Membranes play a crucial role in various industrial and environmental applications, including water purification, wastewater treatment, food processing, and pharmaceutical production. However, conventional membrane manufacturing relies heavily on fossil fuel-derived materials and toxic solvents, leading to environmental and regulatory concerns. Researchers at the University of Bath have now developed a plant-based nanofiltration membrane that eliminates these issues while maintaining high performance. Find the study here:
Sadare, O., Zoumpouli, G. A., Chew, Y. M. J., Wenk, J., Castro-Dominguez, B., & Mattia, D. (2025). Lignin- and Cellulose-Derived Sustainable Nanofiltration Polyelectrolyte Membranes. ACS Sustainable Chemistry & Engineering. https://doi.org/10.1021/acssuschemeng.4c08611
The newly developed membrane is made entirely from cellulose and lignin. Two renewable, plant-derived materials. Unlike commercial membranes, which rely on synthetic polymers and hazardous solvents, this polyelectrolyte membrane (PEM) is fabricated using a more sustainable approach.
Tests have shown that the membrane effectively filters water-soluble dyes of various molecular sizes, simulating different pollutants.
Dr. Olawumi Sadare, a Royal Society Newton Fellow at the University of Bath’s Department of Chemical Engineering, explains the significance of this development:
“The potential of this technology to reduce environmental impacts is particularly crucial, especially in light of upcoming EU legislation to curb the use of toxic solvents, and the proposed bans on fluorinated polymers in membrane manufacturing. Another desirable aspect of the membrane we have created is that you can control its thickness as you wish to tune the permeance characteristics, or how selective it is.”
The membrane has the ability to control its thickness, allowing researchers to fine-tune its permeability and selectivity. This adaptability makes it a viable replacement for existing membranes across various industries.
The research team also demonstrated the membrane’s durability, with tests showing stable performance over 30 days in water. This stability is essential for real-world applications, ensuring longevity without the need for frequent replacement.
Professor Davide Mattia, from Bath’s Centre for Integrated Materials, Processes and Structures, said:
“Chemical separations consume 10%–15% of the world’s energy, and membranes are considered the most promising technology to dramatically reduce the carbon footprint of these vital processes. As such, the focus has always been on improving membrane performance, with little attention paid to the impact of their manufacturing. All commercial membranes manufactured today use toxic organic solvents and fossil-fuel derived materials, particularly polymers.
He went onto say:
These not only emit carbon to manufacture them but also cannot be recycled and end up in a landfill. The approach we developed focuses on making membrane manufacturing sustainable, while producing a membrane that has comparable performance to commercial ones.”
The researchers have applied for patent protection for the technology and are taking steps toward commercialising the membrane. Future research will focus on further testing the membrane’s performance in water treatment, and in the removal of PFAS forever chemicals.
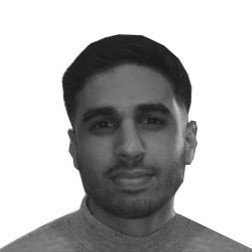
Hassan graduated with a Master’s degree in Chemical Engineering from the University of Chester (UK). He currently works as a design engineering consultant for one of the largest engineering firms in the world along with being an associate member of the Institute of Chemical Engineers (IChemE).