Follow Emilie Bodoin on Linkedin or learn more about Pure Lithium on their website here. You can view our earlier interview with Emilie Bodoin here. Read more about Pure Lithium here:
- Lithium metal to make traditional batteries obsolete, Pure Lithium CEO says | Hotter Commodities
- Pure Lithium Bets on Vanadium Cathodes to Save U.S. Battery Independence
Emilie Bodoin, the founder and CEO of Pure Lithium, is leading a revolutionary change in battery technology. Her company’s innovative use of vanadium-based cathodes is poised to redefine energy storage, offering greater efficiency, sustainability, and safety compared to traditional lithium-ion batteries. This has now been backed by the US Department of Energy which has awarded Pure Lithium funding.
As part of our in-depth exploration of the development of this funding from the US DOE, we had the privilege to speak with Emilie Bodoin. She shared invaluable insights into the challenges, innovations, and environmental benefits driving Pure Lithium’s vision for a sustainable future following the funding.
The following interview is presented unedited to preserve Emilie Bodoin’s original responses and provide an authentic glimpse into the cutting-edge advancements shaping the future of battery technology.
Congratulations on securing funding from the U.S. Department of Energy’s Vehicle Technology Office. Could you provide an overview of how this funding will help Pure Lithium achieve its goals; specifically in scaling production of lithium metal anodes from recycled lithium?
This collaboration with the Department of Energy and Argonne allows us to put our extraction and anode production technologies to work in a practical use case. While our focus remains on extracting lithium metal from lithium brines to produce the anode and then the complete battery, much of the recycling process is very similar, so this scaling up of production capability helps with our long-term goals and creates a closed loop system.
Pure Lithium’s partnership with Argonne National Laboratory is a key element of this announcement. What makes Argonne such a valuable partner for this project, and how did this collaboration come about?
Argonne has deep expertise in battery technology and materials science. With over 50 years of leadership in advanced battery research, Argonne has been at the forefront of developing lithium-based technologies and has worked on lithium metal production and technology for nearly a decade, making it the ideal collaborator for innovations in lithium metal production. Argonne’s Materials Engineering Research Facility (MERF) helps industry scale materials.
I have personally worked with Argonne as a Principal Investigator from 2015 to 2018, and I’ve seen firsthand the laboratory’s ability to drive groundbreaking research and translate it into scalable solutions. This partnership leverages Argonne’s state-of-the-art facilities and world-class scientists. More broadly, this collaboration is a great example of how the U.S. national lab system fosters cutting-edge innovation and strengthens domestic supply chains. By working together, we are not only accelerating the commercialization of lithium metal anodes but also contributing to the long-term success of the U.S. battery industry.
Your press release mentions creating a closed-loop, fully domestic supply source. Why is it so critical to establish a supply chain for lithium metal that is both environmentally sustainable and based entirely in the U.S.?
Right now, the U.S. is entirely dependent on imports from China for the critical minerals used to make batteries for electric vehicles and other devices. As we have seen, this world-spanning supply chains can prove extremely risky for U.S. manufacturers – and by extension U.S. economic security – in a time of growing global trade conflict. The U.S. simply does not have a complete domestic battery supply chain, and we are so far behind China in processing minerals for the dominant lithium-ion battery that it is impossible to catch up. The answer is to leapfrog with technology, completely reinventing the battery, from the materials used to the production process. That is what Pure Lithium has done. Our battery uses materials that are easy to source in the U.S. and contains no graphite, nickel, cobalt or manages, all imported minerals that depend on a supply chain dominated by China.
There is significant industrial waste produced in the United States that contains lithium. Could you talk about the process of recovering lithium from these waste streams and transforming it into a usable form for your batteries?
Sorry, we aren’t able to discuss these details at this time.
Your team is skilled in metallurgical processing. How does that expertise align with this new initiative to recycle lithium metal, and what unique challenges do you anticipate in scaling up these processes?
Pure Lithium operates at the intersection of metallurgy and batteries, and our team here reflects that. My Co-founder, Donald Sadoway, is the Emeritus Professor of Materials Chemistry in the Department of Materials Science and Engineering at Massachusetts Institute of Technology, and Pure Lithium’s full time CSO. He has been a leader in the metallurgy and battery spaces for over 45 years, and he has helped refine our Brine to Battery™ technology. Our PI at Argonne is a metallurgist and incidentally was a post-doc of Professor Sadoway. We have many of Professor Sadoway’s former students on our team.
You highlighted that external partnerships are key to accelerating your time to market. Beyond Argonne National Laboratory, what other collaborations or external support does Pure Lithium see as pivotal in bringing this technology to commercial viability?
We have already formed several partnerships to accelerate our drive towards commercial production including joint development agreements with E3 Lithium and Saint-Gobain Ceramics. We are actively pursuing meaningful partnerships with companies that can help us accelerate.
Pure Lithium’s technology aims to replace currently used lithium-ion battery components with a lithium metal anode and a vanadium oxide cathode. Could you explain how this approach could lead to a “step-change” improvement in performance, cost, and safety?
Lithium metal is the “holy grail” of energy storage. There have been two batteries in our life time commercialized to gigawatt scale, lead acid and lithium-ion. Lithium metal will be the next, and displace lithium-ion just like lithium-ion displaced nickel metal hybrid batteries, or transistors displaced vacuum tubes in the semi-conductor industry. Compared to lithium-ion batteries, our lithium metal battery offers twice the capacity, half the weight, and approximately 30% lower material costs. Our Brine to Battery™ technology enables the commercially viable production of lithium metal anodes by vertically integrating raw material extraction with battery component manufacturing. By eliminating complex lithium compound production and the multiple extraction, refining, and purification steps required in traditional methods, we streamline the process into a single, seamless step. The performance improvements stem from lithium metal’s superior properties—specifically, its tenfold increase in specific capacity compared to the graphite used in today’s lithium-ion anodes. Our cathode does not contain any lithium, further simplifying the supply chain and reducing costs.
Lithium-ion batteries are notorious for their tendency to catch fire through an event known as “thermal runaway.” Thermal runaway starts in the cathode, with today’s nickel-based technologies beginning to release oxygen at temperatures below 100°C. We mitigate this risk by utilizing a thermally stable vanadium cathode that does not release oxygen at its highest state of charge. Vanadium itself is stable at temperatures up to 1800°C, while the carbon binders in the cathode maintain stability up to 700°C. This significantly enhances battery safety and reliability under extreme conditions.
Battery supply chains have been under immense scrutiny in recent years. How does this project with the DOE and Argonne position Pure Lithium to address concerns about critical mineral sourcing, cost, and long-term sustainability?
This project offers us another pathway for large-scale lithium metal production while providing industrial partners with a valuable solution for repurposing their waste. It showcases the adaptability of our core technology by demonstrating our ability to produce ultra-pure lithium metal anodes from a variety of feedstocks. Our work with Argonne will prove that we can maintain the highest standards of quality and purity regardless of the feedstock used, all while keeping production costs low. By enhancing the circularity of supply chains in North America, we are helping pave the way for a more sustainable and self-sufficient domestic battery industry in the U.S, that separates our manufacturing capabilities from the volatility of global supply chains.
From lab to real-world application; what is the roadmap for integrating your recycled lithium metal anodes into commercial products? Do you foresee this technology being adopted first in electric vehicles, or might it find broader usage in other industries?
Actually, this is the easy part. Our battery will work for any product or application that currently relies on lithium-ion batteries, including electric vehicles. That means manufacturers won’t have to adapt their products to make them work with our batteries. Our initial targets are drones and consumer electronics, due to the immediate need for higher energy density, our prowess in producing small cells, and our goal of getting to market and generating returns as quickly as possible. We are not starting with EVs because the timelines for establishing those production lines with automotive OEMs are just much longer. However, those timelines may be accelerated if those OEMs seek to adapt existing battery production facilities to work with our technology.
Looking ahead, how do you see Pure Lithium’s Brine to Battery and recycling innovations shaping the future of battery technology, both domestically in the U.S. and on a global scale?
Our goal is to revolutionize battery manufacturing by creating a vertically integrated, localized process that leverages readily available materials in regions around the world. We firmly believe that lithium metal batteries are the future of energy storage—both in terms of performance and production efficiency. Our Brine to Battery™ technology enables the extraction of lithium metal, the production of a battery-ready lithium metal anode, and the assembly of the completed battery all in a single location. This approach is unlike anything currently available in the industry. Our long-term vision is to establish battery hubs worldwide, strategically located near sources of lithium brine and vanadium.
Everything that helps us move towards our goal of full commercial production is a massive positive for Pure Lithium. For people tracking next-generation battery technology, I urge you to do your homework and remember the history of batteries. The lithium metal battery was invented by Nobel Laureate Professor M. Stanley Whittingham at Exxon in 1977. It had no lithium in the cathode. This is not a new concept, not a black box, not some secret sauce. We do not need two Nobel prizes to commercialize this technology, we have kept our heads down and solved the hard problems by taking a sensible systematic approach. But we had to reinvent a lot of things, because commercially available cathodes are not going to enable lithium metal. We feel like we’re really getting our message across these days and working Argonne is just fantastic.
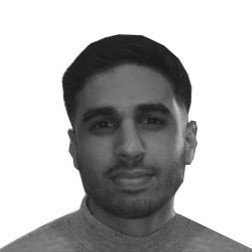
Hassan graduated with a Master’s degree in Chemical Engineering from the University of Chester (UK). He currently works as a design engineering consultant for one of the largest engineering firms in the world along with being an associate member of the Institute of Chemical Engineers (IChemE).