Scientists at the University of Minnesota Twin Cities labs have shown a discovery to minimise chemical production pollution as well as maximise production efficiency. The new chemical process called selective combustion removes only targeted pollutants through its mechanism without needing the energy-intensive requirements of traditional systems.
The study demonstrates the use of a bismuth oxide catalyst that can selectively combust acetylene in ethylene-rich gas streams. This is a main step in the production of polyethylene, one of the world’s most widely used plastics. The research paper can be found here:
Jacob, M., Nguyen, H., Raj, R., Garcia-Barriocanal, J., Hong, J., Perez-Aguilar, J. E., Hoffman, A. S., Mkhoyan, K. A., Bare, S. R., Neurock, M., & Bhan, A. (2025). Selective chemical looping combustion of acetylene in ethylene-rich streams. Science, 387(6735), 744–749. https://doi.org/10.1126/science.ads3181
The challenge in hydrocarbon processing has long been the difficulty of removing trace contaminants without affecting the primary product. In the case of polyethylene production, acetylene contamination; even in small amounts, can poison polymerisation catalysts, stopping the process. To combat this, the solution is to Burn everything at high temperatures, which consumes large amounts of energy and increases carbon emissions.
The team, led by Distinguished McKnight University Professor Aditya Bhan, developed a bismuth oxide catalyst that doesn’t require an external oxygen source for combustion. Instead, it uses a process known as chemical looping, where the catalyst supplies its own oxygen, allowing for controlled and selective oxidation. Bhan explained:
“No one else has shown that you could combust one hydrocarbon present in low concentrations, in mixtures with others,”
The key to this process is the bismuth oxide catalyst’s ability to repeatedly donate and restore its oxygen content without degrading its reactivity.
“We were able to take oxygen out of the catalyst and put it back in multiple times, where the catalyst changes slightly, but its reactivity is not impacted. Operating in this chemical looping mode avoids flammability concerns,”
said Matthew Jacob, a University of Minnesota chemical engineering Ph.D. candidate and one of the main authors.
Selective combustion could be applied to various chemical processes where removing trace impurities is critical.
Chemical looping isn’t a new concept, but its application in selective hydrocarbon combustion marks a novel use.
“You want to do this process selectively. Removing acetylene and other trace hydrocarbon contaminants in this manner could be more energy efficient,”
stated Matthew Neurock, a professor in Department of Chemical Engineering and Materials Science and senior co-author on the paper. He went onto say:
“You just want to be able to go into a gas mixture to remove some molecules without touching the rest of the molecules.”
The team’s research also highlights the importance of molecular-level understanding in catalyst design. By studying how molecules behave on catalyst surfaces, researchers can fine-tune materials for more efficient, selective reactions.
“If we can understand how a catalyst works, at a molecular atomic level, we can adapt it to any particular reaction,”
said Simon Bare, a Distinguished Scientist at the SLAC National Accelerator Laboratory at Stanford University, and co-author of the study.
“This can help us understand how catalysts, that produce fuels and chemicals needed in modern living, react to their environment.”
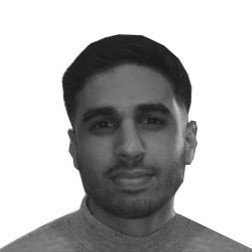
Hassan graduated with a Master’s degree in Chemical Engineering from the University of Chester (UK). He currently works as a design engineering consultant for one of the largest engineering firms in the world along with being an associate member of the Institute of Chemical Engineers (IChemE).