pump, not the pump itself. If flow or pressure is not where it should be, either due to system or pump design, then it is not the pump but a problem with the system configuration or design which follows the system curve.
Efficiency Concerns
Pumps running away from their design point (e.g., higher flows or pressures than expected) will consume more power and exhibit lower efficiency. This can lead to early pump failure, cavitation, or even overheating.
Suction Conditions
Centrifugal pumps don’t “suck” fluid into the impeller. Instead, atmospheric pressure forces liquid into the pump. This is why adequate suction head or flooded suction is necessary, especially for higher elevation installations.
Pump Calculations | Finding the Right Size and Flow
An efficient and proper performing pump requires the proper selection and sizing of pump. According to the following formula, the essential parameters related to the centrifugal pump system can also be determined.
Pump Head Calculation
The total dynamic head (TDH) for a pump system is the total height (in meters or feet) that a pump needs to lift the liquid, including friction losses.
The general formula for calculating the head is:
Where:
- Pd – Discharge Pressure (Pa or Psi)
- Ps – Suction Pressure (Pa or Psi)
- λ – Specific weight of the fluid (N/m3or lb/ft3)
- g – Gravitational acceleration (9.81 m/s2)
- Zd – Height at discharge (m)
- Zs – Height at suction (m)
Pump Head Calculator
This can be simplified to:
Where:
- Static Head is the vertical distance between the suction tank and the discharge point. (m)
- Friction Loss is the loss due to friction in the pipes and fittings. (m)
- Pressure Head is the pressure required at the discharge point. (m)
Total Dynamic Head Calculator
Flow Rate Calculation
To determine the flow rate needed for your application, use the following equation:
Where:
- Area is the cross-sectional area of the pipe (m2).
- Velocity is the speed of the fluid in the pipe (m/s).
It is important to note, that in many applications there is a range of velocity that is required for Certain pumping systems and piping networks. This is to reduce the chances of cavitation and also allow the liquid to move with enough velocity to reduce chances of settling if the fluid contains any solids.
Power Calculation
To calculate the power required for the pump, use this formula:
Where:
- Flow is in cubic meters per second (m³/s).
- Head is Height (m).
- Density is the fluid density in (kg/m³).
- Gravity is the acceleration due to gravity (9.81 m/s²).
- Efficiency is the pump efficiency (decimal).
Common Challenges in Centrifugal Pump Operation
1. Cavitation
Cavitation occurs when the pressure at the impeller’s inlet falls below the vapour pressure of the fluid. These bubbles, also called voids, collapse and cause shock waves that can damage the impeller, and reduce pump efficiency. Cavitation is a common cause of wear and tear in engineering, especially in pumps and propellers.
2. Viscosity Handling
Centrifugal pumps are most effective with low-viscosity fluids. When dealing with higher viscosity fluids, pump performance decreases significantly, requiring adjustments to the design or a different pump type altogether.
3. Suction Lift Limitations
Most centrifugal pumps have limited suction lift capabilities. In cases where the fluid must be lifted from a lower level, a positive pressure or a flooded suction is required to maintain optimal operation.
Industrial systems can’t go without centrifugal pumps due to their simplicity, reliability and versatility. But choosing the pump that is right for your application requires understanding how all of that interplays: flow, head, system curves, and pump performance. By using the principles and formulas in this guide; you can optimise your pump system for efficiency and pump life.
Centrifugal pumps are fascinating devices for engineers and system designers due to their mix of design flexibility and operational stability. We hope this guide has helped you with knowledge and tools to make informed decisions when you’re considering your next centrifugal pump project.
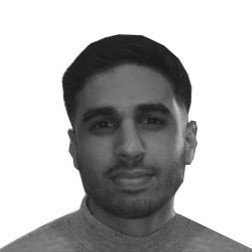
Hassan graduated with a Master’s degree in Chemical Engineering from the University of Chester (UK). He currently works as a design engineering consultant for one of the largest engineering firms in the world along with being an associate member of the Institute of Chemical Engineers (IChemE).