Key Takeaways
– Rotary dryers are versatile machines used in various industries for drying materials.
– They offer advantages such as high efficiency, low maintenance, and flexibility in operation.
– Different types of rotary dryers are available, including direct rotary dryers, indirect rotary dryers, and rotary cascade dryers.
– The selection of a rotary dryer depends on factors such as the type of material, moisture content, desired end product, and available space.
– Proper maintenance and regular inspections are essential for ensuring the optimal performance and longevity of rotary dryers.
Introduction
Rotary dryers are an essential component in many industries, providing a reliable and efficient solution for drying various materials. From agricultural products to industrial waste, rotary dryers play a crucial role in reducing moisture content and preparing materials for further processing. This article will explore the world of rotary dryers, discussing their types, applications, benefits, and maintenance requirements.
Types of Rotary Dryers
Rotary dryers come in different configurations to suit specific drying needs. The three main types of rotary dryers are direct rotary dryers, indirect rotary dryers, and rotary cascade dryers.
Direct Rotary Dryers
Direct rotary dryers are the most common type and are suitable for a wide range of materials. In this design, hot gases directly contact the material being dried, transferring heat and evaporating moisture. The material moves through the dryer in a rotating drum, ensuring efficient and uniform drying. Direct rotary dryers are often used for bulk solids, such as minerals, fertilizers, and grains.
Indirect Rotary Dryers
Indirect rotary dryers are ideal for materials that require gentle drying or are sensitive to direct contact with hot gases. In this design, a heat transfer medium, such as steam or thermal oil, is circulated through the dryer’s outer shell. The material being dried is indirectly heated, ensuring controlled and uniform drying. Indirect rotary dryers are commonly used for fine powders, pharmaceuticals, and food products.
Rotary Cascade Dryers
Rotary cascade dryers are specifically designed for materials that require extended drying times or have a tendency to stick or clump together. In this design, the material is lifted and cascaded through a series of rotating flights or paddles, ensuring thorough drying and preventing agglomeration. Rotary cascade dryers are often used for sticky or heat-sensitive materials, such as biomass, sludge, and certain chemicals.
Applications of Rotary Dryers
Rotary dryers find applications in a wide range of industries, including agriculture, mining, pharmaceuticals, chemicals, and more. Some common applications include:
Drying Agricultural Products
Rotary dryers are used in the agricultural industry to dry crops, such as grains, corn, and rice, before storage or further processing. By reducing moisture content, rotary dryers help prevent spoilage and maintain the quality of agricultural products.
Drying Minerals and Ores
In the mining industry, rotary dryers are used to dry minerals and ores, such as coal, iron ore, and copper concentrate. By removing moisture, rotary dryers facilitate the handling and transportation of these materials, improving efficiency and reducing costs.
Drying Biomass and Waste Materials
Rotary dryers play a crucial role in the biomass and waste management industries. They are used to dry biomass, such as wood chips, sawdust, and agricultural residues, for use as fuel or feedstock. Additionally, rotary dryers are employed in the drying of waste materials, such as sewage sludge and industrial by-products, before disposal or further treatment.
Maintenance and Care
Proper maintenance and regular inspections are essential for ensuring the optimal performance and longevity of rotary dryers. Some key maintenance practices include:
Cleaning and Lubrication
Regular cleaning of the dryer’s interior and exterior surfaces helps prevent the buildup of debris and contaminants. Lubrication of bearings, gears, and other moving parts ensures smooth operation and reduces wear and tear.
Inspections and Repairs
Periodic inspections of the dryer’s components, such as seals, belts, and motors, help identify any signs of wear or damage. Prompt repairs and replacements of faulty parts prevent further damage and ensure uninterrupted operation.
Airflow and Heat Control
Monitoring and adjusting airflow and heat settings are crucial for maintaining optimal drying conditions. Proper airflow ensures efficient moisture removal, while accurate heat control prevents overheating and material degradation.
Conclusion
Rotary dryers are versatile machines that find applications in various industries for drying materials. Their efficiency, low maintenance requirements, and flexibility make them a popular choice for drying a wide range of products. By understanding the different types of rotary dryers, their applications, and the importance of maintenance, industries can make informed decisions and maximize the benefits of these essential drying machines.
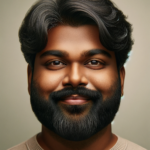
Adrian graduated with a Masters Degree (1st Class Honours) in Chemical Engineering from Chester University along with Harris. His master’s research aimed to develop a standardadised clean water oxygenation transfer procedure to test bubble diffusers that are currently used in the wastewater industry commercial market. He has also undergone placments in both US and China primarely focused within the R&D department and is an associate member of the Institute of Chemical Engineers (IChemE).