What Is Aircraft Fuel Inerting?
Aircraft bleed air is the source for the inerting gas that is used to inert the fuel tank. The bleed air is compressed air taken for the from high or low engine compressor stages of the gas turbine upstream of the fuel-burning stage (Figure 1) (Airbus, 2018). Upon exit of the compressor, the bleed air is at a pressure of 40 PSI and temperature of 200-250, due to this high temperature the bleed air needs cooling down, this is done by using compression and expansion turbines or air-cooled heat exchangers to reduce the temperature, as it is far too hot for the cabin and in the fuel inerting system if the bleed air was introduced at 200-250 degrees, it would cause the fuel to burn in the fuel tank and damage the fuel tank (Skybrary, 2019).
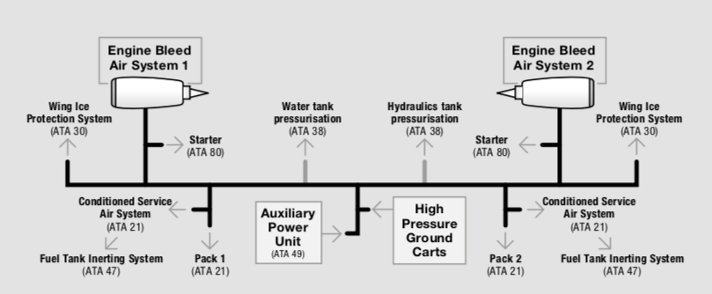
Issues With Bleed Air
Bleed air isn’t without its issues, cases of bleed air leakage are rare and are considered abnormal in the aviation industry. The major threat of bleed air is the risk of a leak of which can lead to overheating, a loss of system functions, melting of aircraft components, the release of emissions of ozone and other gases in the bleed air stream lead to environmental damage (Shao, 2018), noxious fumes can be released into the cabin and a fire could break out (AOPA, 2011). Furthermore, the high demand for Nitrogen needed from the bleed air which can cause strain on the bleed air system due to the need for maintaining ullage oxygen concentration below 12%.
Fuel Weight Penalty
The uses of bleed air for fuel inerting leads to a large fuel weight penalty. Fuel weight penalties are factors that influence an aircraft’s performance due to added weight, external and momentum drag and performance changes (SAE International, 2004). The issues with using bleed air are high demand of bleed air required to inert the fuel tank which requires the engines to draw in more air which puts more stress on smaller aircraft that have smaller engines and struggle to draw in enough air which leads to greater fuel consumption. Also, with the components of the OBIGGS such as heat exchanges, valves and pipework, this adds weight and requires greater fuel consumption which adds to flying costs for airliners.
The bleed air required to inert the fuel tank changes at different stages of an aircraft’s flight, the stages are; low for climbing and cruising, medium in approach and high in descent (Airbus, 2009). During high and medium phases, the requirement for bleed air is large and this puts a huge strain on an aircraft bleed air system with smaller aircraft struggling much more than larger aircraft due to their smaller bleed air systems, these high bleed air demands require more fuel to be consumed to meet the requirements for inerting which cause a fuel weight penalty (Moir, 2020).
Inerting Methods
The methods used to inert a fuel tank are one of two methods; ullage washing and fuel scrubbing (Federal Aviation Administration, 1998).
- Ullage washing involves injecting an inert gas usually Nitrogen into the ullage of the fuel tank, which displaces the oxygen in the ullage space.
- Fuel scrubbing comprises of small inert gas bubbles being sent into the bottom of the fuel tank and rising to the top and displacing the dissolved oxygen with the dissolved oxygen being removed and dissolved Nitrogen being added which reduces the concentration of oxygen that is in the ullage (Administration, Fuel Tank Protection, 2019).
Inerting Technologies
Several fuel inerting technologies that are not suitable for commercial aircraft, such as; the Halon Extinguishing System is very expensive, Explosive Resistant Foam adds a lot of weight leading to a fuel weight penalty and Liquid Nitrogen System that requires frequent resupplying and has logistical issues (Yan, 2014). A breakthrough was perceived when OBIGGS was developed which is cheaper than the other inerting technologies and was lightweight, doesn’t have any major logistical issues, requires few moving parts, is highly reliable (Shao, 2018), don’t require pre-flight or post flights checks and can be monitored by aircraft crew by onboard computers (Figure 2) (Smith, 2014).
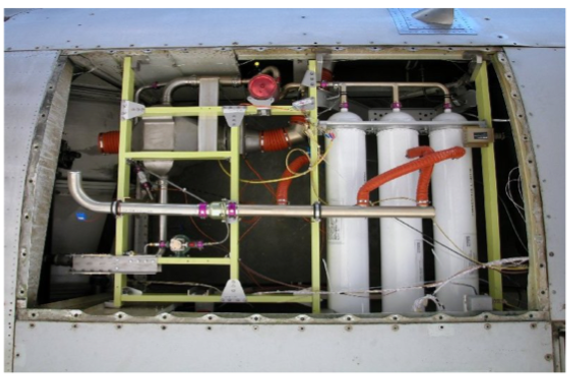
OBIGGS
The OBIGGS system works by inerting the fuel tank with Nitrogen-enriched air (NEA) which is 90-98% pure Nitrogen (Figure 3) (Burns, 2004) and reduces the risk of the oxygen concentration rising above 12% which is the upper limit imposed by the FAA for civilian aircraft for ullage oxygen concentration, as any higher oxygen concertation can lead to combustion and by removing one part of the fire triangle which is an oxygen supply no combustion can occur thus no explosion can occur. The inert gas is produced from the aircraft bleed air and ASM that contains hollow fibre membranes (Figure 4) (Smith, 2014) that separate the Nitrogen which is used to inert the fuel tank (Yan, 2014).
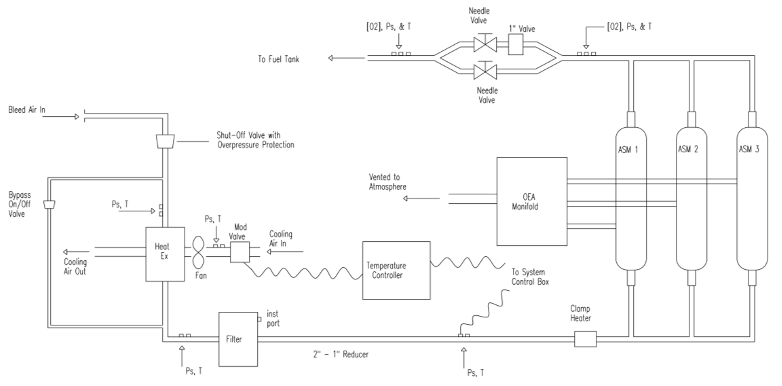
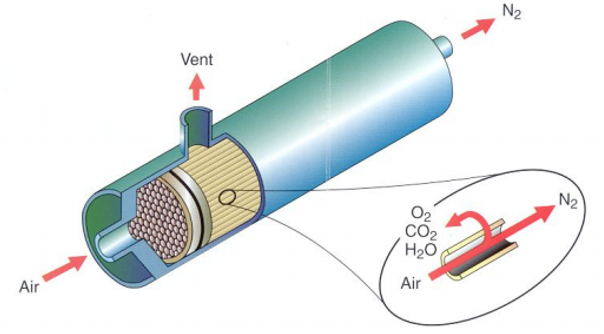
References
Administration, F. A. (2019). Fuel Tank Protection. Retrieved from Federal Aviation Administration: https://www.fire.tc.faa.gov/Systems/FuelTank/Ullage
AOPA. (2011, March 1). SYSTEM SYNOPSIS: BLEED AIR MALFUNCTIONS KNOWING WHAT TO DO WHEN HOT BLEED AIR BECOMES TOO HOT. Retrieved from AOPA: https://www.aopa.org/news-and-media/all-news/2011/march/01/system-synopsis-bleed-air-malfunctions
Federal Aviation Administration. (1998). Fuel Tank Inerting. Atlantic City: Federal Aviation Administration.
Moir, A. S. (2020). Design and Development of Aircraft Systems Third Edition . Chichester: Wiley.
Smith, D. E. (2014). FUEL TANK INERTING SYSTEMS FOR CIVIL AIRCRAFT. Retrieved from mountainscholar: https://mountainscholar.org/bitstream/handle/10217/88618/Smith_David_colostate_0053N_12699_rev.pdf?sequence=1
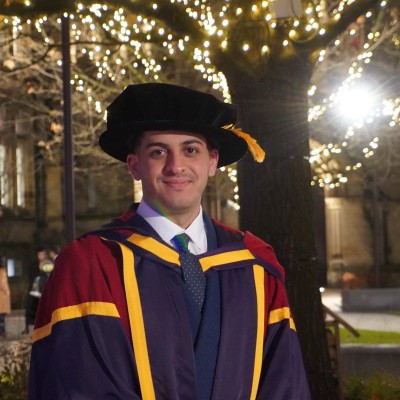
Dr. Adam Zaidi, PhD, is a researcher at The University of Manchester (UK). His doctoral research focuses on reducing carbon dioxide emissions in hydrogen production processes. Adam’s expertise includes process scale-up and material development.’