For Part 1 and Part 3 click here
Why Are Process Layouts Important?
A process layout refers to the positioning of the different processes relative to each other and how the various tasks are undertaken, and the resources required. Having the correct type of process layout will result in a more efficient manufacturing process and more importantly make the process safer by minimizing the flow through the operation, keeping staff away from the noisy or unpleasant area, making equipment accessible, appropriate use of space, and allow for long term flexibility.
Types Of Process Layout
Four basic layout types correspond to a different manufacturing process type, these are:
- Fixed-Position Layout,
- Process/Functional Layout,
- Product (Line) Layout,
- Cell Layout (figure 1 and 2)
(see An Overview of Manufacturing Part 1 – Categories Of Products And Manufacturing Process Types For Information On Manufacturing Process Types).
Figure 1: Relationship between process type and layout type (Bracciotti, 2017).
Figure 2: A restaurant showing all 4 basic process types (Weeks, 2015).
Fixed Position
Transformed resources do not move between transforming resources, this means that the product the process is producing is in a fixed stationary position and the resources such as people, equipment and machinery go to the product, so you can say the resources ‘flow through the operation (figure 3).’ A fixed position is ideal for large, heavy, or fragile products that are too difficult to move such as a fighter jet.
Advantages are; high product flexibility and product variability, product or customer not moved or disturbed and a high variety of staff tasks.
Disadvantages are; very high unit costs, activity and space scheduling can be challenging and more movement of plant and staff takes up time (Slack et al, 2010).
Figure 3: Example of a fixed position process layout (Molla, 2018).
Process/Functional Layout
Similar resources are grouped, either due to connivance or because having the resources together is more efficient, or because the utilization of the resources is improved. The flow pattern is normally complex with the product flowing through the process going from one stage to the next stage such as different departments, and if different products are being produced then different routes would be taken (figure 4). Process/functional layout is used mainly for making custom products that have low demand such as the price of custom furniture.
Advantages are; high product flexibility and product variability, robust in case of disturbances, and easy supervision of the process.
Disadvantages are; low facility utilization, high work-in-progress or customer queuing which can lead to backlogging issues and complex flow can be difficult to control and require full-time expert which adds to costs (Slack et al, 2010).
Figure 4: Example of process/functional layout (Molla, 2018).
Product Layout
The transforming resource is located for the convivence of the transformed resource. This means that each product follows a prearranged route with the activity sequence being carried out matches the process sequence (figure 5). The transformed resources flow along a line of process, this results in a predictable and clear flow process that is easy to control. Product layout is used for high volume goods such as garment factory.
Advantages are; low unit costs for high volume, the opportunity for the specialization of equipment, and convenient movement of goods and customers.
Disadvantages are; Low mix flexibility, not robust in case of disturbances and work is repetitive and can lead to a lack of motivation of the workforce (Slack et al, 2010).
Figure 5: Example of product layout (Molla, 2018).
Cell Layout
Cell layout (also referred to as cellular layout) is a type of layout where machines are grouped according to the requirement for a set of items that require similar processing, these groups are called cells (Inman, 2007). Transformed resources that enter the operation are pre-elected (or select themselves) and move to one part of the operation or cell, in which all the transforming resources are located for immediate processing (figure 6). Furthermore, a cell can be arranged in a functional/process or product format, and transformed resources after being processed in a cell can go to another cell if desired. Cell layout gives companies the capability of building a variety of products and minimizing their waste, with an example being
Advantages are; compromise between cost and flexibility, high variety operations, fast throughout and group work can be a source of motivation for the workforce.
Disadvantages are; costly to rearrange the current layout, need a lot more equipment which adds to costs and in some scenarios can give lower plant utilization (Slack et al, 2010).
Figure 6: Example of cell layout (Scribd, 2015).
References
Bracciotti, M. (2017). OPERATIONAL MANAGEMENT STUDY. Retrieved from Research Gate: https://www.researchgate.net/publication/318858943_OPERATIONAL_MANAGEMENT_STUDY
Inman, R. A. (2007). LAYOUT. Retrieved from References for Business: https://www.referenceforbusiness.com/management/Int-Loc/Layout.html
Molla, R. S. (2018, May). A study on Manufacturing of Deformed Bar (G 60-400W) at Elite Iron and Steel Industries. Retrieved from Research Gate: https://www.researchgate.net/publication/325178996_A_study_on_Manufacturing_of_Deformed_Bar_G_60-400W_at_Elite_Iron_and_Steel_Industries
Scribd. (2015, November 7). Cellular manufacturing. Retrieved from slide share: https://www.slideshare.net/ananya0122/cellular-manufacturing-54853711
Slack, Chambers, S and Johnston, R (2009), Operations Management. Pearson Education ebooks
Weeks, B. (2015, August 31). 07 layout and flow_Operations Management. Retrieved from slide share: https://www.slideshare.net/brentaweeks/07-layout-and-flowoperations-management
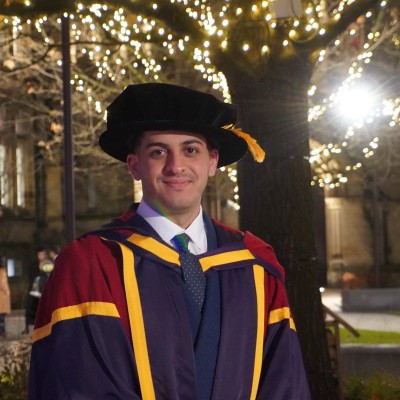
Dr. Adam Zaidi, PhD, is a researcher at The University of Manchester (UK). His doctoral research focuses on reducing carbon dioxide emissions in hydrogen production processes. Adam’s expertise includes process scale-up and material development.’