Research teams at the University of Illinois Urbana-Champaign, working in collaboration with industry partners, have detailed a method that aims to reduce waste, save costs, and minimize reliance on primary platinum mining by recycling platinum catalysts used in silicone material production.
Platinum catalysts are one of a few homogenous catalysts that drive reactions for making silicone materials through a process called hydrosilylation. Although these catalysts are efficient, recovering them can be challenging because of the high viscosity and boiling point of the finished products, the catalysts’ tendency to lose their effectiveness by deactivating and the low concentration of platinum in the final product.
“Most electrochemistry works for things that are very polar, things that are conductive—for example, aqueous solutions such as water,”
said chemical and biomolecular engineering professor Xiao Su. He went onto say:
“It was very challenging to move towards a real industrial process in which everything is apolar, like oils.”
The research published by lead author Jemin Jeon and the Xia Su team can be found here:
Jeon, J., Chung, C.-H., Roh, S., Bergman, E., Wang, M., & Su, X. (2025). Olefin-Assisted Electrochemical Recycling of Homogeneous Hydrosilylation Catalysts in Nonpolar Media. JACS Au. https://doi.org/10.1021/jacsau.4c01071
According to the lead researchers, the first objective was to maintain the catalyst’s activity after each use. The team accomplished this by introducing a specialised “olefin ligand” molecule that connects to the platinum atom, preserving the catalyst’s structure. By preventing unwanted aggregation of platinum particles, this ligand helps keep the catalyst active, which is a critical factor in achieving a successful recycling cycle.
Another key aspect of this method, involves coating electrode surfaces with a redox-active polymer. This coating is triggered by electrochemistry, allowing the platinum catalyst; now stabilized by the attached ligand, to be captured and later released into a separate solution. Because the polymer binds only to the catalyst, the system works like a targeted filter. After the catalyst is “caught,” it is transferred to a fresh reaction medium, ready for reuse.
“It’s a little bit like a filter, It binds the platinum catalyst, which is now stable, and then we bring it to another solution and release it so it can be used again. So we have this catch and release system that basically ‘catches’ the platinum from the product solution and then ‘releases’ it into a fresh reaction media. And this allows you to keep using the catalyst.”
Said Su.
Dow researchers Miao Wang and Evan Bergman, have partnered with the team to test the process under real-world manufacturing conditions. These industrial trials helped refine the method, ensuring it can function in complex environments where nonpolar, oil-like substances are common. In some conventional recycling systems, electrochemical techniques work best in water-based solutions. The new approach, however, addresses non-conductive fluids more typical of silicone manufacturing.
“We’ve demonstrated before that you can recycle catalysts from conductive solutions like water, but this is the first time that we’re actually doing it with real industrial processes which have a lot of nonpolar solvents,” Su said. “We worked with Dow’s R&D teams—the industrial researchers that are actually working on the process for making the silicones—so we had a lot of real feedback on practical issues that industry faces.”
From an economic perspective, recovering platinum in this way may reduce the need to purchase new supplies of the metal. The mining and refining of platinum can be expensive and resource-intensive. By extending the catalyst’s usable life, manufacturers could lower production costs and reduce environmental impacts tied to mining.
The University of Illinois team views the project as an example of building a more circular model for chemical processes. They envision that capturing, releasing, and reusing catalysts could be extended to other valuable metals in various industries. Researchers also state that improved catalyst circularity might lead to stronger supply chains, as well as reduced waste in large-scale production.
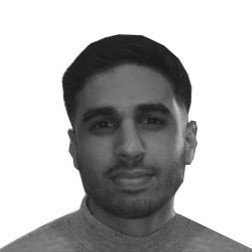
Hassan graduated with a Master’s degree in Chemical Engineering from the University of Chester (UK). He currently works as a design engineering consultant for one of the largest engineering firms in the world along with being an associate member of the Institute of Chemical Engineers (IChemE).