Key Takeaways
– Foundry machinery plays a crucial role in the manufacturing industry.
– Foundry machinery encompasses various equipment used in metal casting processes.
– The advancements in foundry machinery have led to increased efficiency and productivity.
– Safety measures should be prioritized when working with foundry machinery.
– Regular maintenance and proper training are essential for optimal performance of foundry machinery.
Introduction
Foundry machinery is a vital component of the manufacturing industry, particularly in metal casting processes. It encompasses a wide range of equipment and tools used to shape and mold metal into desired forms. From melting and pouring to solidifying and finishing, foundry machinery plays a crucial role in the production of various metal products. This article will delve into the world of foundry machinery, exploring its different types, applications, advancements, and safety considerations.
The Types of Foundry Machinery
Foundry machinery can be classified into several categories based on their specific functions and applications. These categories include:
Melting and Pouring Equipment
Melting and pouring equipment is responsible for melting metal alloys and pouring them into molds. Furnaces, crucibles, ladles, and pouring systems are some examples of machinery used in this process. These machines ensure the metal is in a molten state and can be easily poured into molds for casting.
Molding and Coremaking Equipment
Molding and coremaking equipment is used to create molds and cores that give shape to the final metal product. This equipment includes molding machines, core shooters, and sand mixers. Molding machines help in creating molds by compacting sand or other materials around a pattern, while core shooters produce cores that are inserted into the molds to create hollow spaces or intricate designs.
Shakeout and Cleaning Equipment
Shakeout and cleaning equipment is employed to remove the castings from the molds and clean them. Shakeout machines use vibrations or mechanical actions to separate the castings from the molds, while cleaning equipment such as shot blasting machines or tumblers remove any residual sand or debris from the castings.
Finishing and Inspection Equipment
Finishing and inspection equipment is used to refine the surface of the castings and ensure their quality. Grinding machines, polishing machines, and inspection tools are examples of machinery used in this stage. These machines help in removing any imperfections, such as excess material or rough edges, and ensure that the final product meets the required specifications.
The Advancements in Foundry Machinery
Over the years, foundry machinery has undergone significant advancements, leading to improved efficiency and productivity in the metal casting industry. Some notable advancements include:
Automation and Robotics
Automation and robotics have revolutionized the foundry industry by streamlining processes and reducing manual labor. Automated systems can handle tasks such as pouring, molding, and cleaning with precision and speed, resulting in higher production rates and reduced human error.
Computer-Aided Design and Simulation
Computer-aided design (CAD) and simulation software have enabled foundry engineers to design and optimize molds and cores digitally. This technology allows for the creation of complex geometries and the identification of potential defects or issues before the actual casting process. It saves time and resources by minimizing trial and error in the production phase.
Energy Efficiency
Foundry machinery has become more energy-efficient, reducing the environmental impact of metal casting processes. Improved insulation, heat recovery systems, and energy management techniques have contributed to significant energy savings in foundries. This not only benefits the environment but also reduces operational costs for foundry operators.
Data Analytics and Predictive Maintenance
The integration of data analytics and predictive maintenance techniques has enhanced the reliability and uptime of foundry machinery. By monitoring equipment performance and analyzing data, potential issues or failures can be detected in advance, allowing for timely maintenance and minimizing downtime. This proactive approach improves overall equipment efficiency and reduces the risk of unexpected breakdowns.
Safety Considerations in Working with Foundry Machinery
Working with foundry machinery requires strict adherence to safety protocols to prevent accidents and injuries. Some key safety considerations include:
Personal Protective Equipment (PPE)
Wearing appropriate PPE, such as heat-resistant clothing, gloves, safety glasses, and helmets, is essential when working with foundry machinery. PPE protects workers from heat, molten metal splashes, and other potential hazards.
Training and Education
Proper training and education on the operation and maintenance of foundry machinery are crucial for the safety of workers. Training programs should cover equipment handling, emergency procedures, and hazard identification to ensure that workers are equipped with the necessary knowledge and skills.
Machinery Maintenance
Regular maintenance of foundry machinery is vital to ensure its optimal performance and prevent malfunctions. Routine inspections, lubrication, and repairs should be carried out to identify and address any potential issues before they escalate.
Ventilation and Dust Control
Foundry processes generate fumes, dust, and other airborne particles that can be harmful if inhaled. Proper ventilation systems and dust control measures should be in place to minimize exposure and maintain a safe working environment.
Conclusion
Foundry machinery is an integral part of the manufacturing industry, enabling the production of various metal products through metal casting processes. The different types of foundry machinery, including melting and pouring equipment, molding and coremaking equipment, shakeout and cleaning equipment, and finishing and inspection equipment, each play a crucial role in the overall casting process. Advancements in foundry machinery, such as automation, computer-aided design, energy efficiency, and predictive maintenance, have significantly improved productivity and efficiency in the industry. However, safety considerations should always be prioritized when working with foundry machinery to ensure the well-being of workers and prevent accidents. Regular maintenance, proper training, and the use of personal protective equipment are essential for a safe and productive foundry environment.
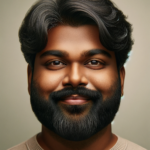
Adrian graduated with a Masters Degree (1st Class Honours) in Chemical Engineering from Chester University along with Harris. His master’s research aimed to develop a standardadised clean water oxygenation transfer procedure to test bubble diffusers that are currently used in the wastewater industry commercial market. He has also undergone placments in both US and China primarely focused within the R&D department and is an associate member of the Institute of Chemical Engineers (IChemE).