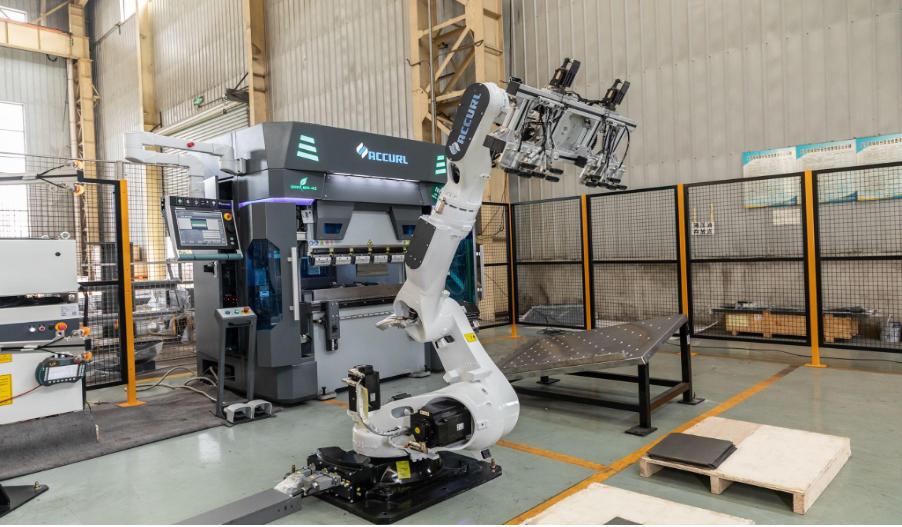
In the ever-evolving landscape of manufacturing, where efficiency and precision reign supreme, robotic press brakes stand out as a pivotal innovation. These sophisticated machines integrate automation to transform traditional metal forming processes, offering unparalleled accuracy and productivity. This article explores the transformative impact of robotic press brakes and why they are becoming a preferred choice in various manufacturing sectors.
What Are Robotic Press Brakes?
Robotic press brakes represent a significant leap in the technology used for bending sheet metal and other ductile materials. Essentially, a robotic press brake is a machine that combines traditional press brake mechanics with robotic arms and advanced software control systems to enhance functionality.
- Control Unit: The brain of the operation, coordinating all movements and functions.
- Robotic Arms: Execute precise bending operations, replacing manual adjustments.
- Backgauge System: Positions the metal sheet accurately for bending.
- Tooling: Customizable tools that perform the actual bending.
- Software Interface: Allows operators to program and control the press brake’s operations seamlessly.
Robotic press brakes from Accurl exemplify the crucial role of technical proficiency and extensive experience in the press bending process. Known for offering innovative solutions, Accurl has established a strong reputation for consistently delivering premium machines and has set a benchmark in the industry
Why Choose Robotic Press Brakes Over Traditional Models?
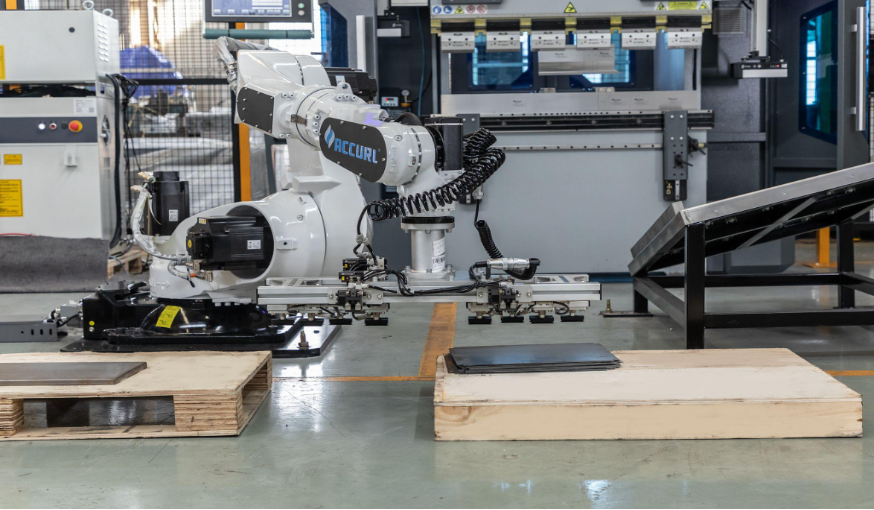
Enhanced Precision and Accuracy
Robotic press brakes utilize advanced sensors and control technologies to achieve a level of precision unattainable with manual operations. This high degree of accuracy is crucial in industries where even a millimeter’s difference can determine the usability of a product.
Increased Production Speed
Automation enables these machines to operate continuously at speeds that human operators cannot match. The integration of robotic arms accelerates the production process, allowing for more cycles per hour and significantly boosting output.
Improved Safety
With robotic press brakes, the direct human interaction with the machine’s moving parts is minimized, substantially reducing the risk of workplace injuries. Safety sensors and emergency stop features further enhance the operational safety environment.
Reduced Labor Costs
By automating repetitive tasks, these machines reduce the need for skilled labor, which can be a significant expense in traditional press brake operations. Automation also mitigates the impact of labor shortages, a common challenge in the manufacturing sector.
How Do Robotic Press Brakes Work?
The operation of robotic press brakes is a symphony of precise movements and coordinated actions. Here’s a step-by-step breakdown:
- Programming: Operators input specifications and bending sequences into the control unit.
- Sheet Loading: Robotic arms or other automated systems place the metal sheet.
- Alignment: The back gauge positions the sheet precisely.
- Bending: Tooling performs the actual bend as programmed.
- Unloading: Finished pieces are removed, and the cycle repeats.
Key Features of Robotic Press Brakes
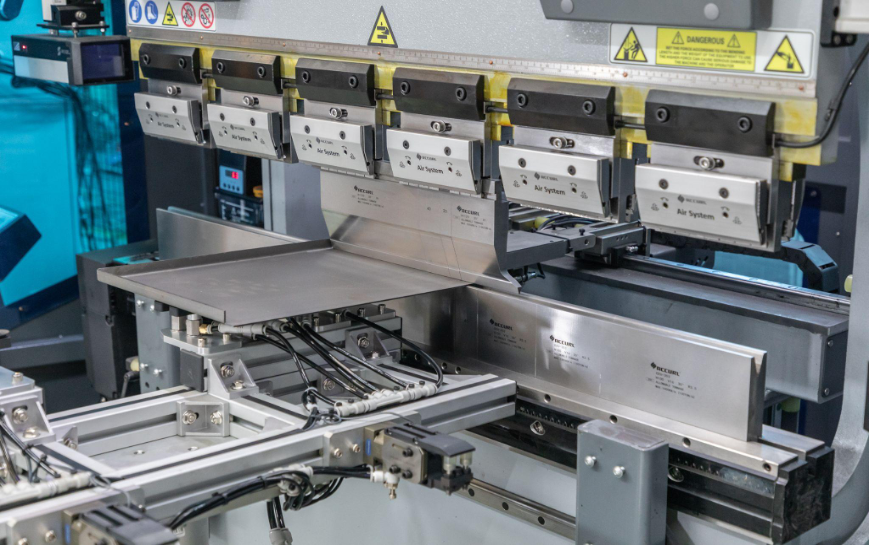
Automation Capabilities
Robotic press brakes are equipped with automation technologies that optimize various aspects of the bending process, from sheet handling to the bending itself, all controlled through sophisticated software platforms.
Software Integration
Software plays a crucial role in the operation of robotic press brakes. It allows for the integration of design and manufacturing data, ensuring that the bending process aligns perfectly with the planned specifications.
Versatility in Manufacturing
These machines can handle a wide range of materials and thicknesses, making them suitable for industries requiring versatile manufacturing capabilities, such as automotive and aerospace.
Advantages of Using Robotic Press Brakes
- Increased Productivity: Continuous operation without fatigue increases throughput.
- Scalability: Easily adjust production processes to handle varying volumes.
- Cost-Effectiveness: Reduced labor costs and enhanced production speed lower the overall cost per unit.
Challenges and Considerations When Implementing Robotic Press Brakes
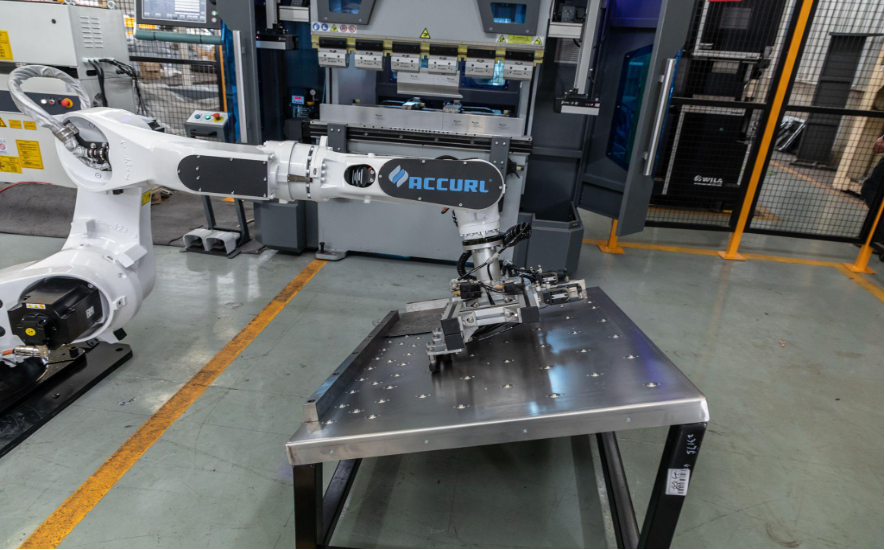
Initial Investment Cost
The upfront cost of acquiring and setting up a robotic press brake can be significant, making it essential for businesses to analyze their return on investment carefully.
Technical Training Requirements
Operators must be trained not only in basic machine operations but also in software management and troubleshooting, which requires time and resources.
Maintenance and Upkeep
Robotic press brakes require regular maintenance to keep them running efficiently, including software updates and mechanical checks.
Who Should Consider Using Robotic Press Brakes?
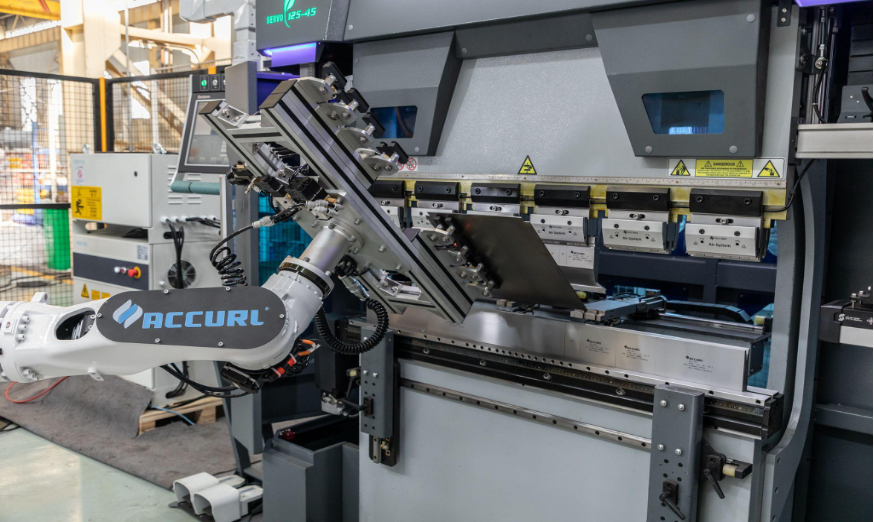
Industries that benefit most from robotic press brakes include:
- Automotive: For the precision bending of car frames and components.
- Aerospace: Where high-strength, lightweight materials are common.
- Heavy Machinery: For constructing robust equipment parts.
Step-by-Step Guide to Choosing the Right Robotic Press Brake
When selecting a robotic press brake, consider the following:
- Material Type: Determine the types of materials you will be working with.
- Production Volume: Assess your typical production needs.
- Available Space: Ensure you have adequate space for the equipment.
Case Studies: Success Stories Using Robotic Press Brakes
Automotive Industry
Robotic press brakes have revolutionized production lines, enabling faster turnaround times and higher-quality components.
Aerospace Sector
In aerospace, the precision and ability to handle exotic materials have significantly improved the manufacturing of critical aircraft components.
Heavy Machinery
The robust construction of heavy machinery components has been enhanced, improving durability and performance.
Future Trends in Robotic Press Brake Technology
Innovation continues to drive the development of robotic press brakes, with trends pointing towards even greater integration of AI and machine learning to further optimize bending processes and predictive maintenance.
Conclusion
Robotic press brakes represent a transformative technology in modern manufacturing, offering substantial benefits in terms of precision, safety, and efficiency. As industries continue to evolve, the adoption of such advanced technologies will be critical in maintaining competitive edges and meeting the demands of quality, speed, and flexibility in production. The future of manufacturing bends towards innovation, and robotic press brakes are at the forefront of this curve.
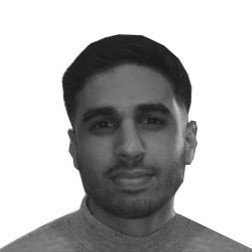
Hassan graduated with a Master’s degree in Chemical Engineering from the University of Chester (UK). He currently works as a design engineering consultant for one of the largest engineering firms in the world along with being an associate member of the Institute of Chemical Engineers (IChemE).