Key Takeaways
– Fiberglass springs are a type of spring made from fiberglass material.
– They offer several advantages over traditional metal springs, including lightweight, corrosion resistance, and high strength.
– Fiberglass springs are commonly used in various industries, such as automotive, aerospace, and sports equipment.
– The manufacturing process of fiberglass springs involves the use of fiberglass strands and resin to create a strong and flexible composite material.
– Proper maintenance and care are essential to ensure the longevity and performance of fiberglass springs.
Introduction
Springs are an essential component in many mechanical systems, providing support, cushioning, and flexibility. Traditionally, springs have been made from metal materials such as steel or bronze. However, with advancements in technology and materials, fiberglass springs have emerged as a viable alternative. In this article, we will explore the world of fiberglass springs, their advantages, applications, and the manufacturing process behind them.
Advantages of Fiberglass Springs
Fiberglass springs offer several advantages over their metal counterparts. One of the key benefits is their lightweight nature. Fiberglass is a composite material made from glass fibers and resin, resulting in a significantly lighter spring compared to metal springs. This weight reduction can have a positive impact on various applications, such as automotive and aerospace industries, where reducing overall weight is crucial for fuel efficiency and performance.
Another advantage of fiberglass springs is their corrosion resistance. Unlike metal springs, fiberglass springs are not susceptible to rust or corrosion, making them ideal for outdoor or marine applications. This corrosion resistance ensures the longevity and durability of the springs, even in harsh environments.
In addition to being lightweight and corrosion-resistant, fiberglass springs also offer high strength. The composite nature of fiberglass allows for a combination of flexibility and strength, making them suitable for applications that require both. This strength is particularly beneficial in industries such as sports equipment, where fiberglass springs are used in various sporting goods like tennis rackets and archery bows.
Applications of Fiberglass Springs
Fiberglass springs find applications in a wide range of industries. One of the most common uses is in the automotive industry, where they are used in suspension systems. The lightweight nature of fiberglass springs helps reduce the overall weight of the vehicle, improving fuel efficiency and handling. Additionally, their corrosion resistance ensures a longer lifespan, reducing maintenance costs.
The aerospace industry also benefits from the use of fiberglass springs. They are used in aircraft landing gear systems, providing shock absorption and support during takeoff and landing. The lightweight and high strength properties of fiberglass springs contribute to the overall performance and safety of the aircraft.
Sports equipment manufacturers have also embraced fiberglass springs in their products. Tennis rackets, for example, utilize fiberglass springs in the form of composite frames, providing a balance of flexibility and strength for optimal performance on the court. Archery bows also benefit from fiberglass springs, offering improved accuracy and power.
Apart from automotive, aerospace, and sports equipment, fiberglass springs are used in various other applications. These include industrial machinery, marine equipment, and even furniture manufacturing. The versatility of fiberglass springs makes them a popular choice across different industries.
Manufacturing Process of Fiberglass Springs
The manufacturing process of fiberglass springs involves several steps to create a strong and flexible composite material. It starts with the selection of high-quality fiberglass strands, which are typically made from glass fibers coated with a protective resin. These strands are then woven together to form a mat or fabric.
Next, the fiberglass fabric is impregnated with a resin, typically epoxy or polyester, to create a composite material. The resin acts as a binding agent, holding the fiberglass strands together and providing additional strength. The impregnated fabric is then shaped into the desired spring form using molds or other shaping techniques.
Once the spring shape is achieved, the composite material is cured or hardened through a process called polymerization. This process involves subjecting the spring to heat or ultraviolet light, allowing the resin to fully cure and bond with the fiberglass strands. The resulting fiberglass spring is then trimmed, finished, and inspected for quality control.
Conclusion
Fiberglass springs offer a range of advantages over traditional metal springs, making them a popular choice in various industries. Their lightweight nature, corrosion resistance, and high strength properties make them ideal for applications where weight reduction, durability, and performance are crucial. From automotive suspension systems to aerospace landing gear and sports equipment, fiberglass springs have proven their worth. Understanding the manufacturing process behind fiberglass springs helps appreciate the intricate engineering and craftsmanship involved in creating these versatile components. Proper maintenance and care are essential to ensure the longevity and optimal performance of fiberglass springs, making them a reliable choice for many mechanical systems.
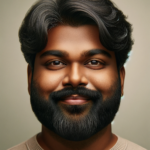
Adrian graduated with a Masters Degree (1st Class Honours) in Chemical Engineering from Chester University along with Harris. His master’s research aimed to develop a standardadised clean water oxygenation transfer procedure to test bubble diffusers that are currently used in the wastewater industry commercial market. He has also undergone placments in both US and China primarely focused within the R&D department and is an associate member of the Institute of Chemical Engineers (IChemE).