Stainless steels are used across a variety of industries from transportation, oil and gas, nuclear power and chemical processing. Their ability and resistance to corrosion is key to their versatility and abundant usage. However, exposure to temperatures in the range encountered during welding can trigger sensitisation; a process that depletes chromium in microscopic regions and undermines the protective passive layer. This can lead to pitting, cracking and downtime for industrial components. Researchers at the University of Wisconsin-Madison have now found a new approach for restoring stainless steel corrosion resistance and was featured in Metallurgical and Materials Transactions. The paper can be found here:
Sasidhar, K. N., Ulfig, R., & Sridharan, K. (2025). Nanoscale Compositional Homogenization by Severe Plastic Deformation-Induced Twinning for Achieving Desensitization in Stainless Steel. Metallurgical and Materials Transactions A, 56(5), 1572–1584. https://doi.org/10.1007/s11661-025-07730-7
Kumar Sridharan, Vilas Distinguished Achievement Professor, Departments of Nuclear Engineering & Engineering Physics and Materials Science & Engineering at the University of Wisconsin–Madison was the team lead on the research. He stated:
This is a major problem for stainless steels, when stainless steel gets corroded, components need to be replaced or remediated. This is an expensive process and causes extended downtime in industry.”
Alongside Sridharan, assistant scientist Kasturi Narasimha Sasidhar, a scientist part of Sridharan’s group as well as Robert Ulfig have demonstrated that ultrasonic nanocrystal surface modification (UNSM) can restore corrosion resistance in sensitised 304-grade stainless steel without any heat treatment. In UNSM, a hardened pin oscillates against the metal surface at ultrasonic frequencies, inducing severe plastic deformation and forming a nanocrystalline surface layer. Sridharan said:
“We showed that ultrasonic nanocrystal surface modification can restore the corrosion-resistant state of the stainless steel, without needing any heat treatment, which is a really big deal,”
To uncover the mechanism behind this effect, the researchers partnered with CAMECA Instruments (AMETEK) to apply atom probe tomography. This technique maps the three-dimensional distribution of elements at near-atomic resolution, revealing how chromium; which normally accounts for about 18 % of stainless steel, redistributes after UNSM. Sasidhar, now a senior applications scientist at CAMECA Instruments Inc said:
“CAMECA’s atom probe tomography technology allowed the researchers to look at the steel at the nanometer scale, in three dimensions, and to precisely measure the location of the elements in the material,”
Their analysis showed that UNSM equalises chromium levels in the previously depleted zones, re-establishing a continuous protective film. As a result, treated samples regained their original corrosion resistance; comparable to that of as-manufactured material, without exposing the steel to high heat.
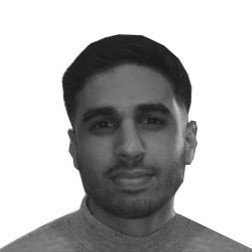
Hassan graduated with a Master’s degree in Chemical Engineering from the University of Chester (UK). He currently works as a design engineering consultant for one of the largest engineering firms in the world along with being an associate member of the Institute of Chemical Engineers (IChemE).